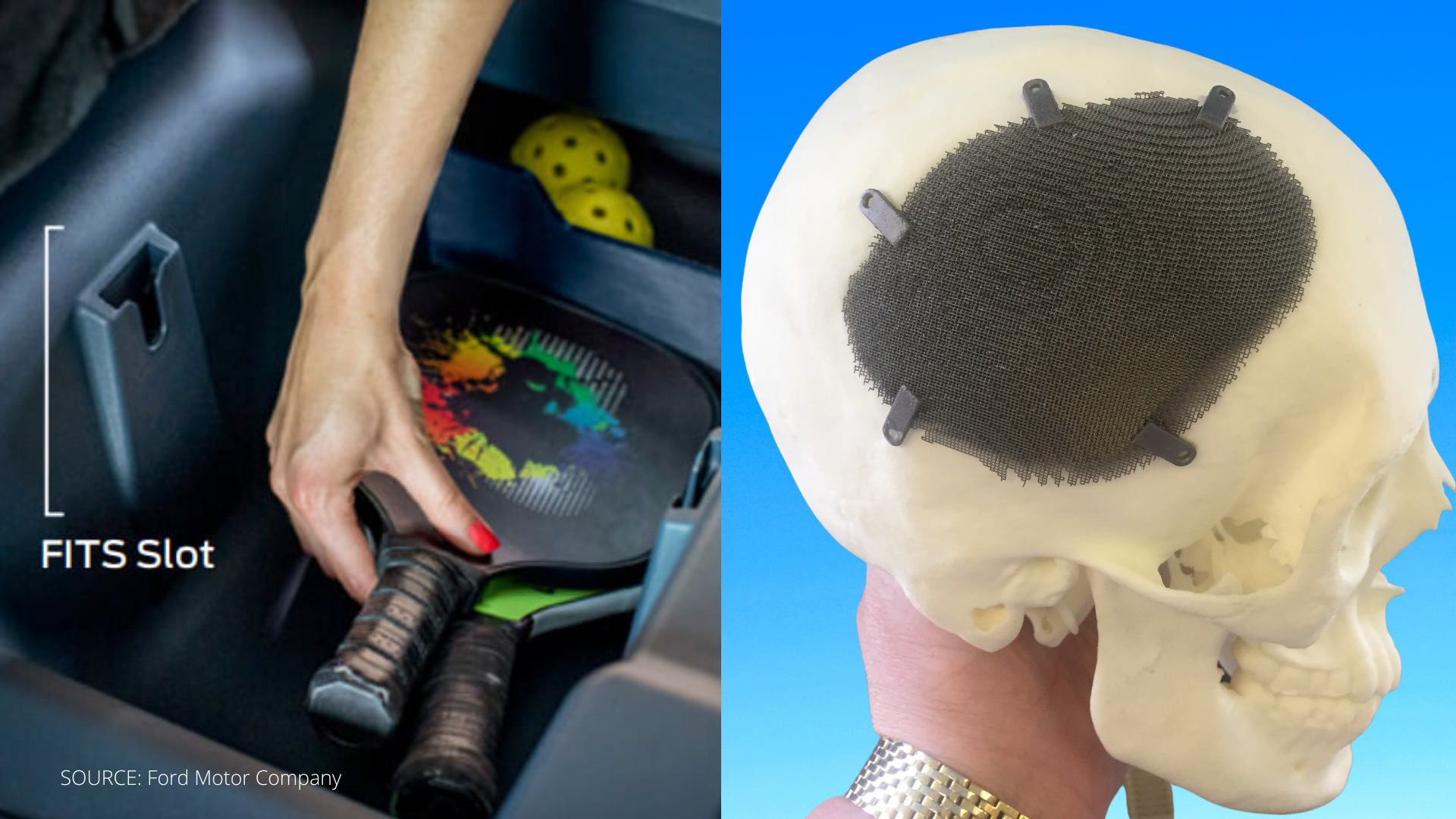
Steve Jobs is famously known for his thoughts on customer choice — saying “that’s not my approach. Our job is to figure out what they’re going to want before they do.” For many years in 3D printing circles, the idea that a digital process would allow customization or personalization at a mass scale, would largely nullify Jobs’ philosophy.
Mass customization and personalization are quite different, however, from a manufacturing perspective. Within additive manufacturing, personalization is often seen, but mass customization less frequently.
While additive manufacturing allows for more efficient methods to create small batches and even one-off production, the idea of mass customization has not been fully realized. Today, we see more examples of consumers having the ability to personalize products.
According to Juha Tiihonen and Alexander Felfernig writing in the Journal of Intelligent Information Systems, “Mass customization as a state-of-the-art production paradigm aims to produce individualized, highly variant products and services with nearly mass production costs. Personalization technologies can help to alleviate the challenges of mass customization.
One could suggest that personalization is a valuable approach within mass customization. On the consumer front, we see individuals customizing their eyeglasses, orthotic shoe inserts, or even their Ford Maverick pickup truck via the Ford Integrated Tether System (FITS) that allows you to download various 3D models to print on your own 3D printer or using a third-party provider.
Luxury car maker, Bentley Motors, started using AM for personalization in early 2000 with personalized passenger features including a makeup mirror and table. Less than two decades later, they are investing £3 million to double their 3D printing capacity at their Crewe factory with the intent for more customer-personalized components as well as low volume manufacturing of specific parts.
