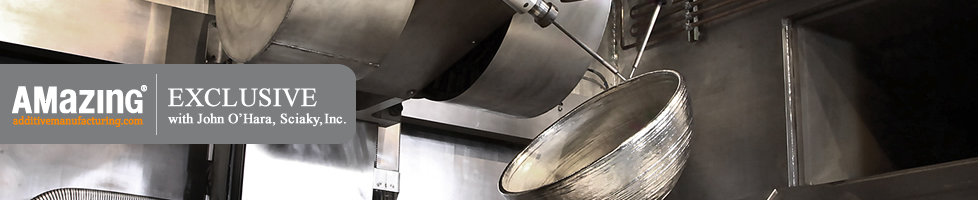
Sciaky, Inc., a subsidiary of Phillips Service Industries, Inc. (PSI), recently introduced an expanded lineup of Electron Beam Additive Manufacturing (EBAM) systems. The expanded lineup of EBAM systems provides new options for medium, large, and extra-large part applications. In addition to offering EBAM systems for purchase, Sciaky offers flexible additive manufacturing services for customers looking to produce a critical prototype part or a run of high-value production parts.
The company also provides electron beam and advanced arc welding systems, as well as job shop welding services for the aerospace, defense, automotive, healthcare and other manufacturing industries.
We caught up with John O’Hara, Global Sales Manager at Sciaky Inc. to learn about recent developments at Sciaky Inc. in an exclusive AMazing® Q&A conversation.
*****
AMazing®: John, thank you for your participation.This must be an exciting time for Sciaky, Inc. with the introduction of an expanded lineup of Electron Beam Additive Manufacturing (EBAM) systems, as well as new financing and lease options for customers that purchase EBAM systems. What prompted the need to expand Sciaky’s lineup of EBAM systems?
John O’Hara: We felt that a wide range of offerings was in the best interest of the customer base. This will allow each customer to “right-size” their system for the optimal balance of capability and efficiency. Customers who will only run small size parts will not want the cost and floors space consumption of a larger machine. Customers who suspect they may want to produce large parts now, or in the future, may regret acquiring a chamber too small for their needs. The range of options allows each customer to choose the right solution to suit their specific needs.
AMazing®: In an earlier press release, we learn Sciaky’s EBAM technology is the most widely scalable metal 3D printing solution on the market with the fastest deposition process. How does Electron Beam Additive Manufacturing (EBAM) technology work?
John O’Hara: Electron Beam Additive Manufacturing uses an electron beam as the directed energy source. This beam is focused onto a metal substrate (a plate of metal, the outer diameter of a round shaft or the surface of an existing metal structure). The beam will create a pool of liquid metal while the wire feedstock is fed into the path of the beam. The beam will melt the wire, adding additional metal to the liquid pool. The beam will then move along the substrate, leaving behind a new layer of solidifying metal. The overall shape of the additively manufactured part is created in this manner, layer by layer.

During this deposition process, a suite of sensors continually monitor the important measureable parameters in the process. This data will be used to modify the inputs to the process in real-time. This continuous monitoring and updating of the inputs will ensure that every ounce of metal deposited will have the same experience in transitioning from wire feedstock, through melting, and then through solidification. This process gives part designers and manufacturers consistency in the resulting geometry, microstructure, and chemistry of the deposited metal.
AMazing®: As we understand EBAM can produce large-scale metal structures from high-value metals up to 19 ft. in length or round parts up to 96 inches in a few days. From a time and cost standpoint, how does large-scale metal EBAM compare against the production of large-scale forgings and castings?
John O’Hara: Production of parts is only limited by the availability of the very simple and basic inputs – wire and the substrate plate or rod onto which the metal is deposited. These inputs are standards, meaning that the same plate and wire will be used to make many different parts. This allows a manufacturer to stock these inputs, or at the very least, allows for a quick delivery.

The other inputs are production availability of the EBAM machine and the software designs of the deposited parts. Once these major inputs are in place, which can be as little as several hours with the right planning, the deposition can start. The actual time to deposit the metal will vary from minutes to hours depending on the size, geometry, and materials used. In the best cases, a manufacturer could produce a small part within a few hours or a very large part over the course of a few days.
Manufacturers of castings and forgings, on the other hand, have to wait for the tooling to be made before the raw metal can be forged or cast. This can range from months to potentially longer than a year in some cases. So, in a nutshell, it’s easy to see that there is significant time and cost savings with the EBAM process as compared to the turnaround time of forgings and castings.
AMazing®: The use of additive technologies to repair high valued metal parts is exciting. Can EBAM technology be used to repair parts? What are some examples of high valued parts that would benefit from using EBAM for repair purposes? How does the repaired section compare to the substrate in terms of material composition and mechanical properties?
John O’Hara: Part repair is a particularly interesting capability of EBAM. While the repair of fine features in precision-made parts is being well served by other metal AM technologies, we believe the repair of large features on large structures is very well suited to EBAM. As with any repair process, the heat input to the repaired metal will be a concern, especially in hardened alloys. Sciaky’s EBAM can be scaled to lower deposition rates (if required), while still allowing the repairs to be done to large structures. The hard vacuum environment also allows the added metal to be deposited without the worry of contamination from gasses in the environment.
AMazing®: What types of metals can be used with EBAM technology to build prototypes, metal parts or support repair work?
John O’Hara: Some of the most unusual metals include the pure refractory metals and alloys of Tungsten, Niobium, Tantalum, Rhenium, and Molybdenum. Electron beam directed energy deposition is a very efficient method of melting metal, and the full power of the beam (up to 42 KiloWatts) will not have trouble with high melting-point metals. Many other superalloys can be deposited with EBAM – the only rules are that it is a weldable metal and that is available in wire feedstock.
AMazing®: In addition to EBAM technology, what other products and services does Sciaky provide to industry?
John O’Hara: Sciaky has a deep history (dating back to the 1930’s) of supplying high-end welding systems to industries like Aerospace, Oil/Gas Exploration, Industrial uses and nuclear. Today, Sciaky continues to supply welding systems and services in addition to the Additive Manufacturing systems. The product line consists mostly of Electron Beam Welding systems and robotic arc welding systems. Sciaky can offer standardized or customized systems to suit user needs. At the Chicago headquarters, Sciaky operates a fleet of systems available for contract services in EBAM, EB welding, and Arc Welding.

