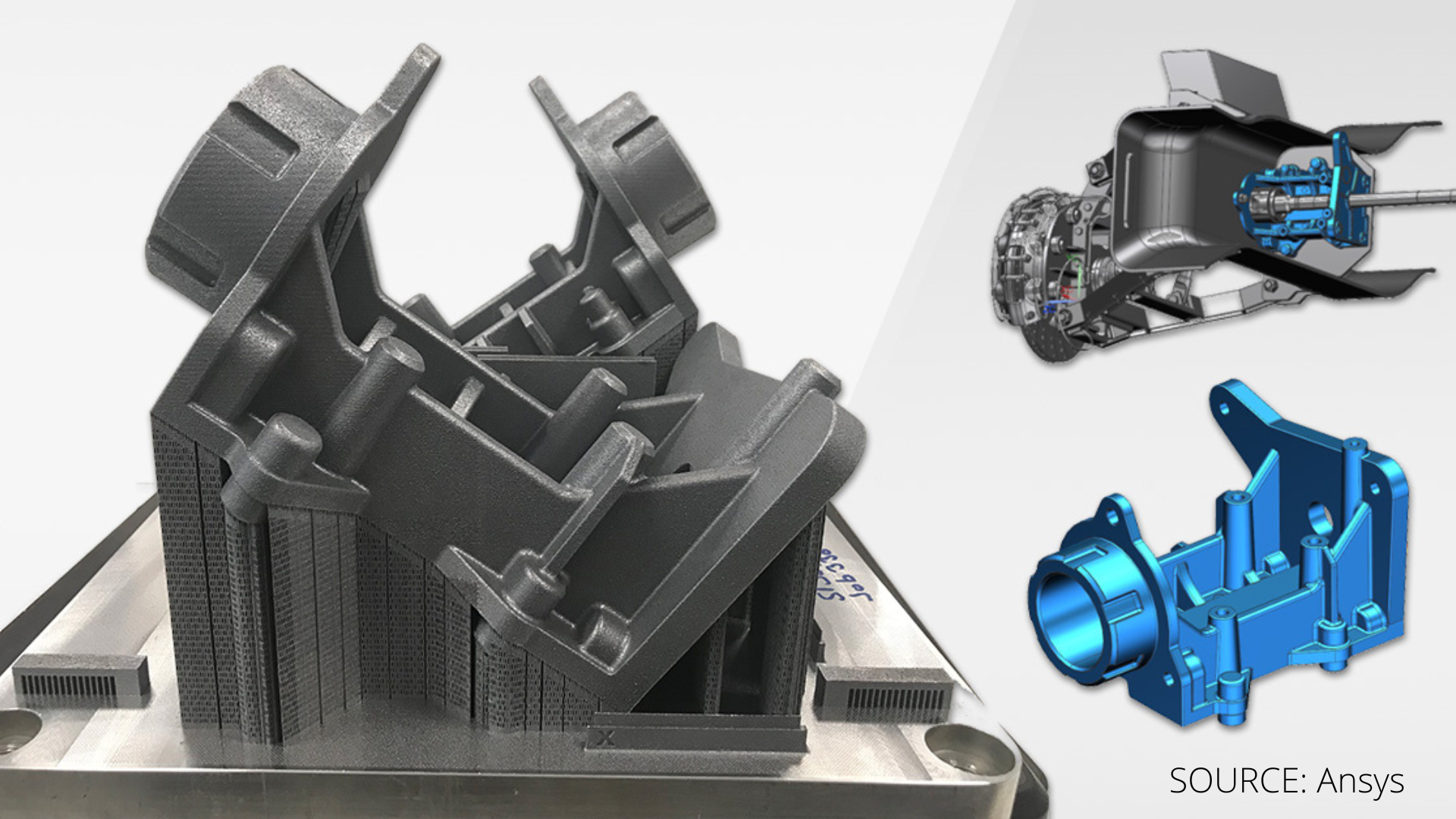
You may have noticed an increase in those fat tire bicycles in your community. Most often, they are electric bikes. These E-Bikes are catching attention in no small part thanks to advances in 3D modeling and simulation software. Manufacturers of two, three, and four-wheeled models are, like just about every product maker, searching for cheaper, lighter, faster (to make), and stronger products. Modeling analysis and simulation software is making it possible for just about every manufacturer to change or improve their product lifecycle.
