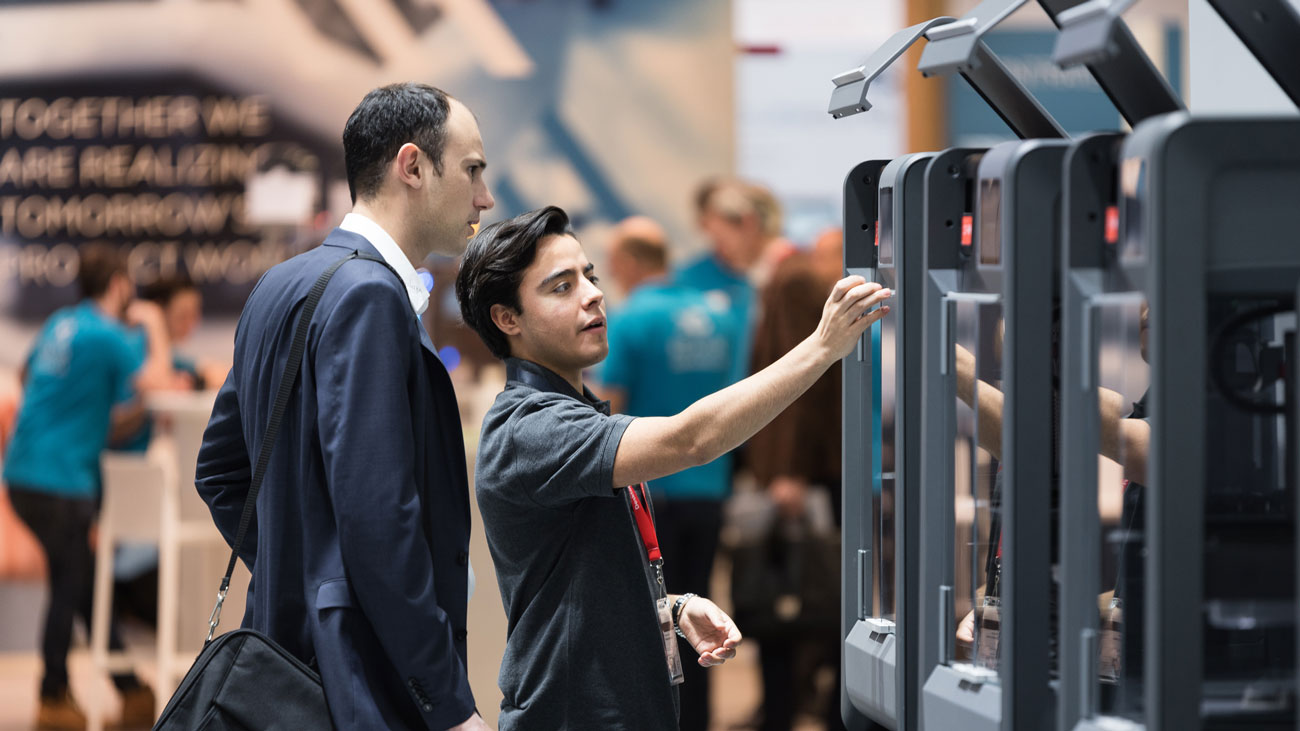
At this year’s formnext in Frankfurt AM Solutions – 3D post processing technology is presenting not one but three trend setting machines. The new S1 Wet was specifically developed for the removal of residual powder and the surface homogenization and smoothing of metallic 3D components. With the S2 the experts for automated post processing solutions are presenting the first shot blast machine for treating 3D printed components made from polymers in indexing, continuous flow mode. Of particular interest will be the C2 system that allows the chemical surface smoothing and application of a color dye in one single machine.
The increasing utilization of additive manufacturing for volume production of standard components goes hand-in-hand with increasing demands for quality, consistency and cost efficiency of the post processing and surface refinement operations for 3D printed components. For this purpose AM Solutions – 3D post processing technology, the division of Rösler Oberflächentechnik GmbH that specializes in automated post processing and surface finishing solutions, presents various innovative developments at this year’s formnext (hall 12, booth C 119). The new systems were specifically developed for volume production of 3D printed components made from metal and plastic.
Consistent de-powdering, surface homogenization and smoothing of metal components
One of these developments is the wet blast machine S1 Wet that was specifically developed for post processing 3D printed components made from metal. Besides the removal of residual powder, the compact plug and play system also allows the surface homogenization and smoothing. Depending on the surface roughness of the raw components, the S1 Wet can produce low Ra values. To a certain extent, this is even possible on the surface areas of internal passages and / or cavities. The wet process prevents small metal particles removed from the work pieces, dust and shavings from creating a combustible or explosive mixture. Therefore, it does not require the installation of protective ATEX accessories. The water layer created on the part’s surface prevents from abrasive media inclusions. As an option, an integrated waste water recycling system consistently removes any contaminants from the slurry consisting of blast media and water limiting the water consumption. The S1 Wet system can be used for a variety of post processing tasks ranging from the manual processing of single components to fully automatic batch operation.
Efficient post processing in indexing continuous flow mode
Placing entire batches of plastic components, produced with powder-bed printing systems, into a machine, selecting the respective processing program, and everything else running fully automatically. With its new ATEX compliant S2 shot blast machine, AM Solutions – 3D post processing technology is fulfilling this demand for effective, time- and personnel-saving post processing with repeatable results. After being placed in the machine, the work pieces are gently passing through a special troughed belt in single-piece flow. This allows the complete removal of any residual powder. Depending on the utilized blast media, the work piece surface can also be homogenized or peened. The blast media cleaning and recycling system, integrated into the plug and play system, is a major reason for achieving absolutely clean and repeatable results. It ensures that the blast media remains at a consistently high quality. A patent application covering the machine and the process is pending.
Eco-friendly chemical surface smoothing and application of a dye in one single machine
The design of the C2, presented at formnext as a concept solution, is based on Rösler’s comprehensive knowhow in the fields of equipment building and consumables. The innovative C2 system (pending patent application) allows the fully automatic chemical surface smoothing of 3D printed components made of common polymers and elastomers (including TPU) in series. Thus, the costly single piece handling of the work pieces is completely eliminated for this post processing operation. In addition, a future, retrofittable update will also allow the application of a color dye on the work pieces.
Of particular interest is that the non-hazardous processing media, developed by AM Solutions – 3D post processing technology, permits the eco-friendly chemical surface smoothing so that the spent media can be easily disposed of without any environmental restrictions. The new C2 will be available commercially in the first quarter of 2022.
AM Solutions – 3D post processing technology at the formnext, hall 12, booth C119.
About
For over 80 years, the privately owned Rösler Oberflächentechnik GmbH has been actively engaged in the field of surface preparation and surface finishing. As global market leader, we offer a comprehensive portfolio of equipment, consumables and services around the mass finishing and shot blasting technologies for a wide spectrum of different industries. Our range of about 15,000 consumables, developed in our Customer Experience Centers and laboratories located all over the world, specifically serves our customers for resolving their individual finishing needs. Under the brand name AM Solutions, we offer numerous equipment solutions and services in the area of additive manufacturing/3D printing. Last-but-not-least, as our central training center the Rösler Academy offers practical, hands-on seminars to the subjects mass finishing and shot blasting, lean management and additive manufacturing. Besides the German manufacturing locations in Untermerzbach/Memmelsdorf and Bad Staffelstein/Hausen the Rösler group has a global network of 15 manufacturing/sales branches and 150 sales agents.
For more information, please go to: www.rosler.com
Media Contact
Daniel Hund
+49 9533 924-802
d.hund@rosler.com