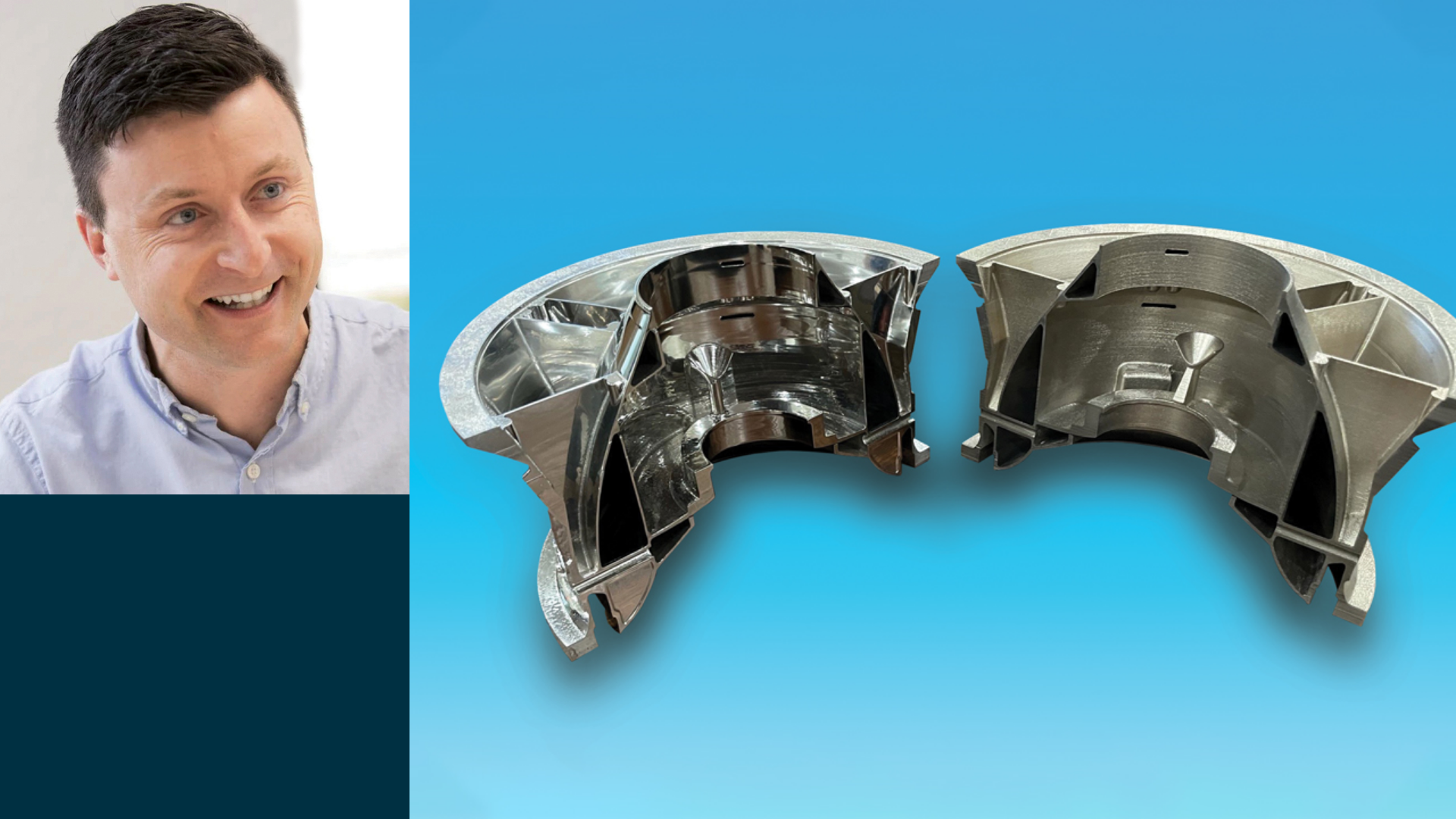
The future of additive manufacturing (AM) will rely heavily on software advancements. New software platforms will help engineers design parts for 3D printing faster and more efficiently. Zach Murphree, the vice president of global sales and business at Velo3D, highlights the advances in software and how new standards will help engineers ready parts for the additive manufacturing process.
Adam Penna: How has the role of software evolved within AM?
Zach Murphree: Traditional additive manufacturing in the complex, mission-critical metal parts industry is very reliant on Design for Additive Manufacturing (DfAM). After engineers design the part they want, they’ve had to redesign it for additive manufacturing. Then, another engineer takes the DfAM part and builds a print file for a specific machine.
However, solutions are emerging that eliminate the need for part-specific development. Engineers simply design the part they want, upload the file, and the software prescribes how it should be manufactured. For example, Velo3D’s Flow print preparation software does this by taking a set of recipes for various designs and geometries it knows how to create, analyzes the CAD file that a customer wants to print, and prescribes a process for 3D printing it in the most efficient way.
A.P.: What new standards have been developed to help engineers design for additive manufacturing?
Z.M.: A good example is the API20S standard from the American Petroleum Institute. This standard is the first-ever oil and gas industry sanctioned specification for metal additive manufacturing. As more of these standards emerge to outline specifications for companies looking to build parts for their respective industries using additive manufacturing, we will see greater adoption.
A.P.: Within the oil & gas industry, how is additive manufacturing being used to create parts?
Z.M.: Additive manufacturing is generally used in oil and gas in three ways. The first is in the rapid prototyping of parts that will be manufactured with different technology. The second is in new products that are designed to leverage the capabilities of additive manufacturing. Additive is used in both the product development and initial production and the high-volume serial production of these parts. The third is in maintenance and repair applications where manufacturers or part customers can no longer get the parts they need through their traditional supply chains.
A.P.: How can engineers better leverage software to design more efficient parts
Z.M.: Engineers looking to leverage software to help them in additive manufacturing should begin by looking at design and analysis software as the first tool to optimize the part for its intended application. Engineers also need new software from manufacturing technology companies to print the part without compromising its performance because of constraints on the manufacturing technology.
A.P.: How much post-processing is required once the production part is printed?
Z.M.: Post-processing is required on additive parts in areas where you need a surface finish closer to that of a machined part, like sealing surfaces or mating surfaces. There is also post-processing required wherever supports need to be removed. Some additive technologies can produce parts with far fewer (or no) supports, enabling the manufacturing of internal flow paths or other inaccessible areas.
A.P.: What should engineers know about the machine and material qualifications?
Z.M.: The challenge is that machine and material qualifications are very industry-specific—especially with mission-critical components. There are nuances around qualifying parts made through additive manufacturing. Industries are working to define what those requirements are.
Adam Penna is director of content strategy for Metrix.