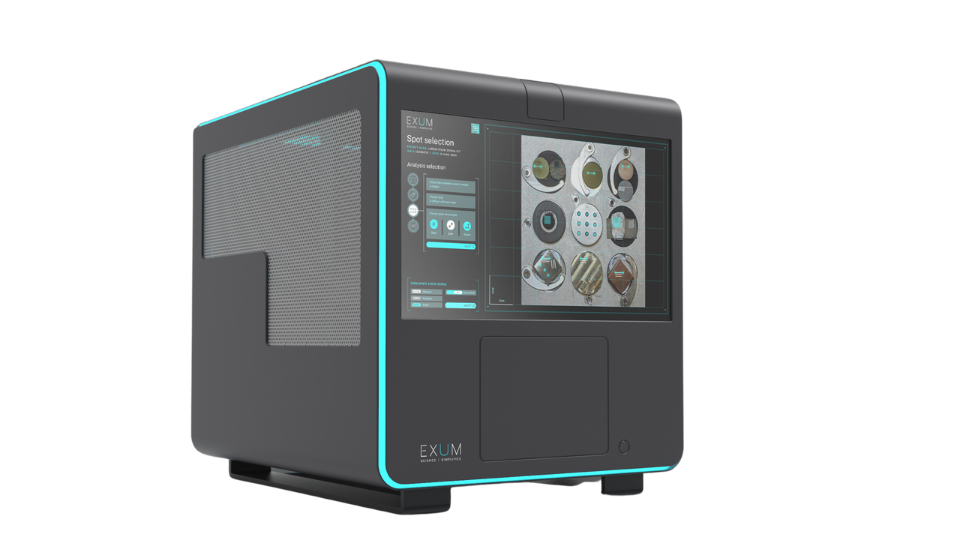
The Challenge
The physical properties of any manufactured material depend on its chemical characteristics. Such understanding of additive manufacturing feedstock powders determines the built part’s performance, including important aspects such as mechanical properties and corrosion resistance. Currently, feedstock chemical characterization requires multiple analytical techniques. Traditional methods like Inductively Coupled Plasma Optical Emission Spectroscopy (ICP-OES) and ICP-Mass Spectrometry (ICP-MS) require chemistry expertise to properly perform acid digestion for liquid sample introduction, correct for interferences and matrix effects, and execute calibrations. Furthermore, light elements like carbon, oxygen, and nitrogen are not easily measured by ICP-OES and ICP-MS. These important light elements affect metals’ properties such as brittleness, hardness, ductility, and melting point. Quantifying these elements requires additional analytical methods, such as inert gas fusion and combustion.
Laser Ablation Laser Ionization Time of Flight Mass Spectrometry (LALI-TOF-MS)
Addressing the challenges associated with other analytical techniques, Laser Ablation Laser Ionization Time of Flight Mass Spectrometry (LALI-TOF-MS) offers rapid, high-sensitivity quantification of nearly the entire periodic table. LALI uses two lasers to first ablate, or release, material from a solid sample’s surface and then ionize the ablated material in a second step. The laser ablation process allows direct analysis of solid materials, like additive manufacturing powders or parts, without the complicated sample preparation procedures. The ionization laser targets the neutral particles created by ablation, which are more representative of the sample’s constituents compared to plasma-generated ions used by ICP-MS. Overall, LALI results in more reliable isotopic verification and reduced matrix effects.
After ionization, the TOF mass analyzer measures the difference in time required for ions of different masses to impact a detector. This creates a full mass spectrum at each laser shot, as shown below. Figure 1 displays a stainless-steel powder certified reference material, IARM Fe316LP-18. Based on the naturally occurring isotope patterns, the software verifies each detected element in the spectrum. The top pane highlights trace (i.e., less than 1,000 parts-per-million (ppm)) low-mass elements that are difficult for many techniques to quantify: carbon, nitrogen, and oxygen. The bottom pane shows the naturally occurring isotope pattern for a major element, nickel. The text box compares the theoretical (known) isotope ratios with those quantified from the mass spectrum’s peak areas. The measured isotope ratios nearly match those of the known values, demonstrating LALI-TOF-MS can create mass spectra with isotopically correct peak intensities.