AMazing®: As the additive manufacturing industry evolves over the next several years, how will Sciaky’s EBAM systems evolve to meet the growing needs of industry?
John O’Hara: Sciaky’s EBAM technology will continue to evolve to meet the growing needs of industry. Efforts are currently underway to improve the geometric consistency and fine detail features of the deposits. AM users will benefit from producing parts closer to net shape – and this will continue to be our goal.
Sciaky will also continue to expand the current set of alloys and geometries we can produce. We are constantly challenging ourselves to create new ways of applying the technology across multiple industries, alloys, and shapes. This continual cadence of development and refinement will benefit users for years to come.
AM users will also benefit from our continued research and cataloging of the metallic properties of parts produced with EBAM. This will be an enormous amount of data, yet designers will benefit immensely from design guidelines. Sciaky is planning partnerships and internal efforts to produce this data to help the industry take full advantage of the EBAM technology.
Video courtesy of Sciaky Inc.
This concludes our interview. Thank you very much John for your participation. We are very grateful for the opportunity to learn about Sciaky’s products and services and ongoing commitment to additive technologies.
*****
About John O’Hara
John O’Hara spent the first 22 years of his career in the world of Assembly Automation at Cox Automation Systems, today called ixmation North America.

Starting out in the metal shop, then working through Machine Design, Project Management, Applications Engineering and eventually leading the Sales and Marketing Group. During this time John worked closely with customers and internal resources to develop custom high-tech assembly and test solutions.
In 2013, John joined Sciaky, Inc., a subsidiary of Phillips Service Industries, Inc., as a Sales Manager, and in 2014 assumed the role of Global Sales Manager. This position has him dealing directly with Designers, Engineers, and Executives to solve difficult production problems with Electron Beam Welding (EBW) and Electron Beam Additive Manufacturing (EBAM) solutions.
John spends the rest of his time at Sciaky building a Global Sales Force of direct, indirect and contract local resources. During his tenure, John has led the transition of Sciaky’s revenues from primarily welding equipment to a mostly Additive Manufacturing services and equipment.
About EBAM:
Sciaky’s Electron Beam Additive Manufacturing (EBAM) is a one-of-a-kind 3D printing technology that excels at producing large-scale, high-value metal parts. As opposed to forgings, which typically have lead times of 6+ months, EBAM can produce high quality, large-scale metal structures, more than 20 feet in length, made of metals like titanium, tantalum, and nickel-based alloys in a matter of hours or days, with very little material waste.
While 3D printing large, high-value metal parts is Sciaky’s specialty, the EBAM process is equally effective for 3D printing small metal parts (with features as fine as 1mm). EBAM systems can be used in any phase of the product life cycle: from rapid prototypes and production parts to repair and remanufacturing applications.
About Sciaky, Inc.
Sciaky, Inc., a subsidiary of Phillips Service Industries, provides industry-leading metal 3D printing systems and services. Our exclusive Electron Beam Additive Manufacturing (EBAM) process is the fastest, most cost-effective metal 3D printing process in the market, allowing manufacturers to save significant time and money over traditional manufacturing and prototyping processes.
Sciaky also provides best-in-class electron beam and advanced arc welding systems, as well as flexible job shop welding services, for the aerospace, defense, automotive, healthcare and other manufacturing industries. Our welding equipment meets rigid military specifications to manufacture items such as airframes, landing gear, jet engines, guided missiles and vehicle parts.
For more information on Sciaky, visit www.sciaky.com. You can also follow Sciaky on Twitter, Facebook, Google+, YouTube and LinkedIn.
About Phillips Service Industries, Inc.
Established in 1967, Phillips Service Industries, Inc. (PSI) is a privately-held global manufacturing and services holding company, which oversees a diverse collection of innovative subsidiaries: Beaver Aerospace & Defense, Inc., Evana Automation Specialists, Mountain Secure Systems, POWERTHRU, PSI Repair Services, Inc., PSI Semicon Services, Sciaky, Inc., and Skytronics, Inc.
We serve a wide range of high-tech industries like aerospace, defense, automotive, alternative energy, healthcare, security and semiconductor. Our award-winning products and services help reduce costs and maximize efficiency for many Fortune 500 companies around the globe, as well as the U.S. Military. We push the boundaries of technology on critical programs like Homeland Security, Defense research and space exploration, delivering innovative solutions for land, sea, air and space. We’re PSI: Always innovating. Everywhere.™
Contacts
John O’Hara
Global Sales Manager
Sciaky, Inc.
4915 W. 67th Street
Chicago, Il 60638 USA
Cell: (312) 459-6849
Fax: (708) 594-9213
Jay Hollingsworth
Public Relations Manager
Phillips Service Industries, Inc.
734.853.5211 direct
jay.hollingsworth@psi-corp.com
(Top photo)-Courtesy of Sciaky Inc.
Republication or redistribution of AMazing content, including by framing or similar means, is expressly prohibited without the prior written consent of AMazing. AMazing® is a registered trademark of Amazing.