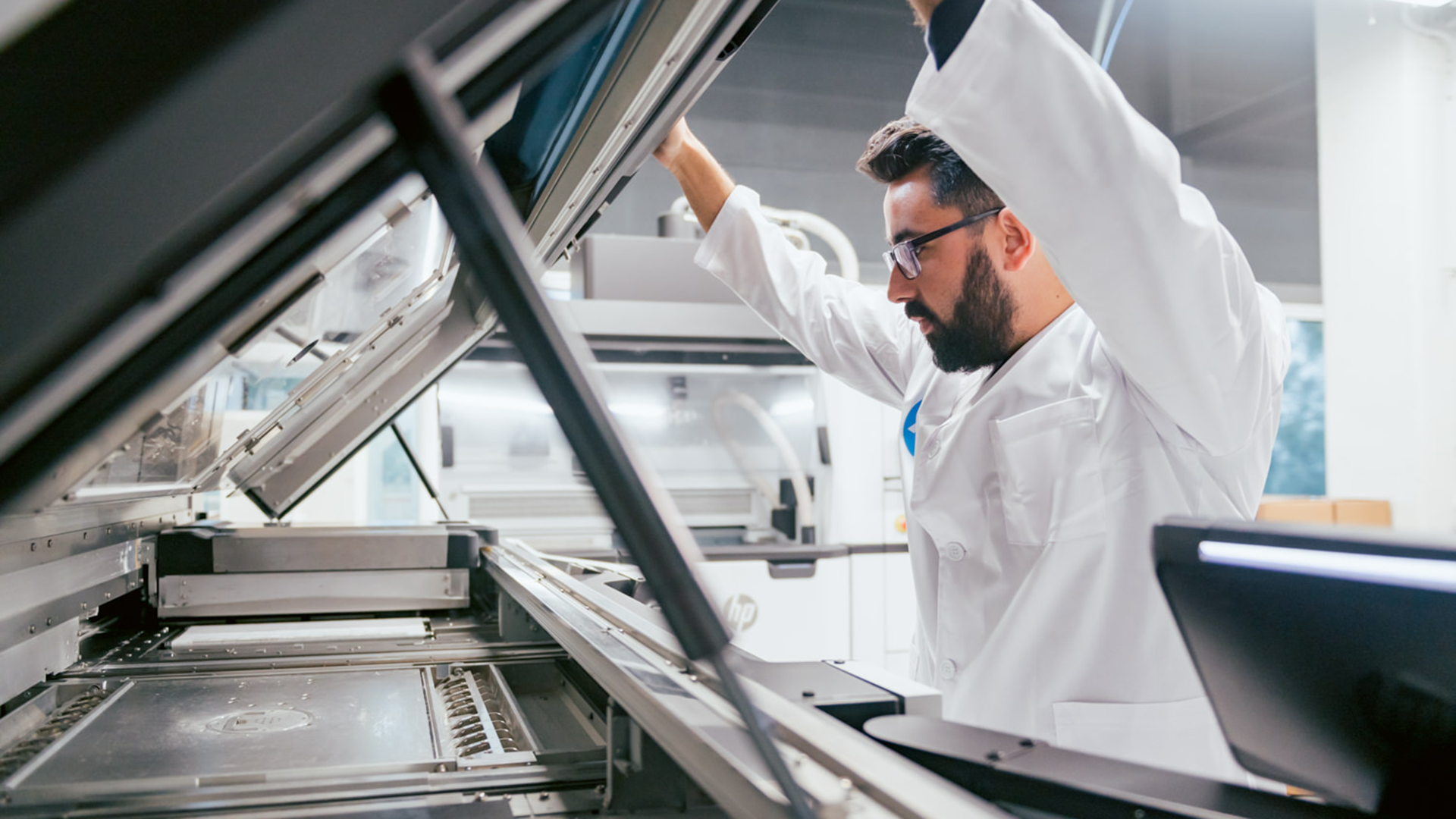
In 2022 we expect a new era of mass-personalization enabled by digital manufacturing to disrupt a range of large industries, drive innovation, and create new value. Industries ripe for disruption include the highly personalized health and wellness sector. We believe this is a huge growth area as people seek better health outcomes based on their individual needs. For example, orthotics and prosthetics are an approximately $10B opportunity. We are collaborating with the lower limb industry to upend the status quo with the new Arize end-to-end digital orthotic solution, providing efficiency and customization capabilities not possible through traditional processes . In addition, another multi-billion dollar opportunity is in personalized sporting goods and high-performance athletic footwear. We are also working with customers like SmileDirectClub in the U.S. and Impress in Europe as they continue to push the boundaries of oral care using 3D printing to manufacture highly personalized products at scale.
As companies look to meet the demand for more personalized products they are also looking to deliver more sustainable products and packaging. When HP surveyed global digital manufacturing and 3D printing decision makers in late-2020, an overwhelming majority (89%) said they were changing their business models, and at least 9 out of 10 were investigating new and more sustainable supply chain models. 3D printing is providing more sustainable manufacturing methods from sustainable design that removes excess weight and waste to local production that leads to a lower carbon footprint. We are inspired to make a huge difference in the environmental footprint of plastic packaging as we aim to replace the more than 150 million tons of single-use plastics produced each year with fiber-based packaging that is 100% biodegradable in any waste-stream. Recently, HP acquired Choose Packaging, a packaging development company and inventor of the only commercially available zero-plastic paper bottle in the world. In addition, we are delivering solutions to transform industries such as fiber-based packaging by enabling compostable products to be brought to market faster and more affordably. We are currently working with several large brands on solutions for food, beverages, cosmetics, and dairy products.
We are seeing companies develop new supply chain strategies for risk mitigation, not only to address the current Covid-19 crisis or future pandemics, but to guard against volatile global economic trade cycles. Advanced 3D printing solutions can help them accelerate this transformation. We expect industries will look at 3D printing as a way to disrupt their traditional supply chains and make them more efficient and flexible. In addition to new applications, we believe entirely new ecosystems and alliances will emerge as companies look to deliver more value to end customers. We’re already seeing this trend take hold in industries including automotive, consumer, healthcare and industrial. A recent example is HP’s work with L’Oréal, the world’s largest cosmetics company, to increase production flexibility, create innovative new packaging and customer experiences, , and provide added agility in response to changes in consumer purchasing behaviors. L’Oréal plans to use HP’s Digital Manufacturing Network across its global supply chain and meet its sustainability goals by efficiently producing parts when and where they are needed.
We are very excited about the promise of additive for mass metal manufacturing, the fastest growing segment of the traditional 3D printing market. Based on HP’s core Thermal Inkjet capabilities, our Metal Jet technology enables the production from high volume runs to truly unique high-value parts. We believe our modular system and integrated workflow delivers better productivity, lower part cost, and superior quality. For example, I am very pleased with our advancements with Volkswagen. Volkswagen shared a recent use case highlighting HP Metal Jet produced parts for the A pillar of the T-Roc Cabriolet. The structural parts have passed crash test certification and weigh almost 50 percent less than conventional components. Auto manufacturers are among the most demanding in the world. This is the first time an automaker is using metal binder jetting for structural components. We are continuing to validate production applications with partners and customers as we move toward broader commercial Metal Jet availability in 2022.