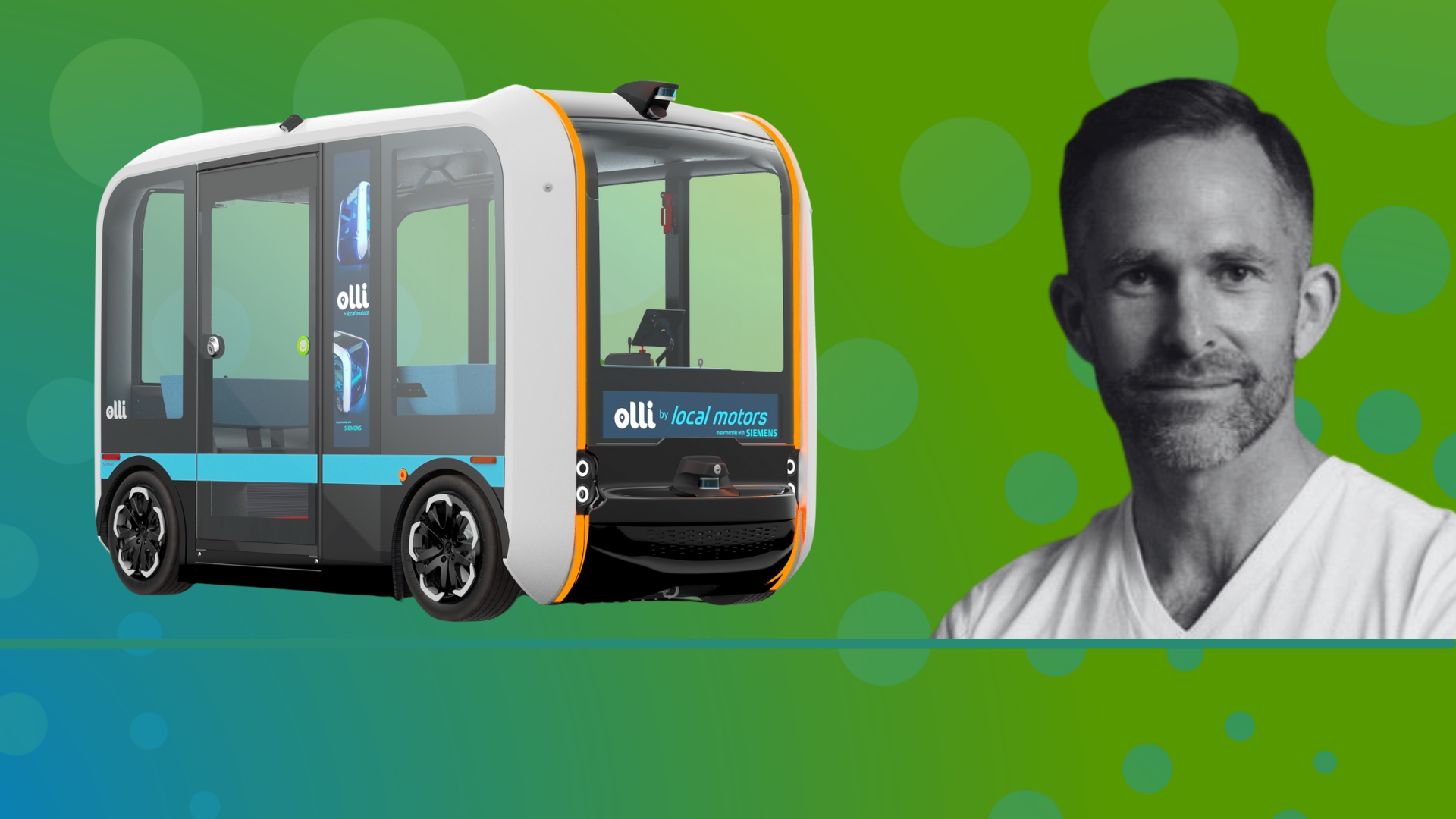
With automotive and aerospace developing more electrical and autonomous vehicles, does additive manufacturing have a role? Is it an enabler to producing EVs and AVs? As the founder of LM Industries, John (Jay) Rogers has explored options to create products that haven’t been seen before. We discussed many topics with Jay to gain his perspective and how AM is helping to accelerate the advancement of EVs and AVs.
Q1: What are some of the challenges in manufacturing for EVs and autonomous vehicles. What are some of the overall challenges that are faced?
