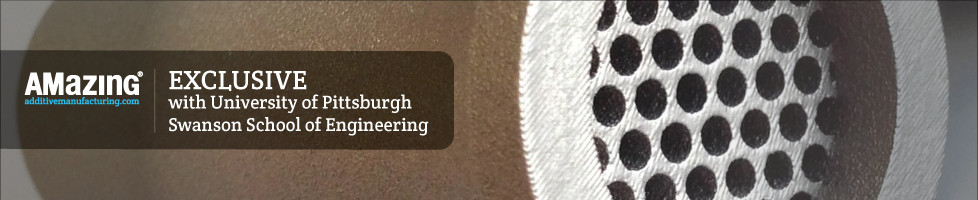
America Makes recently awarded a contract to the University of Pittsburgh for developing computational “latticework” for additive manufacturing (AM). The University of Pittsburgh will be in partnership with Acutec Precision Machining Inc, Alcoa Inc, ANSYS Inc and ExOne.
In an effort to gain a better understanding of computational “latticework” for additive manufacturing (AM), we connected with Albert To, PhD, assistant professor of mechanical engineering and materials science at University of Pittsburgh Swanson School of Engineering, to share his thoughts and observations in an AMazing® exclusive Q&A session.
—————————————
AMazing®: Thank you Dr. To for participating in this Q&A session. Before we begin our discussion of the research project, what was your first experience with additive manufacturing? Was it apparent at that time, that computational latticework would one day be needed?
Dr. To: My first experience with additive manufacturing occurred nine years ago when I had the opportunity to get involved in a selective laser melting project. It was not apparent to me at the time that lattice structures would one day be needed. Later on, I conducted research on lattice structures and foams and started to realize that there is a distinct advantage of using additive manufacturing (AM) to fabricate these structures.
AMazing®: What makes additive manufacturing ideal for developing cellular structures or latticework? By the way, are the terms cellular structure and latticework used interchangeably?
Dr. To:Because additive manufacturing builds parts layer-by-layer, very complex shaped geometries such as those of cellular structures can be fabricated. Cellular structure is a term that means a structure consists of cells (i.e. pores) which encompasses lattice structure and randomly-structured foams.
AMazing®: Is the scope of the project focused primarily on the development of software, that will allow the creation of lattice optimized CAD design (based upon an MRI or other) with FEA validation?
Dr. To: Yes, the focus is on development of efficient computational algorithm and software.

AMazing®: I would imagine the characteristics of latticework for a part will be dependent upon a number of variables such as weight, load requirements, stiffness and displacement. How will the behavior of the cellular structures be analyzed to produce an optimized part?
Dr. To: Good question. This depends on the objective of the design problem. In this project, we will focus on minimize stiffness for a given weight and load conditions as well as minimize weight while satisfying allowable stress and load requirements.
AMazing®: Will the research be limited to any particular materials or material conditions?
Dr. To: This project will be limited at several metal alloys including Ti-6Al-4V and plastics including ABS.
AMazing®: Will the research focus on single material parts? What about multi-material parts or multifunctional parts, additively manufactured in a single operation?
Dr. To: The research will focus on just single material parts, but with some modifications, the same computational algorithms developed can be applied to multi-material parts as well.
AMazing®: What types of additive manufacturing technologies will be used in the project?
Dr. To: These will include direct metal laser sintering, laser engineered net shaping (LENS), particle binding, and also stereolithography.
Amazing®: Topology optimization analysis analyzes the stresses on a shape; removing the unnecessary material. Is this a fair statement? What types of topology optimization tools are needed to conduct your research?
Dr. To: Yes, it is a fair statement. The topology optimization tools will be developed based on micromechanics models together with finite element analysis.
AMazing®: As research begins, what do you perceive as the major challenges facing the development of software for design and optimization of AM latticework?
Dr. To: One major challenge is to generate a computational model that can actually be fabricated by the different AM techniques.
AMazing®: We are avid supporters of education. If someone desires to work in the field of computational latticework, what types of skill sets and education are needed?
Dr. To: The person must have training in mechanics of materials, finite element analysis, and optimization methods.
AMazing®: Which commercial sections do you feel will benefit most from the research? How will small and mid-size businesses benefit from your research?
Dr. To: The aerospace industry will benefit the most because lattice structures are ideal for reducing weight while maintaining structural stability. This project actually involves a mid-size company in Acutec Precision Machining, whose customers include several aerospace companies.
AMazing®: Five (5) years from now, how will optimization of advanced AM cellular structures for design and manufacture have changed?
Dr. To: I fully expect that the computational technology for optimization of AM cellular structures will be commercialized and applied to design of parts and components in real applications.
AMazing®: This concludes our interview. Thank you very much Dr. To. We are grateful for your participation and bringing awareness of University of Pittsburgh Swanson School of Engineering’s commitment and advances to additive manufacturing technologies.
—————————————
About the Swanson School of Engineering
The University of Pittsburgh’s Swanson School of Engineering is one of the oldest engineering programs in the United States and is consistently ranked among the top 50 engineering programs nationally. The Swanson School has excelled in basic and applied research during the past decade and is on the forefront of 21st century technology including sustainability, energy systems, bioengineering, micro- and nanosystems, computational modeling, and advanced materials development.
Approximately 120 faculty members serve more than 2,600 undergraduate and graduate students and Ph.D. candidates in six departments, including Bioengineering, Chemical and Petroleum Engineering, Civil and Environmental Engineering, Electrical Engineering, Industrial Engineering, Mechanical Engineering, and Materials Science.
Contact:
Paul Kovach
Director of Marketing and Communications
Swanson School of Engineering, University of Pittsburgh
412-624-0265
pkovach@pitt.edu
About America Makes America Makes is the National Additive Manufacturing Innovation Institute. As the national accelerator for additive manufacturing (AM) and 3D printing (3DP), America Makes is the nation’s leading and collaborative partner in AM and 3DP technology research, discovery, creation, and innovation. Structured as a public-private partnership with member organizations from industry, academia, government, non-government agencies, and workforce and economic development resources, we are working together to innovate and accelerate AM and 3DP to increase our nation’s global manufacturing competitiveness. Based in Youngstown, Ohio,
America Makes is the pilot institute for up to 45 manufacturing innovation institutes and is driven by the National Center for Defense Manufacturing and Machining (NCDMM). For more information about America Makes, visit .
About NCDMM NCDMM delivers optimized manufacturing solutions that enhance the quality, affordability, maintainability, and rapid deployment of existing and yet-to-be developed defense systems. This is accomplished through collaboration with government, industry, and academic organizations to promote the implementation of best practices to key stakeholders through the development and delivery of disciplined training, advanced technologies, and methodologies.
NCDMM also manages the national accelerator for additive manufacturing (AM) and 3DP printing (3DP), America Makes – the National Additive Manufacturing Innovation Institute. For additional information, visit the NCDMM at www.ncdmm.org.
Republication or redistribution of AMazing content, including by framing or similar means, is expressly prohibited without the prior written consent of AMazing. AMazing and its logo are registered trademarks.