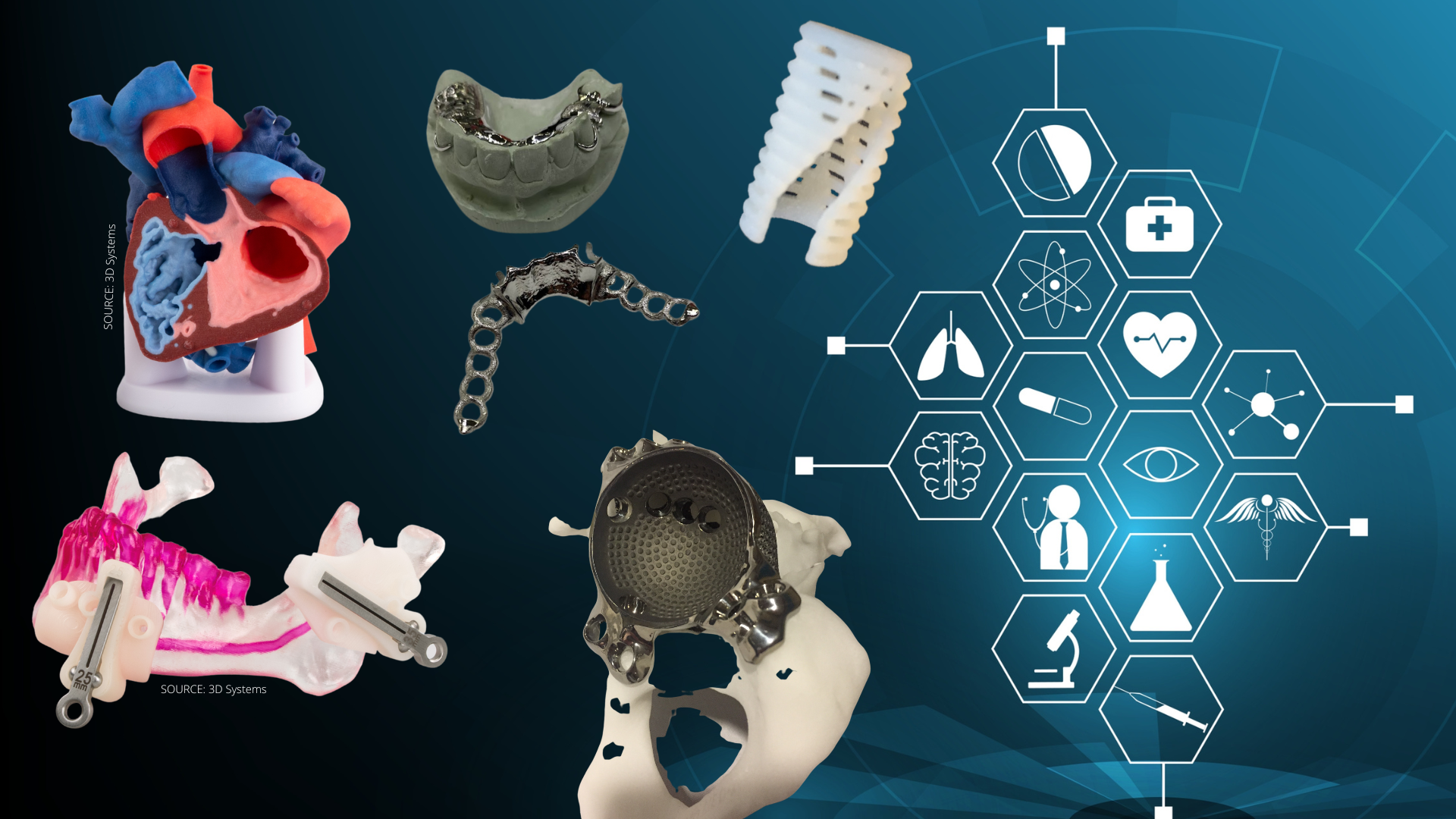
As physicians and other healthcare professionals work to advance patient care, becoming more personalized and precise, additive manufacturing has demonstrated to become an enabler. From the early days of the first commercial AM technology, stereolithography, the ability to use medical imaging to create patient care tools emerged.
In a recent survey of the medical AM community that included medical device manufacturers, hospitals (point-of-care manufacturers), dental labs, and more, 26% are already creating patient-matched devices with AM. While growth within the next year is expected in all application areas, patient-specific devices is the area for which largest number are expecting growth.
