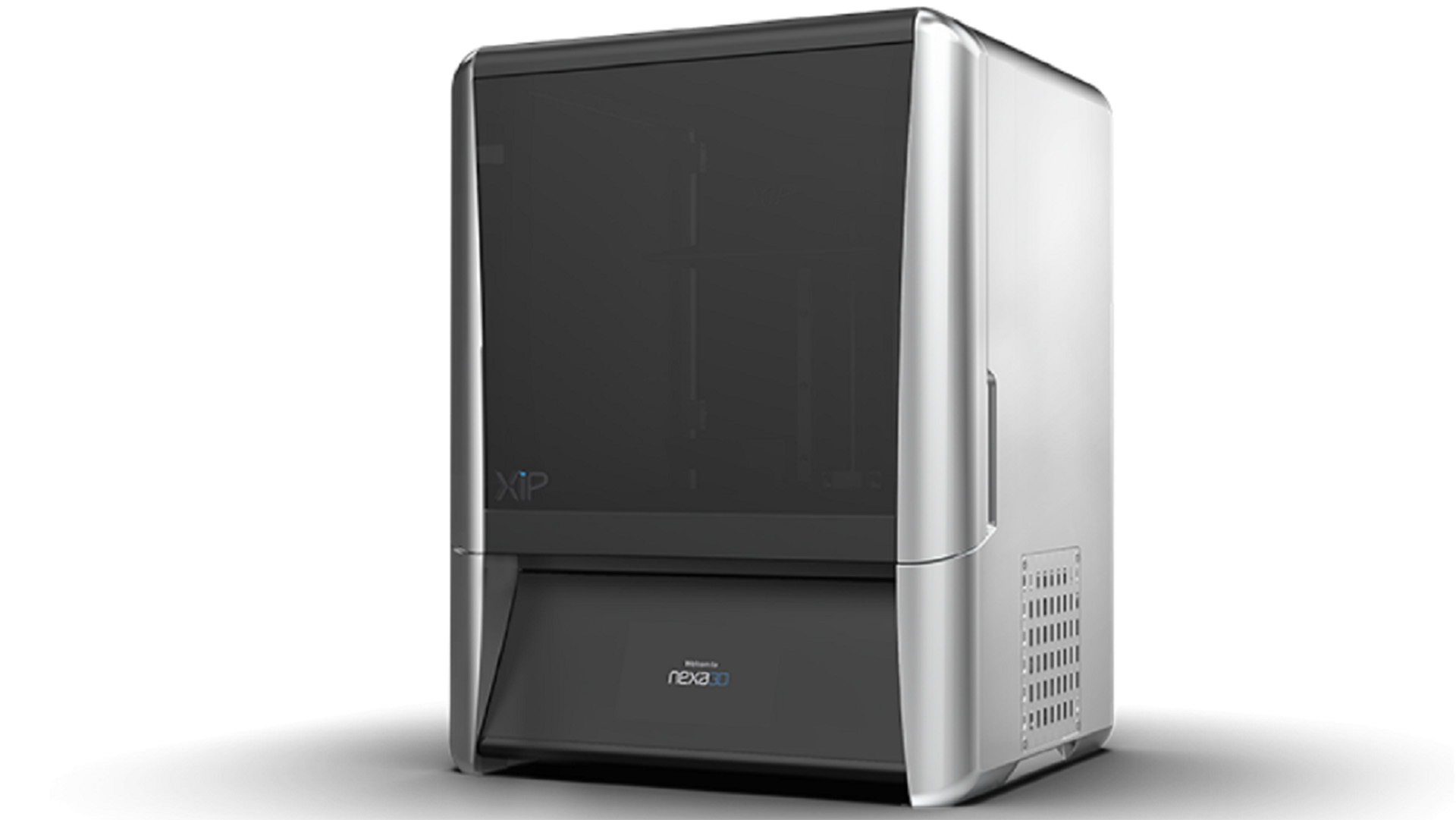
What does it take to transfer industrial capabilities to desktop 3D printing?
As additive manufacturing technology has advanced, the gulf between industrial and desktop 3D printing has narrowed. Blurring the lines means that today’s design engineers expect more power at their fingertips. Beyond rapid prototyping, desktop 3D printing is increasingly a tool to bring new products to market faster or even offer bridge production. Workflows are becoming more versatile – and it’s up to the 3D printing industry to keep up with that flexibility.
