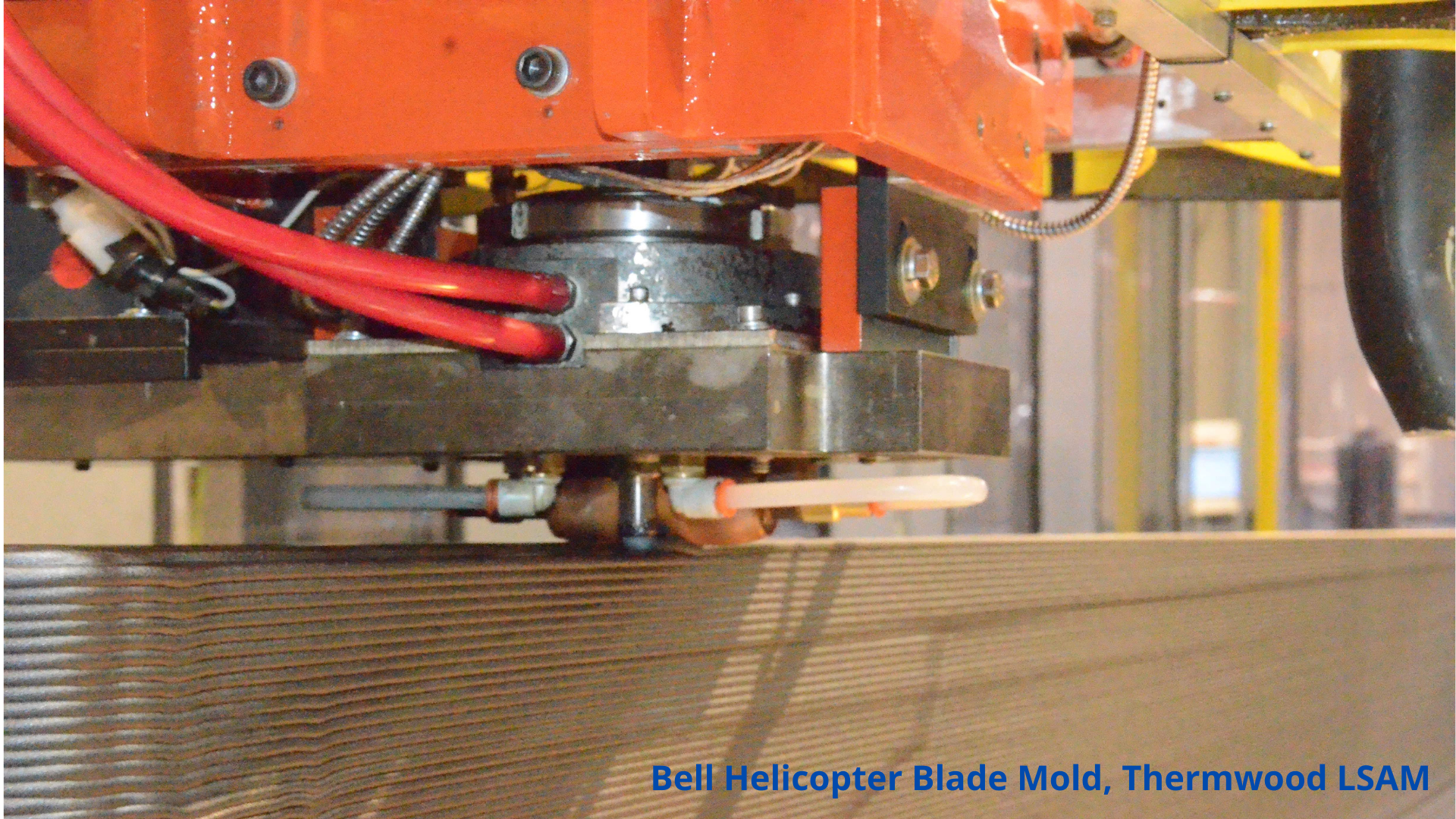
Many people are familiar with 3D printing or its more formal name additive manufacturing (AM), making a part layer by layer. Most 3D printed parts will fit in your hand. Industry has been pushing the limits of AM, both larger and smaller. What if we could go really big? We call really big Large-Format Additive Manufacturing or Large-Scale Additive Manufacturing.
As it turns out, there is quite a lot going on in large-scale additive manufacturing in processes and materials and their impact on aerospace and energy markets.
