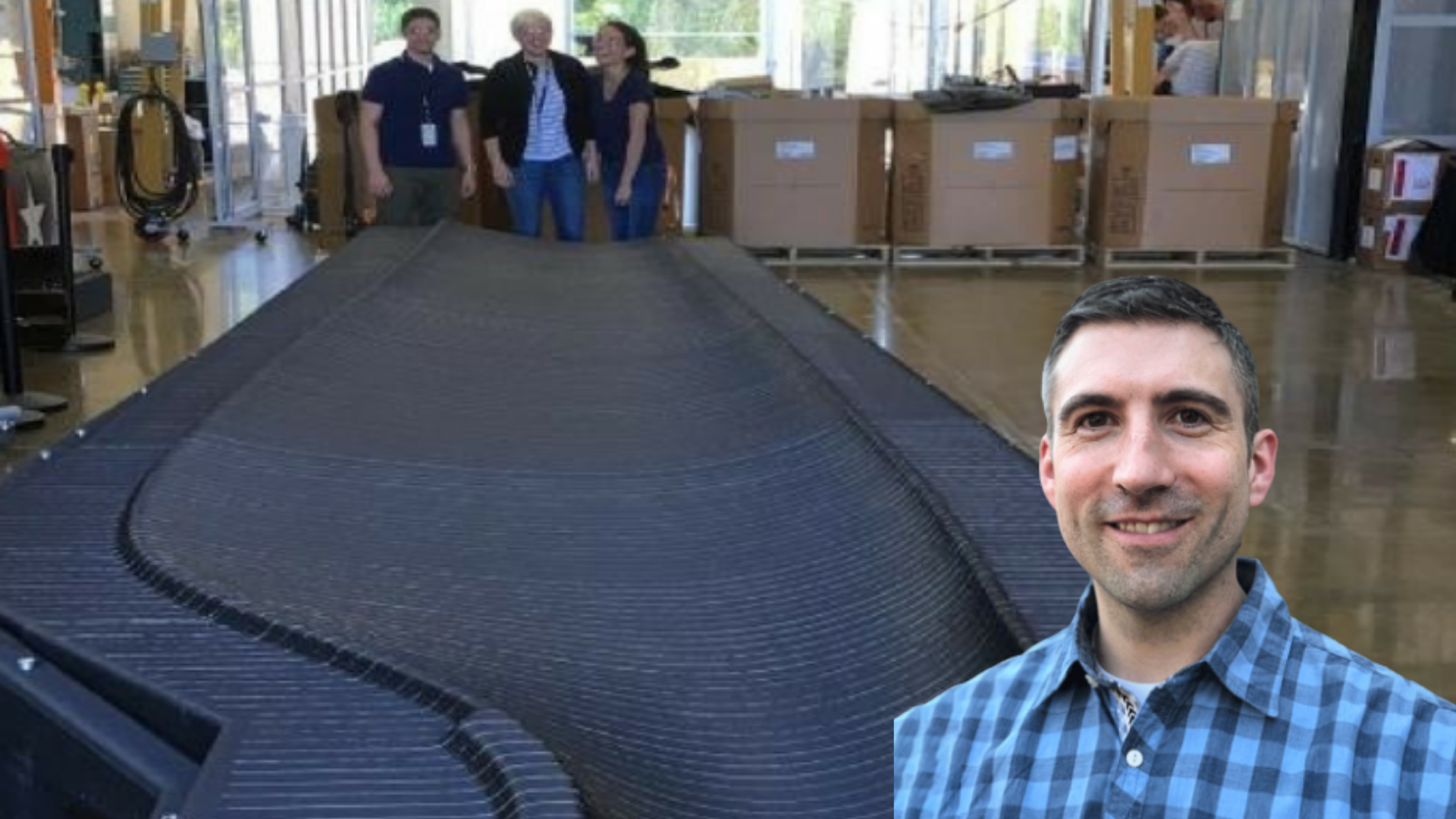
The ability to use additive manufacturing to produce large-scale components is growing, particularly in aerospace and energy. Blake Marshall, Technology Manager, Advanced Manufacturing Office, US Department of Energy, shared some insights during a panel discussion at an AM Industry Summit to understand the processes, materials, and where large-scale AM could be used.
