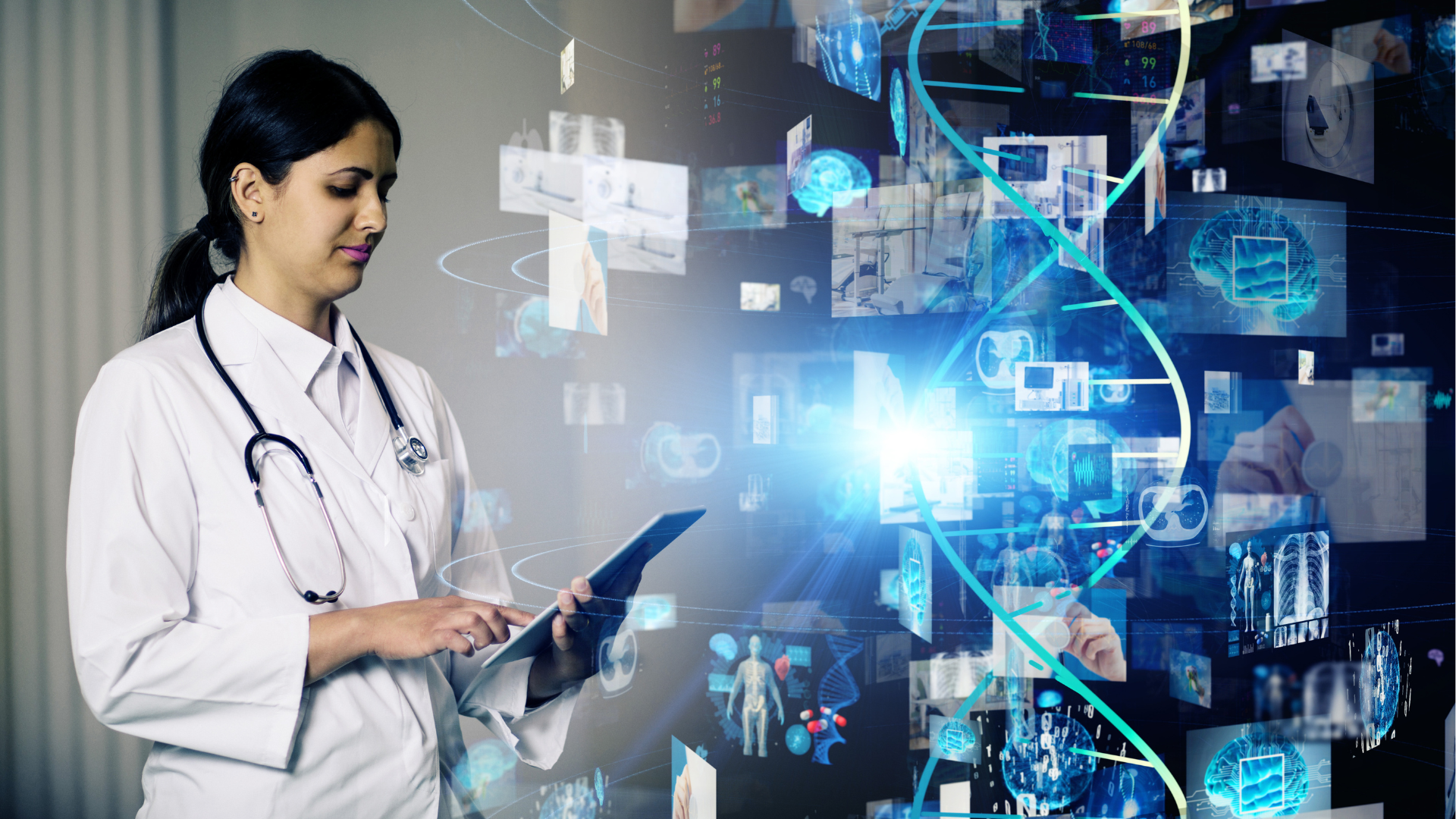
A Not-Too-Distant Future
Due in part to a very active and passionate medical 3D-printing community, the past decade has witnessed a significant growth of point-of-care manufacturing, including additive manufacturing, by a variety of healthcare providers. Simultaneously, but independently from these expanding PoC activities, significant efforts have been put towards progressing tissue engineering and tissue regenerative technologies, including the development of additive manufacturing compatible advanced biomaterials. Although not as mature as their traditional material counterparts, and not manufactured at the point of care, the number of synthetic and naturally-derived tissue regenerative biomaterial devices and products progressing through regulatory clearance and proceeding towards commercialization is increasing. With the parallel progress of PoC manufacturing and tissue regenerative biomaterial and product commercialization, it makes perfect sense to ask the questions will hospitals and other healthcare providers ever produce patient-matched tissue regenerative implants at the point-of-care? And if so, when? The answers are: Yes, and likely sooner than most think.