JAY: As you move to making vehicles, it goes back to that head-scratcher, which is, how industrial is the method? How fast is it? How reliable is it? How does it meet with your ESG (Environmental, Social, Governance) sustainability goals? And is it something that we can model and understand, a process that we can put into a factory? Those are some of the big challenges when you’re making it and making things, and of course the end result. I think, almost logically, it has to be a different design system too, because it’s using a different method with different material properties.
Q2: What are some of the ways you can see additive manufacturing helping with EVs and AVs, or can potentially support a streamlined process for production of vehicles?
JAY: I think one of the things you’re seeing right away is the ability to be able to scale the type of product, or look at the scale of the type of product that you’re making. We work on the structure of the vehicle. We’ve got a lot of size and therefore a lot of material. What we have seen is that the tooling is very expensive, typically several hundred million dollars to do all the tooling and design it, make it, and then refurbish it for making a vehicle system. We see the improvement in that the large scale hybrid additive and subtractive and assembly system that we use reduces the cost of tooling effectively to zero.
Q3: What kind of additive process are you using? Polymers and metals or any other materials?
JAY: We started with the structure. That meant that the body of white married to the panels in the vehicle, married to any other substructures that were used for absorption of crash energy or increase in performance of the vehicle. It also includes certain things like seating positions, or structures, or other things like that that are in the vehicle, and dashboards, and other things that get added into a vehicle as a sub system afterwards. At the beginning, we didn’t know whether we would be able to use multiple materials or not, but we were focused on part count reduction and the decrease of cycle time and the decrease of making, and then the decrease of development time. We started following performance of materials, particularly, fiber reinforced polymers. The ability to use sustainably derived polymers, those that are either recyclable or those that are compostable, those that are bio derived, the nylon families that have the opportunity now for us to be plant-based nylons. The fiber allows you in a sense, to turn a knob that is a more refined knob than you typically can do with metals. However, in doing so it means that dissimilar materials or multi materials are really something that we need in the vehicle, because not everything should be made of the same polymer.
Q4: What are some of the unique things about AM and the electrification or autonomy that you have found that makes that this a good match?
JAY: Considering materials, it’s not just about a survivability, or crash energy absorption, or recyclability, I think also the performance of materials for deadening sound and for doing thermal absorption are factors. I think we hold out hope for pressure tropic materials that can get stiffer as they get impinged. There are other things like viral defense and bacterial defense that can be easily dropped into these materials. Material science for EVs is critical. You have a vehicle that is much quieter because you don’t have the rumble of an internal combustion engine. You also have a need for lightness. You also want to expose all the extra space you now have in the vehicle without an internal combustion engine and all of its supporting systems. When you’re using additive, you’re deleting interface areas where you’ve typically had fasteners and adhesives that can squeak, and this is a really nice feature. You also have the ability to control temperature in the vehicle. HVAC allows you not cool the entire cabin, but you can cool something which makes you feel cool. That’s your face, your neck, your seat. Additive gives you the opportunity to pipe air to those places. It gives you the ability to have certain thermal conductivity in materials, which allow you to be cooler in those areas.
Q5: What are some of the unique sensor needs that you’ve seen for autonomous or electric vehicles?
JAY: We have a traditional layup of inertial measurement units and accelerometers and encoders. Those are the ones that are sort of around the vehicle that you don’t see that tell you where the vehicle is going to be. Then you have the ability to put in really cool, very low cost sensors, like strain gauges, and other things like that that allow you to be able to measure the performance of the material as it’s living its life. That means that the sort of bones of the vehicle can report themselves and talk about how they’ve been used over the life of the vehicle. And then you have the ones that you often hear about more, which is the LiDAR, RADAR, visual cameras, and those sorts of things for pressure sensors, other things like that, ultrasonics in the movement of the vehicle. They need to be carefully positioned. Additive works very well to be able to do that. We believe that additive works well to get a lot of the bracketry and the potential for jitter and movement in those highly sensitive sensors out. Additive has allowed us to put our LiDAR into or inboard on a vehicle, behind glass, which means that those very expensive sub-components can be more survivable.
Q6: Talking about sensors, starts getting into printed electronics. Are you doing anything with printed electronics, and have you seen a printed superconductor?
JAY: If you can embed printing and you can get dissimilar parts out of the way you’re doing with structures, then you can have a better chance at survivability. If you have all this wall’s strength, using it for buses or harnesses, as opposed to just using it for the other needs of what a structure is, we see great applicability in that. There are also polymers that are self-healing, and so those are pretty exciting things that in printed electronics have been proven already. I see this as an opportunity there for really thinking about electronics.
UPDATE: After our discussion, Local Motors closed. John Rogers is working on exciting new projects we hope to hear about soon.