Question 1: What is large-scale additive manufacturing?
Blake Marshall: I don’t think there’s one single definition, much like there’s not one single additive process. In general, we’re looking at those scales, at which things fundamentally change within the economies of scale, or the capabilities to build larger, both in terms of build volume or scale. Comparing to either traditional manufacturing or specifically a traditional additive manufacturing process, there are many differences. Things like the material set changes from custom small batch boutique type production in certain cases, to commodity feedstocks. The technologies are going to be, by the nature of them, larger. We’re often talking about being in the production environment itself. There are many other changes as well, in terms of how you coordinate all these energy systems or material deposition systems and the topology technological issues that come along with all of those challenges.
Q2: What types of large-scale AM systems exist?
B.M.: Oh good question, it might be hard to cover them all, because there’s a new one or seemingly, every week coming out, but there are a lot of different types. Large-scale metallics tend to follow along from cladding industries, some of the earlier techniques, like the DED powder blown techniques which you still see. The movement towards wire feedstocks and metallics with directed energy is becoming more and more popular. With wire fed large-scale additive techniques on the metal side, you see extrusion processes been used a lot for the higher side but also ceramics and printing of cements and reinforced polymer systems that tend to be extrusion based. Hybrid systems that incorporate both additive and subtractive are going to be increasingly important as the structures become larger. You might have surfaces need machining as you’re building in a variety of other systems coming into play. I should also mention binder jetting with has been used, but it’s a very different system and the way it’s applied. Material jetting, photo polymers and a variety of other things that may be further down the line, as well.
Q3: There are a number of different companies that have partnered with the Department of Energy in developing large-scale additive. The energy industry and the aerospace industry are fairly conservative. Could you talk a little bit about where this technology is being applied with some of the partners?
B.M.: I think tooling is a very useful and appropriate first market for a lot of these systems. Both because, we have the ability to iterate on the platform very easily and everyone who’s used the systems understands that these are not push button. As we move forward, large-scale additive is going to have to be more and more integrated with the overall cost structure of the of the facility itself. In certain cases, things like time to market for a new tool may be a critical factor. Maybe that shrinks by months and that can lead to huge changes in terms of bottom line sometimes. You may need to see that sort of thing happening, where it can offset potentially the increased cost of material or human capital, takes to design for large-scale additive. On a case-by-case basis, you have to address that. From our perspective, we’re trying to look at those first markets, those first movers, those sectors where it makes some sense to get to get in the door. Things like trim tooling for larger structures, for composite structures, make sense. We can move towards more advanced tooling as we develop the technology. That same type of technology can be applied to wind blades, for instance. There’s a lot of different composite technologies. The concrete printing can be applied to wind towers as well. We can see different entities’ large-scale processes integrating with energy systems. There’s all the gas, nuclear, and a variety of other applications as well.
Q4: That’s amazing. Are you making final use parts out of metal, for instance for either energy or aerospace applications?
B.M.: In certain cases, yes. I wouldn’t say in general, the large-scale systems are as ready for that application with some caveats. We do have programs focused on net shape components being printed out of titanium. We have we’ve partnered with Oak Ridge National Laboratory, supporting work with GKN to help develop net shape structures that are meters in length. There is some work to be done there and that may be one of the biggest, long-term impactful sectors. If we can actually print the primary structure of the airframe with huge buy-to-fly weight ratio losses, that would be impactful. But, that’s far down the road in terms of those primary structures that could be certified.
Q5: Do you see some applications opportunities that you’d like to talk about?
B.M.: There are also building applications we’re looking into like the actual built environments, buildings HVAC, etc. There’s still a lot of a lot of growth to see here, a very exciting place to be.