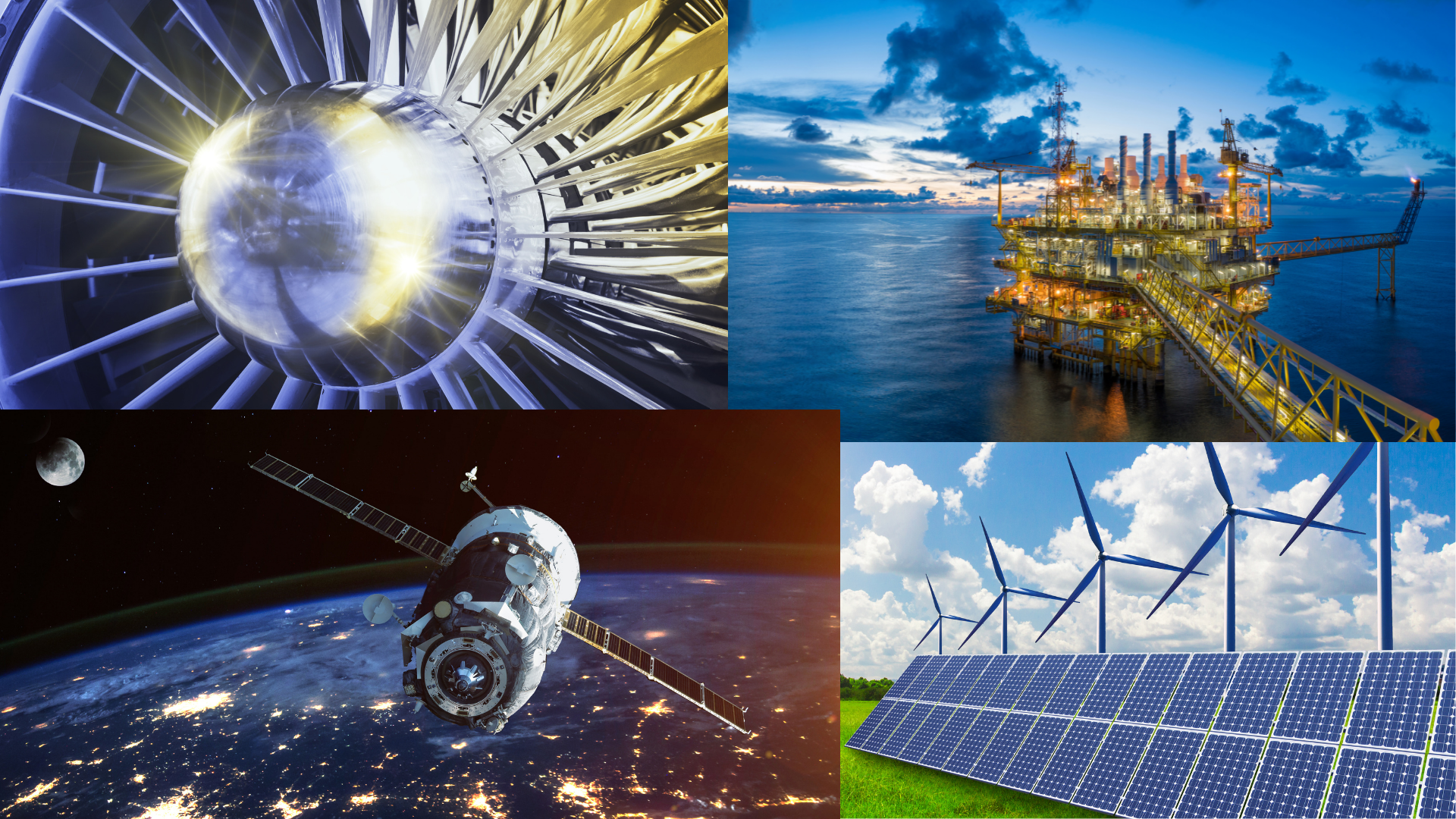
AM’s journey in energy mirrors the aerospace industry.
In the additive manufacturing community, the aerospace sector has been an application leader for more than 30 years. Like the automotive industry, the ability to accelerate design and development was the first value of rapid prototyping. Assembly jigs soon followed, providing efficiencies for constructing aircraft fuselages and more.
What may be surprising is that the first additively manufactured part certified for flight was in 1999. Boeing developed polymer environmental control ducting and other nonstructural parts for the F-18 Super Hornet. Within two years, a supply chain with Boeing-certified suppliers was in place to produce more than 100 laser-sintered nylon parts per aircraft. In 2007, Boeing added the first certified AM component to the 787, a nonstructural laser-sintered nylon part. Today, Boeing has reported more than 100,000 AM parts in flight, most of which are non-metal components.
By comparison, the energy sector is newer to AM, with the oil and gas sector categorized as being in the early adoption stage. The first safety-critical component was field deployed in February 2021. Developed together with Vallourec, TotalEnergies installed an AM water bushing in the North Sea. Using a direct energy deposition (DED) process, a 1.2-meter-high and 220-kg metal component was 3D printed. By using AM, TotalEnergies was able to reduce total weight by 50 percent along with reducing the total carbon footprint of production.
Aerospace and energy may seem to be in two very different places with AM and have little in common at first glance. Taking a closer look reveals these two industries have technology needs that are nearly the same. Both are highly regulated, with a need to certify parts for use. Much of the production for aerospace and energy are highly complex and in lower volumes when compared to other AM sectors like automotive and medical device. These parts often require high performance and are exposed to extreme environments. Lightweighting for fuel efficiency and reducing carbon emissions are critical for both.
All of these similarities mean aerospace and energy professionals are looking to use AM to combine components, create digital inventories to reduce physical warehousing, utilize distributed production approaches to manufacture parts at the point of need, including for maintenance and repair, and 3D print large scale structures. Both focus on metals including refractory metals, next-generation polymers with high heat properties, ceramics, and composites.
The AM processes used most often are the same, including powder-bed fusion and direct energy deposition. Even the applications are similar with both using AM for turbines, valves, nozzles, heat exchangers, and repairs. As with all using AM for end-use, aerospace and energy are also looking for effective nondestructive evaluation tools, repeatable processes, and total process strategies, from design to use.
Bringing aerospace and energy together promises to provide opportunities to accelerate their AM use. One can see the paths built by experience, while the other can hear fresh perspectives and questions. To learn more about the developments and strategies used to achieve their AM goals, plan to attend the AM Industry Summit: Aerospace & Energy, June 21-22, 2022, in Long Beach, California. event.asme.org/AMIndustrySummit