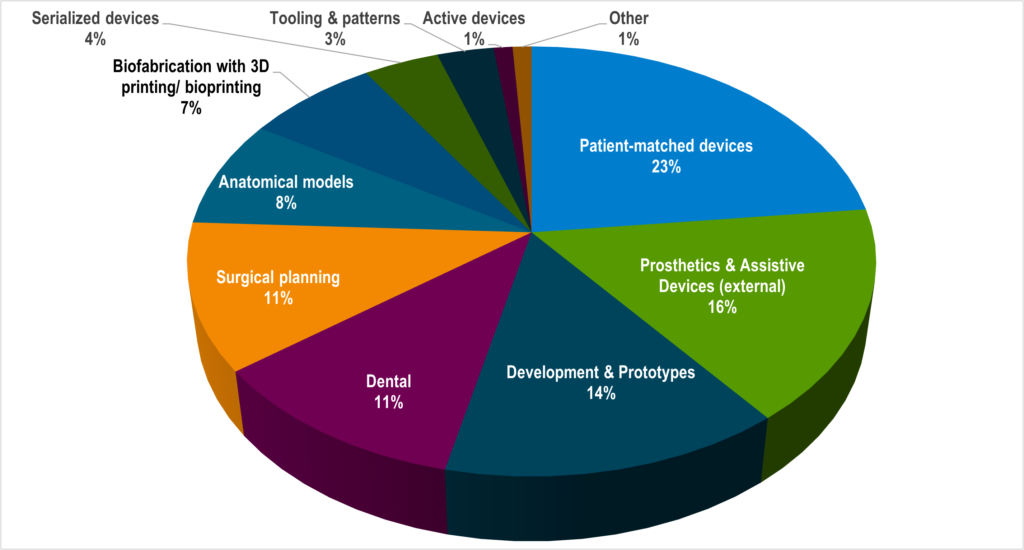
What are these patient-specific devices?
Building anatomic models were the earliest patient-specific applications, finding great value to help surgeons plan complicated surgeries like separations of conjoined twins as well as cranial maxillofacial reconstructions with symmetry and other aesthetic needs. Patient-specific devices have moved beyond earliest patient-matched tools were anatomic models. The next natural step for surgical planning was to create surgical guides for cutting and placement.
Applications that were already built specifically for an individual patient were quick to embrace AM and related technologies. The hearing aids are a great example. The first in-ear hearing aid cases were manufactured using AM in 2021. Within five years, AM became the industry standard for production with more than 99% of hearing aid cases being patient-matched and produced with AM today.
Hospitals or the point of care have been the center of patient-specific 3D printing for many years. In addition to create surgical planning and educational tools, hospitals have designed and built assistive devices and prosthetics. In the US, Walter Reed National Military Medical Center has been a leader in patient-specific devices including cranial implants to treat head injuries. They have also used the technology to improve a patient’s quality of life with assistive device that allow an amputee to hold a fishing rod or hockey stick.
Medical device manufacturers have not missed the patient-specific opportunity. Orthopedic implant manufacturers, in particular, have leveraged the complex design capabilities and porous structure production efficiencies to produce joint and spinal implants in standard sizes for several years. Adding value to their implants, many have taken the extra step to 3D print patient-specific surgical guides and instrumentation. Both Zimmer Biomet and DePuy Synthes have receive clearance from the FDA for these types of patient-specific tools.
What’s behind the growth expectations?
Patient-specific devices require several workflow improvements to reliably process medical imaging files, designing for additive manufacturing, processing, and selecting the optimal material all while meeting quality and regulatory compliance needs. As a primarily digital process, much of this workflow improvement has come from the software side. In 2019, there were only a handful of software packages specific to additive manufacturing. Today, that number is closer to 200 covering a range from generative design, build simulation, build planning, along with timing and cost estimates.
For medical applications, the initial processing of medical imaging files or segmentation has always been a bottleneck. In addition to more software options available, leading packages provide more tools to facilitate the segmentation process and have received FDA clearance to demonstrate reliability. Advancements in artificial intelligence (AI) are also pointing to a more streamlined processing and design process for patient-specific devices.
Find out more about medical personalization with 3D printing at the upcoming AM Medical Summit, November 1-3, 2022 in Minneapolis, Minnesota.