Generative design is probably the best-known method for improving 3D manufactured parts, often used for lightweighting. Using AI, simulation, and modeling, a designer can input requirements to generate optimal designs. This process can create designs that use less material thereby creating a lighter part that meets performance requirements. Use of lightweighting is critical in several areas including those needing fuel efficiency like aerospace and automotive.
But what else can modeling and simulation software and tools do?
After reading about E-bike designs, I wondered about what advanced features modeling and simulation providers were adding to their tools. Well, that sent me down a deep Google rabbit hole, so to speak.
I landed on a 3D metal printing (because metal has always fascinated me) concept page from Ansys that gave a quick summary on Powder Bed Fusion (PBF), Directed Energy Deposition (DED), and Metal Sintering, to name a few. Years ago, I spent time with the well-known 3D experts at the University of Louisville. They explained how creating a reliable and predictable process was what production-level users needed, but that it was difficult to do on the first try, with tools available then. It appears that the Ansys software has the ability to simulate and then compensate for deformation in the metal AM build process.
Most importantly, it led me to their case study resource page and making a better race car.
- Additive Processes: Ansys Additive Manufacturing
- Case Study: Framing a Lighter, Stronger Race Car | Additive Manufacturing
In just a short time, I found valuable, but less common uses of today’s modeling and simulation tools, that can save small and large manufacturers money, time, and materials. Here are a few:
- Build failure prediction
- Support removal (planning for and reducing post-processing is a big deal)
- Nesting / packing
- Parameter selection
- Build time estimation
- Printability
- Post-processing preparation & time estimation
- Build cost estimate
- Improve workflow & performance results
If you want to keep up with me, or down with me, into the rabbit hole, and you are into bikes (or process improvement), you might enjoy how German company, Krause DiMaTec, makes an e-bike that is 55 percent lighter through additive manufacturing using MSC and Hexagon simulation and test solution software. Case study at end of post.
A quick detour from bikes and cars, if you want to see a company start and execute from the ground up with modeling and simulation software, take a look at Impact Footwear – they created a 3D printed, fully-customized flip flop (plus it is environmentally-friendly). They went heavy on advanced modeling and generative design using the cloud-based nTopology platform.
Back to bikes — Marco Antonelli, Engineer and Industrial Designer, brings another great example of incredible design from the cycling world with his revolutionary handbike. Yes, you read that right, a handbike is a bike you pedal with your hands and arms. Para-cycling has become one of the most popular and recognizable sports for the disabled covered by the media and Antonelli leveraged modeling and simulation tools from PTC Creo and Ansys to build the handbike.
Often, leveraging modeling and simulation tools to their full potential means that a manufacturer is exploring what’s known as digital transformation (in a nutshell, moving as much of your business into the digital realm as possible). Siemens recently released an ebook on this topic for small manufacturers considering or diving deeper into AM for many of the benefits explored here.
Additive Manufacturing is seeing strong growth again, despite decreases from the pandemic, thanks to massive advances in machine development as well as in metal, polymeric, and bio materials. As AM users increasingly leverage modeling and simulation software tools for topology optimization, generative design, and tactical flow for AM parts (as in build direction, supports), the growth will continue to surge in 2022 and beyond. If you would like to see more examples of software advances, get in touch with me and maybe we can do another post like this focused on different industries or use cases.
Resources mentioned:
- Ansys Case Study: Framing a Lighter, Stronger Race Car | Additive Manufacturing
- Hexagon (MSC) Ebike Case Study: Generative design provides and easy ride for e-Bike manufacturer with 55% lighter design for additive manufacturing
- nTopology Flip Flop Case Study: Impact Footwear Brings to Market Customizable Flip Flops.
- Siemens: Small manufacturers save big with digital transformation [EBOOK]
- For more on lightweighting in action, check out Mark Crawford’s article on ASME: 3D-Printed Lattices Optimize Strength-to-Weight Ratios
- The Handbike of the Future is Designed with Creo | PTC
Additional Resources:
- Case Study from Boeing: Development of Model Based AM Enabled Thermal Technology for Aerospace Applications
- 2021 Technology Roundup: Software