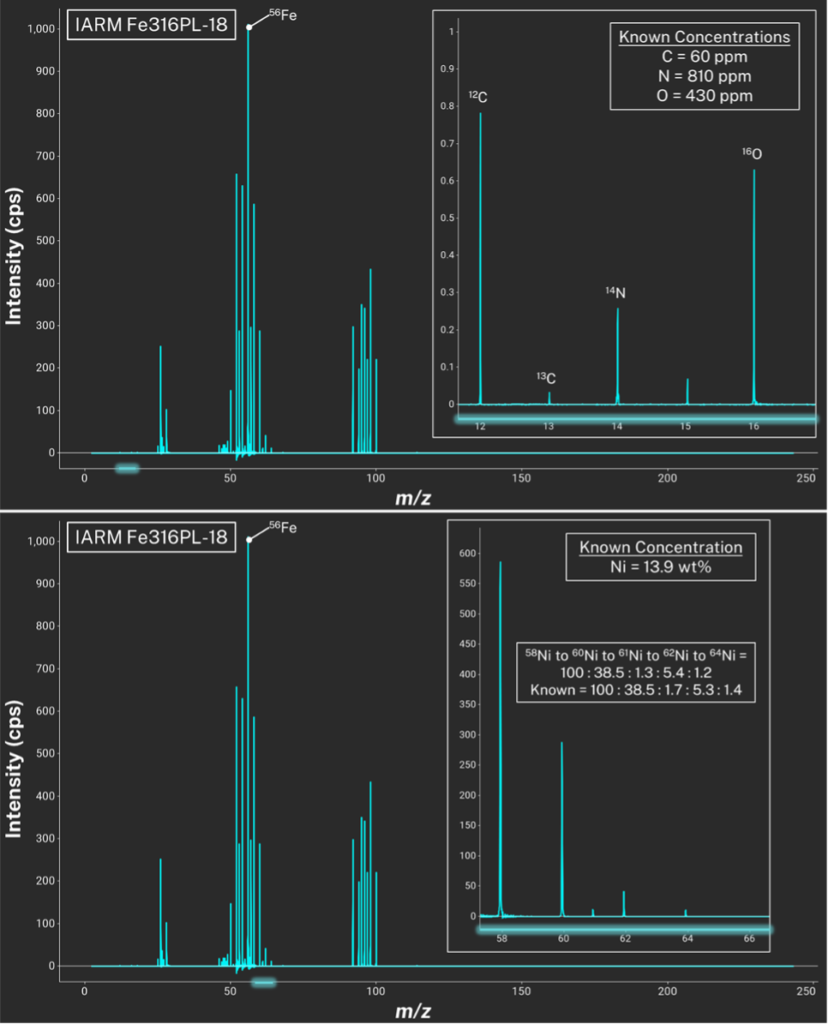
Testing Quantification Capabilities
Demonstrating the new mass spectrometer’s quantification capabilities involves analyzing a set of certified reference materials, treating one as an “unknown,” and quantifying its constituents using calibration curves generated by the remaining reference materials. As detailed in the table below, four additive manufacturing (AM) powder samples were analyzed in this study. Because LALI-TOF-MS requires a solid sample, powders are pressed into 1.3-cm (0.5-in) solid pellets using a pellet die set and hydraulic press.
Summary of Certified Reference Material (CRM) Samples
Sample No. | Material Type | Material Grade |
1 | Pellet pressed from pure AM powder | 316L Stainless Steel |
2 | Pellet pressed from mixed AM powders | 316L Stainless Steel + 14 wt% 718 Nickel Alloy |
3 | Pellet pressed from mixed AM powders | 316L Stainless Steel + 6 wt% 718 Nickel Alloy |
4 | Pellet pressed from mixed AM powders | 316L Stainless Steel + 0.6 wt% 718 Nickel Alloy |
Each sample is analyzed using three 0.2 mm2 areas. The areas are rastered twice, removing any surface contaminants in the first pass and using the second pass for quantification. The system’s sample tray can accommodate up to nine pressed pellets, and the user can set up the instrument to analyze all samples within the same session. While the user is defining testing conditions, the instrument brings the closed sample chamber to vacuum. Once vacuum is achieved, the analysis requires only three minutes per sample.
