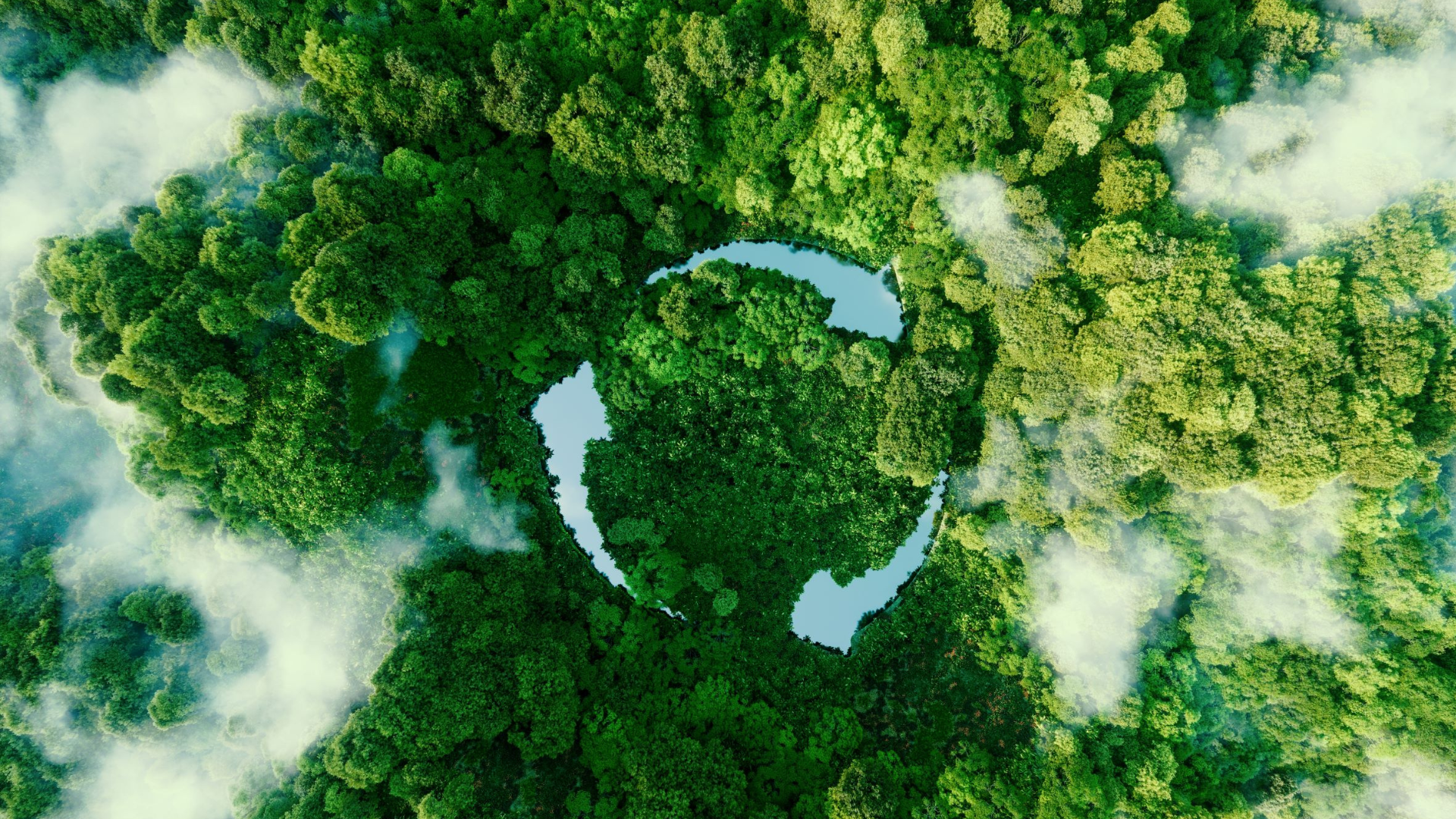
Additive manufacturing has the potential to play a role in each step of the circular economy. Sherry Handel, Executive Director, Additive Manufacturing Green Trade Association (AMGTA) sat down with Marie Langer, CEO, EOS to discuss what that means and in ways AM can enable more sustainable manufacturing.
Sherry Handel: Many say AM has always enabled sustainable applications, but what really is sustainability from your perspective? And could you share some ways in which you’ve seen this realized in the industry?