Industrial 3D printing capabilities are well understood today, offering ultrafast production with fine-tuned materials and performance. Desktop 3D printing, though, has had more of a stutter-start in offering market-ready performance. Some of the best-known desktop workflows remain plagued by common pain points. In order to successfully bring a new product to an increasingly saturated desktop 3D printing space, specs need to be substantively set apart to measurably perform better.
What does it actually mean, though, to take industrial 3D printing capabilities to the desktop?
It means rethinking everything about not just a 3D printer, but the end-to-end workflow attached to it. It means thinking about the why behind every aspect of every process.
Additive manufacturing is an industry accustomed to thinking differently. With a new way of manufacturing, new possibilities open up in terms of design, lightweighting, topology optimization, biomimicry, part consolidation: it can seem that the sky is the limit. Really, though, the tech is the limit.
With the NXE 400 industrial 3D printing system on the market for a few years, customers have been approaching Nexa3D with a request: make it smaller. Industrial productivity has shown to offer the yield and performance needed, but ramping up to production or creating new designs often require a step back – to the drawing board. To the desktop.
“The XiP was designed in response to customer demand,” says Michael Currie, Nexa3D VP & GM of Desktop Solutions. “After becoming familiar with the speed and precision of LSPc technology on the industrial level, users contacted us wanting to know if we would modify that technology for the desktop level. We thought that would be a great opportunity to reach a wider range of industries, so we began working on scaling LSPc to meet the needs of businesses of all sizes.”
Taking an advanced mSLA process to a different build volume isn’t a straightforward proposition. Optical systems, LCDs, and all the ‘secret sauce’ that comes together to make a process work is a fine-tuned orchestration. Sizing down (or up!) requires a reworking of the underlying physics.
Further, there’s always the question of why the market could possibly need another desktop 3D printer. The value proposition needs to be differentiated enough to make a potential user look twice. What gets that second look?
Performance, for sure; 3D printing is a solution-driven technology. When the Nexa3D engineering team approached taking the proprietary Lubricant Sublayer Photo-curing (LSPc) technology from an industrial footprint to the desktop, it wasn’t just a question of scaling the technology down, it was about addressing the common pain points associated with desktop 3D printing, particularly resin desktop 3D printing.
With SLA, speed is always a concern. Traditional SLA 3D printing works by curing a part a tiny bit at a time, painstakingly tracing it out with a laser beam. While mSLA sped things up by allowing entire layers to be exposed at one time, LSPc took it a step further. In addition to a UV light array that cures the entire print area with uniform intensity, the XiP’s speed draws from what Nexa3D calls the Everlast Interface.
A typical vat bottom, or membrane, in an SLA 3D printer serves as the foundation of a print. The print layers cure against this membrane, and once the print is complete, it must be carefully peeled away to protect the structure. The Everlast-2 Interface was developed to circumvent this typically slow and delicate operation with a self-lubricated, flexible membrane that resists sticking to both the printed part and the underlying LCD screen. This allows a quick, damage-free release of the part.
In addition to speed, everyone, naturally, wants a frustration-free process. The user experience is not insignificant when it comes to selecting a 3D printer; a smooth workflow and reduction of waste and mess go a long way toward eliminating headaches. Much has been said about “push-button” technology; the designers of the XiP aimed at making that phrase as literal as possible.
The XiP was designed with a Smart Resin System that allows users to easily pop a cartridge in, even during a live print job. Once resin has been loaded, the XiP uses NFC technology to authenticate the material and match it to build requirements. 3D printing, as an advanced manufacturing technology, should be smart – but it’s only as smart as a particular printer. The XiP is an intelligent machine, one that allows users to, well, push a button and walk away.
Another buzzword often heard in the 3D printing industry is “open-source,” a philosophy that Nexa3D has embraced. Collaboration is where progress happens. The XiP reflects that idea with an open-source material system that allows users to develop their own materials, and Nexa3D takes it a step further by encouraging those users to share their ideas about how the XiP could look in the future.
3D printing is an ever-changing and growing industry. The XiP is not a shrunken-down copy of Nexa3D’s industrial 3D printers, but its development stemmed from a desire to allow a wider range of businesses to print production-quality parts. When a desktop machine can create both prototypes and finished products, using the same materials, it represents a step forward into true democratization.
The XiP will be available for purchase in Q2 of 2022. Until then, you can join the waitlist to be informed once it becomes commercially available.