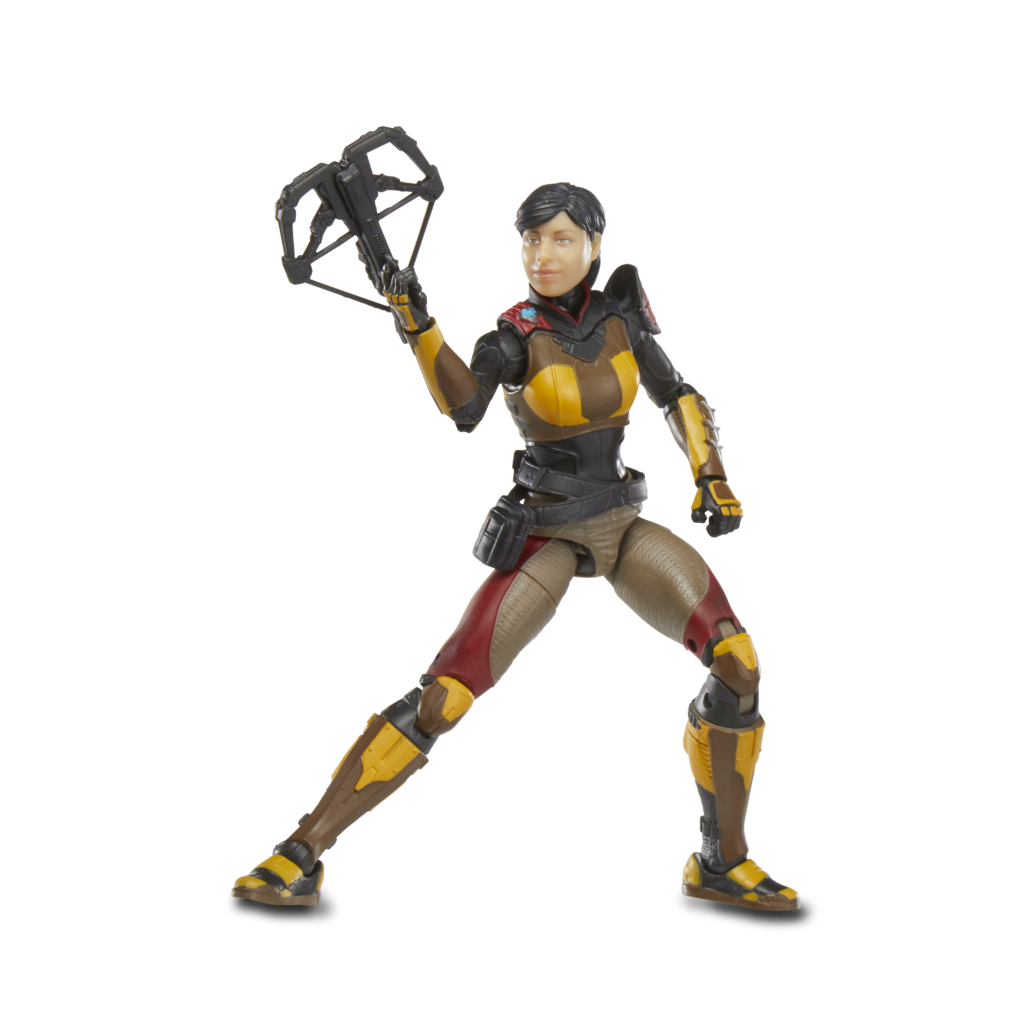
One of the biggest names in toys, Hasbro, is also a pioneer in 3D printing, particularly in mass personalization. Since 1995, the company has used 3D printing for prototyping as well as attempting various personalization efforts over the years. Recently, the company teamed up with Formlabs to create a hybrid manufacturing approach called the Hasbro Selfie Series. A special 3D scanning app called Hasbro Pulse allows consumers to scan their face, matching skin color and hair that is used to create a 3D printed head. This is then attached to an injection molded action figure body to complete the figure.
Within the medical field, huge advances are made possible through AM. Medical imaging, together with 3D printing, has long held the promise of patient-specific devices (one could view this as “personalization” on steroids). For many years, this had been limited to point-of-care produced items like anatomic models, assistive devices, surgical guides, and cases for in-ear hearing aids.
Hearing aids may be the earliest example of mass personalization, more accurately called patient-specific or patient-matched devices. Siemens introduced the first hearing aid case built using stereolithography in 2000. By 2004, it became the industry standard for in-ear hearing aids. Today, 99% are produced using AM. Yet, molds of a patient’s ear canal is still the primary method to gather data. This mold is then scanned to create the digital file. Over time, scanning advances should make it possible to remove the mold process, since it is hard to match direct 3D scanning of the ear for accuracy (and reducing steps, and error from handling of the mold).
Orthopedic implant manufacturers have produced patient-specific surgical guides for several years to kit with their joint replacement implants; think hip and shoulder replacements. At least 2 devices designed to be patient-specific have received FDA clearance
Dental prosthetics and other advanced procedures have always been patient-specific, but 3D is speeding up that industry as well. Dental implants, such as crowns and bridges, could sometimes take months to produce with lab dental technicians working by subtractive methods. The availability and use of intra oral scanners has made a fully digital dental process possible, more precise, and faster.
The high value of additive makes these patient-specific aids and devices impossible to produce by other methods. Consumers, patients, doctors, and technology experts are looking for ways to achieve a new level of personalization through better digital systems integration – from gathering patient data digitally through delivery of the final product. Naturally, for AM to scale, we need faster builds, through reliable and predictable processes and improved workflows that remove manual intervention.
Steve Jobs may have believed he could know what customers wanted before they did, but he couldn’t outrun or outthink the millions who know what they want or know very specifically how they want to change and personalize a product with today’s 3D printing approaches.
For more information on personalization, join us at the AM Medical Summit.