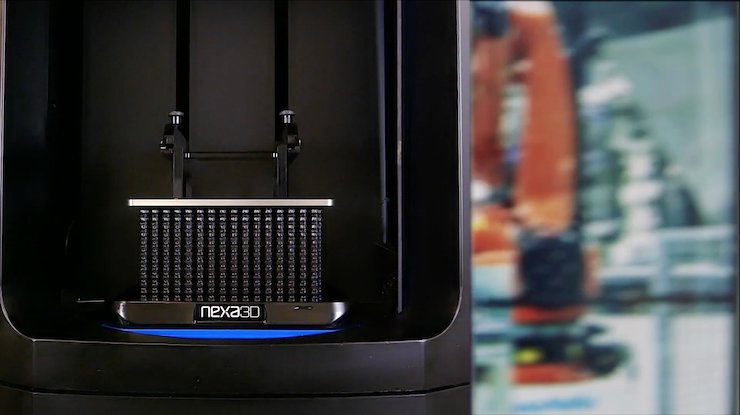
The manufacturing industry has faced a number of changes and challenges over the past few decades. Manufacturers in both North America and Europe have seen jobs migrate overseas in the name of cheaper labor and production, leading to the closing of many companies that had been operating for years. Some other companies, however, found that with flexibility, creativity, and a willingness to adapt to changes in manufacturing technology, they could rebuild their success.
Czech production company KADEN has a true survivor’s story. Upon its founding in 1950, the organization functioned as a government-controlled commune of companies focused on carpentry and tool shop work. In the 1960s, KADEN (then known as KOVODRUŽSTVO Náchod, before its 1992 renaming) shifted to the production of metal toys, particularly toy cars.
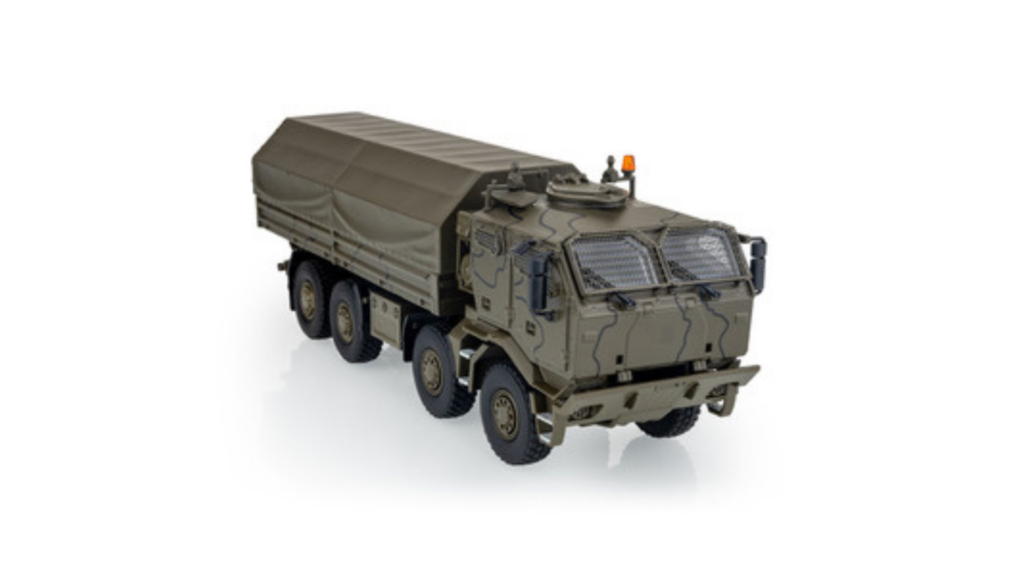
KADEN faced steep challenges in the 1990s. At that time, the company was still producing its toy cars, made from zinc alloy and plastic. Foreign competition was growing due to the lower costs of outsourcing to China, which came at an especially bad time for East European companies that were trying to rebuild after the collapse of communism in 1989. By 2010, only two major diecast toy manufacturers remained operational in Europe.
In 2020, KADEN was down to only about 40 workers, who mainly provided assembly services for other model manufacturers. While they were a highly skilled and diverse team, their skills weren’t being leveraged to their full potential. That was also the year, however, that Filip Klepek, a new Managing Director, stepped in. Determined to restart European production and reduce dependence on outside providers, Klepek saw a shift to additive manufacturing as the solution.
KADEN then began exploring additive manufacturing solutions from multiple providers. None of them, however, was a great fit. A single part could take over nine hours to print, which meant that at most, KADEN could use these printers for occasional prototyping, but none of them was the solution the company was looking for. Then they discovered Nexa3D.
Another Czech company, Industrial Technology Systems (ITS), reached out to KADEN around that time. ITS, a reseller of Nexa3D’s ultrafast 3D printers, thought that Nexa3D’s industrial NXE 400 3D printer would be a good match for KADEN’s needs. Klepek had been overseeing the implementation of CAD software and in-house additive manufacturing capabilities within KADEN, and was quickly won over to the NXE 400 by how fast it was able to print benchmark parts from KADEN’s files. In stark contrast to the other printers the company had tried, the NXE 400 was able to print a full plate of those parts in a fraction of the time.
KADEN was sold on the size, speed, and industrial production capabilities of the NXE 400, but still faced the challenge of learning an entirely new technology. With the assistance of ITS, however, they were able to pivot from traditional manufacturing technologies to the much faster process of 3D printing.
KADEN did not do away with all of the techniques they had previously used, ensuring that artistry and skill continued to shine through for these in-demand products. The company’s model cars are still finished and assembled by hand, and their diecast exteriors are hand painted with airbrushes. The plastic and soft rubber parts, however, are produced on the NXE 400 using 3D printing materials like Loctite xPRO410, also supplied by Nexa3D. The speed and build volume of the printer let KADEN decrease production costs while increasing output and quality and allowing time for the careful hand-finished detail the company is known for.
Much has been said about additive manufacturing replacing more traditional methods of production, but in the case of KADEN, it serves as a complement to the older forms of artistry that have formed the company’s roots. KADEN is still able to craft its cars with individual attention, even more so now that other parts of the process have been so dramatically sped up. Previously, expensive aluminum tooling and molds could take up to three months to acquire; now functional prototypes and final production parts can be made in the same day. By optimizing the space offered by the NXE 400, KADEN can print 108 model car tires in 34 minutes.
Using additive manufacturing, KADEN is able to produce both functional prototypes and end-use parts, including the detailed interiors of its cars. The company is now offering significant competition against foreign manufacturers. In addition, KADEN intends to begin manufacturing model parts for other European companies. Additive manufacturing has helped KADEN to not only survive, but to grow.