This study involved treating Sample #1, the 316L stainless-steel powder, as an “unknown” and quantifying its major and trace elemental constituents from calibration curves generated from the remaining samples. Figure 2 compares the quantified results to the material’s certified values. In this graph, certified values are gray and those quantified by LALI-TOF-MS are blue. Major elements’ concentrations are presented in weight percent (wt %) and those of trace elements are in parts-per-million (ppm). On the known values, the error bars indicate the certified uncertainties. Uncertainties for the quantified values are calculated to a 95% confidence interval using least squares linear regression of the calibration curves’ points and unknown (all measured in triplicate).
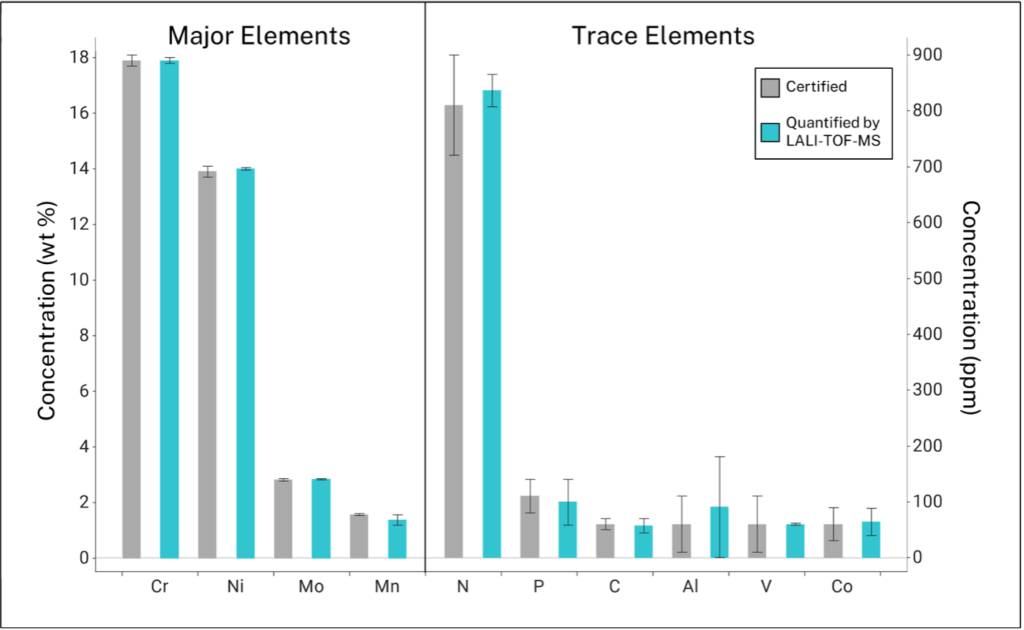
Summary
This study highlights LALI-TOF-MS as a promising new and alternative technique for chemical characterization of additive manufacturing powders. Treating the 316L stainless-steel powder reference material as an “unknown,” all elemental constituents were quantified within the certified values’ margins of error. Internal precision was 1.1% relative standard deviation (RSD), calculated from the triplicate raster areas’ variance. This low variance demonstrates the repeatability of the technique.
Quantified results’ accuracy for major elements were 4% on average, and all major elements were within 13% of certified values. For stainless steels, ASTM specifications allow an acceptable concentration range of ±0.5 to ±2.0 wt% for major elements. In this study, LALI-TOF-MS quantified all major elements within 0.02 to 0.20 wt% of certified values, and uncertainties were all less than ±0.18 wt%. This demonstrates LALI-TOF-MS can exceed the precision and accuracy required of the additive manufacturing industry.
Because this innovative technique can quantify the metallic, trace, and light elemental constituents in the same analytical session, it has potential to reduce quality control time and accelerate research and development for additive manufacturing powders. LALI-TOF-MS combines high-sensitivity chemical characterization with simplified operations into a compact, desktop package.