The first place to look is tooling. With 3D printing, we might think of tooling as an inspection fixture. Companies like Bell Aerospace use a Thermwood LSAM to print large composite tooling like a mold for a helicopter rotor blade. Manufacturers can extrude carbon-reinforced high-temperature thermoplastics with extrusion-based technology similar to an FDM machine. Like all additive manufacturing, we must not overlook post-processing. Post-processing typically consists of machining the tooling surface to make it smooth and accurate. The Bell LSAM has built-in machining capability. LSAM tools can work in an autoclave with composites vacuum bagged to the tooling surface. Bell can print with a low coefficient of thermal expansion thermoplastic and make a tool with vacuum integrity.
Once a composite part has cured, it is typically trimmed with a router. To trim a composite component, there is a need for a unique tool that will position it in space so that critical features like the outline, access ports and fastener holes can all be accurately machined. Large-scale additive manufacturing is faster and less expensive than traditional methods for making durable production trim tools. General Atomics and Boeing are making LSAM trim tools.
Reinforced thermoplastic is not just for aerospace. Oak Ridge National Laboratory and the National Renewable Energy lab successfully collaborated in printing a mold for a wind turbine blade in 2017. The University of Maine with funding from the US. Department of Energy is developing a 3D printing solution to make segmented wind turbine blades.
When we look at composite manufacturing, it is a type of additive manufacturing. Manufacturers add carbon fiber and resin to build a part layer by layer. The resin can be epoxy, polyester, or even thermoplastic. Electroimpact builds robotic systems that can extrude a thermoplastic to make a tool, machine the tool and wrap the tool with carbon fiber composite.
Continuous Composites makes a machine that uses a photo-cured polymer with carbon fiber. The robotic system deposits the carbon fiber and cures the polymer instantaneously. They can make some large carbon fiber composite parts without tooling.
When made the traditional way out of a block of material, some metal aerospace parts are not very efficient. Over 90% of the material is often machined away to leave a robust and lightweight component. With additive manufacturing, you only add material where you need it. For post-processing, a little machining may be required to improve the surface or dimensions, but still, you use most of the material in the part.
Direct energy deposition, DED is a metal additive technique that grew out of the laser cladding business. Laser cladding has been used for 20 years to add material to the surface of parts in the oil and gas industry to improve wear resistance. It has also been used in both aerospace and energy to repair turbine blades. A small amount of material can be added to the worn tips of the turbine blades to bring them back to specifications.
In DED, a laser is focused near the surface of a part and either metal powder or a metal wire is melted and welded to the layer below. There are a variety of companies selling laser DED systems, including Optimec, Hybrid Manufacturing Technology, RPM Innovations, Inc., Meltio, Trumpf and AddUp,
Sciaky makes DED systems where an electron beam melts the metal. Electron beams must work in a vacuum, which adds cost and complexity to the machine and eliminates contamination of the process. They can deposit 15 pounds per hour of titanium to build a part in two days that could take up to a year with forging and machining.
Lincoln Electric has a system with three robotic welding heads that can use conventional welding to build large parts. They can even print in INVAR for aerospace tooling. INVAR has a coefficient of thermal expansion near zero, so it is ideal for composite autoclave tooling.
Another fantastic technology is coming from MELD. They use a process akin to friction stir welding to Melt metal and build parts layer by layer. They are working with the US Army to try to print heavy military vehicle frames.
SPEE3D and TITOMIC make machines using cold spray technology for AM. In a cold spray process, you accelerate a gas stream to supersonic speeds and introduce a little metal powder into the stream. You then impact the powder enriched stream against a plateāthe metal particles bond on a molecular level without melting or heat. You can build parts layer by layer quite quickly. This room-temperature process has benefits in conductive materials like copper.
Several equipment manufacturers and dozens of builders are attempting to revolutionize the housing market by 3D printing homes, apartments, and offices out of concrete. The latest news affecting the energy market is GE Wind has partnered with COBOD and HOLCIM to develop wind turbine towers printed out of concrete. The larger the wind turbine, the more energy it can deliver. We are at the size limit for transporting wind tower components today. If we want to go bigger, we will need technology like concrete additive manufacturing where we build the tower on site.
There is new technology developing for additive manufacturing in the aerospace and energy sectors every day. Follow Metrix and the AM Industry Summit at AdditiveManufacturing.com to be in the know.