To understand the reasoning around these answers, it’s good to briefly review where PoC manufacturing is today. Healthcare-provider-led PoC manufacturing activities have primarily centered on the design, fabrication, and use of patient-assist devices, tools to assist with patient informed consent and physician education, guides to assist surgical procedures, and anatomically emulated parts to assist with pre- and intraoperative surgical planning and procedural execution. Although different, these applications share similar workflows and utilize the same sets of materials and 3D-printing methods, from extrusion, to jetting, to vat polymerization. Additionally, these applications are all external — they do not result in parts intended to be implanted within the human body, and thus are relatively low risk compared with implantables. Despite the significantly increased risk, there are an increasing number of examples of patient-matched implantable structures being produced at PoC. These implants are intended for hard tissue, boney replacement (i.e. cranial, orthopedic, thoracic implants) — similar to their industrial produced, non-PoC counterparts. The design and manufacturing processes of these permanent, structural implantables make use of very similar workflows as the non-implantables, but the materials as well as the 3D-printing methods utilized do vary — structural polymers such as PEEK and PEKK as well as established biomedical alloys, such as Ti64, formed primarily via powder-bed fusion additive methods. The progression to PoC additively manufactured tissue regenerative implantable structures from permanent implants comprised of traditional medical materials may seem like a large leap, but the workflows, 3D-printing methods, reimbursement strategies, technical standards, and workforce expertise used in current PoC activities are directly applicable and can be immediately leveraged.
What is new today, beyond the particular applications, are the materials being utilized. For clarity, tissue regenerative biomaterials can be divided into two major categories: acellular v. cellular. As the names suggest, the function of acellular, tissue regenerative biomaterials do not rely on the presence of exogenously added cells, but rather, the body’s own cells after implantation – where the cells interact with the biomaterials’ engineered microenvironment (composition + microstructure) and transform it into new tissue. This is in contrast to cellular biomaterials, which contain living cells at the time of manufacture, and whose function primarily derives from the presence of those cells. Additional biomaterial sub-categories exist: gel v. non-gel, synthetic v. natural v. hybrid, factor (drug, growth factor, etc.) containing v. non-factor-containing. Thus, tissue regenerative biomaterial 3D-printing/bioprinting is far more nuanced than immediately jumping to creating a fully living, functional tissue or organ at the PoC, which is likely still 5-10 years away. Unlike complex, cell-containing, living structures, PoC additive manufacturing of acellular, non-gel, synthetic, non-factor-containing biomaterial implants is within a much closer future.
As non-PoC, mass-produced medical products comprising these types of 3D-printed tissue regenerative biomaterials continue to gain acceptance and are more frequently utilized, they can be directly integrated within the existing and maturing PoC manufacturing workflows and processes, allowing for the rapid fabrication of patient-matched implants. This is possible because these specific types of acellular advanced biomaterials do not require any specialized equipment or handling techniques beyond what is currently being utilized in PoC additive manufacturing. Applications for these types of implants range from boney to simple soft-tissue (peripheral nerve, cartilage, fat) repair and regeneration. As the technologies advance, additional complexities will be integrated, allowing for multi-tissue repair, integration of cells (autologous, allogenic, or fully engineered), and eventually creation of structures intended for repair extreme tissue and organ injuries or full tissue or organ replacements.
With the integration of PoC manufacturing workflows and processes with developing advanced biomaterial technologies, both the near and distant futures of medicine are incredibly exciting. However, this medically revolutionary future is not guaranteed and a number of non-technical challenges must still be addressed and overcome. For example, who will pay for these advanced regenerative technologies and will new reimbursement codes and processes need to be put in place? How will PoC manufacturing of tissue regenerative implants, acellular or cellular, be regulated? As these technologies advance and the engineering, medicine, imaging, and other disciplines become necessary for successful PoC manufacturing, what does the workforce look like, and should new medical doctors and engineers be specifically trained in tissue/tissue-regenerative implant design and fabrication? In short, do we need a new type of medical professional? These are not challenges that can be addressed by a single individual or healthcare, private, or government entity. They require concerted, selfless efforts among all relevant parties. If we can do this, patients will benefit greatly, and we gradually enter into an entirely new age of medical treatment and care.