Marie Langer: We strongly believe we can contribute with our technology to make the world a better place. We see AM as a real responsible and sustainable manufacturing technology in production, which contributes to less material consumption, less overproduction, and less waste overall. In AM, every one of us can contribute so much. At EOS, we can influence three levels. Using the technology to look at resource efficiency, extended product life, and inventory waste reduction. Spare parts on demand is a very important area of concentration. We also have the humanity level where, especially in the medical field, we can do a lot with our customized, individualized products that can be realized for patients, or also doctors, to improve patient care. On a corporate level, how can we really reduce the ecological resource waste? How can we make sure resources or materials are not wasted? We can reuse it and we can improve the whole waste management. One great example is at Airbus. In the A350, we have this locking shaft for the aircraft door where we can actually really reduce weight by 45% while keeping the same robustness. We can save 25% in production costs by reducing material usage and assembly times. There are many other things I could say, but this is a great application example which is already benefiting today to become more CO2 neutral.
S.H.: There’s a huge fuel savings when you’re lightweighting aerospace parts. You have the fuel savings and carbon emissions reductions. It’s a really great example of sustainability. What are EOS’ corporate social responsibility goals? How are you planning to measure your performance in relation to your employees, customers, and other stakeholders?
M.L.: Everyone in the industry is looking into that right now, not only our industry, but in the world. How can we fight climate change together? Sustainability our company purpose. We call it responsible manufacturing, because we believe we can establish responsible manufacturing as the new normal in a world that is still adapting to the realities of climate change. This needs a holistic approach. We started by hiring a sustainability manager to make sure we put it on a strategic level. We are carrying out a comprehensive material and life cycle analysis in polymers where we can see that AM is bringing better sustainability results compared to conventional manufacturing. We plan to publish our CR report with very clear KPIs.
S.H.: The EU has some really interesting carbon emission reduction goals of at least 55% by 2030. How does this new EU climate law impact EOS? What does it mean in terms of your goals and what you’re planning to actually initiate and to measure?
M.L.: We feel it’s an important step towards climate neutrality. It’s providing a framework for all of us to really work towards. It’s really time to back up these ambitious CO2 reduction targets with bold measures. We want to make sure that we’re also pioneering in the industry with that. We were picked as one of the 50 sustainability and climate leaders this year. This law is important to also make sure that our customers are setting the right targets and we can move towards climate neutrality altogether.
S.H.: For United Nations Sustainable Development Goals, how are you planning to tie your performance into those goals? Which ones have you identified as being of real concern to focus your efforts?
M.L.: These goals are a great starting point for every business leader to tie what do you to overarching goals. We picked topics we feel are important for our industry and for what we want to do and the culture and values we work on. Gender equality is important. We work to improve diversity, which is not related to sustainability, but the social goals. Making sure we provide decent work and economic growth, we offer fair wages, secure workplaces, respect for human rights, and not doing business only, but business with purpose. There are goals for technology, industry, innovation, infrastructure, but also responsible consumption and production. Partnership for goals is also important topic. We believe establishing AM as a responsible manufacturing technology, will be an effort of many different players and initiatives. This is integrated in the things we do.
S.H.: How will you measure, evaluate and report on your goals?
M.L.: The challenge for us was to really understand where we stand, looking at clear data. If you have the data of the status quo, you can really decide on, “Where do we need to improve? Where are we really good already? Where do we maybe have opportunities to leverage even more?” Collecting the right data, for specific applications and industries, life cycle analysis, is important to set the right targets. Our sustainability manager together with cross-functional teams, customers, and suppliers, is working to make sure we have the right baseline.
S.H.: Benchmarking is key. How did you initially get your employees involved with sustainable production and processes? Are there any lessons learned in building a culture of sustainability that you would like to share?
M.L: Very early on, there was a group of people that voluntarily came together, to emphasize what we can do. It wasn’t strategic. It was understanding what we can do. With taking over, I made the other shareholders, my family one condition, “I will only take over this company if I can make sustainability the core of what we do.” I realized in conversations with my dad, this technology can be a green solution in the manufacturing. It’s a raw diamond now. We need to make sure it’s unleashing all the potential that we see. When I started, we decided we want to work on our purpose and understanding better how we can weave in sustainability in this core. We all employees part of creating this purpose.
S.H.: Do you have any advice for anyone looking to have more sustainable operations? What would you suggest what could be their first or second step?
M.L.: You need to get people in who understand what this means. Get involved with experts. You don’t need to recruit all of them right away. They can be freelancers or people you know in your network, or initiatives like AMGTA. We’re also very happy to be partner of this initiative. To start, collecting data is important. You really need people who understand how to collect data. These are very holistic, complex things. It’s not functional, it’s cross functional and cross interdisciplinary. And, make sure people who’re in the company really want to do it.
View the full discussion here.
NOTE: In June 2022, Sherri Monroe took over the position of Executive Director at AMGTA.