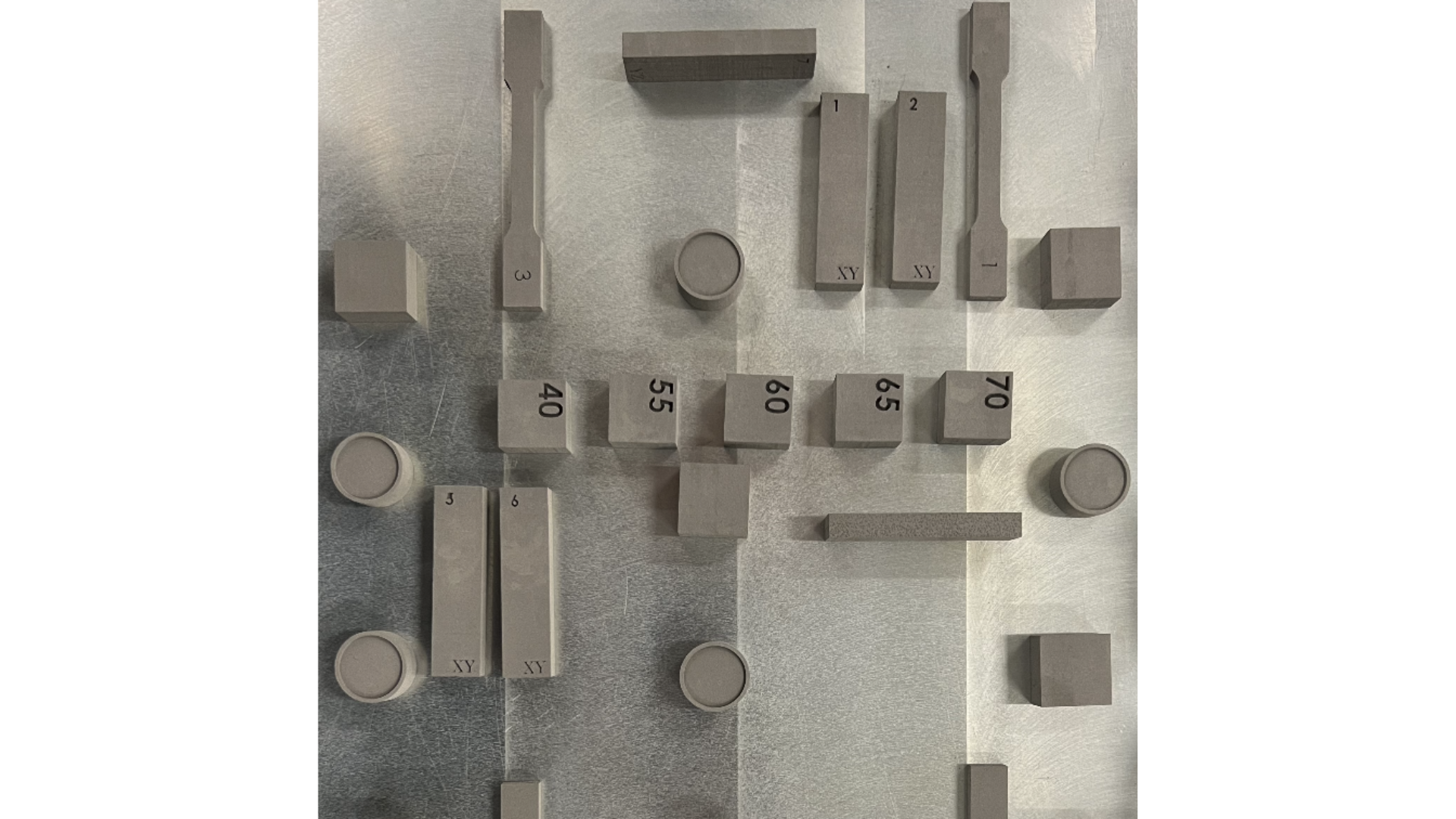
FREMONT, Calif., Sept. 13, 2022 — Uniformity Labs announced the availability of its ultra-low porosity 17-4PH stainless steel powder for the Desktop Metal Shop Pro Binder Jetting (BJT) platform, an advanced metal powder that delivers superior material properties, sintered part geometric accuracy, process yield and print uniformity at highest throughput.
Developed by an in-house team of world-leading materials scientists and 3D printing innovators, Uniformity Labs’ ultra-low porosity 17-4 PH powders exhibit a typical Tap Density of 5.33 ± 0.05 g/cm3. In an industry-first, Uniformity Labs provides insight into the geometric uniformity of parts throughout the part production cycle and considering all factors within a typical spread, print, cure, de-powder, and sinter.
A high and highly repeatable Sintered Density of 7.68± 0.03 g/cm3 and in-print brown density deviation of +/- 0.024 g/cm3 delivers uniform sintering shrinkage across the bed. Brown density across prints, batches, and in-spec process and environmental parameters averages 4.49 +/- 0.05g/cm3, delivering at better than 95% confidence levels inclusive of batch-to-batch, spread, print, cure, de-powder, and sinter sources of variation, a highly uniform sintering shrinkage of 15.17% ± 0.65% in the X direction, 15.66% ± 0.65% in the Y direction and 18.18% ± 0.63% in the Z direction. This low and unusually stable shrinkage allows the manufacture via binder jetting of large parts, up to 10s of cms in length.
The process stability reported is enabled by the low cohesion, low porosity powder that repeatably spreads uniformly across the build bed. The high brown densities result in up to 50% reduction in linear shrinkage relative to competitor materials and repeatably deliver 99-100% final part density for best-in-class materials properties. An additional benefit of low shrinkage is increased printer throughput due to greater use of the build volume. The highly flowable powder even further improves throughput by allowing repeatable fast layering, with a net throughput benefit of approximately 50% relative to non-Uniformity powders on comparable platforms, thereby enabling substantial cost reduction to be taken advantage of by parts manufacturers contemplating adoption of metal AM at scale.
Uniformity continues to deliver on its promise of No Compromise Metal AM for the industry. The benefits of its uniform, ultra-low porosity, high flow materials are not limited to print and sinter steps but also to secondary process steps, including de-powdering and sintered part finishing. The flowability of Uniformity’s low cohesion powders drastically facilitates de-powdering of high aspect ratio and geometrically complex parts with fine features and channels, preventing breakage during the de-powdering process step and enabling binder jetting of more complex, high aspect ratio parts. Furthermore, the unusually low variability in geometric shrinkage reduces the need for costly post-machining, as does the low as-printed surface roughness averaging 4.1um in the XY plane and 8um in the Z planes.
17-4 PH is martensitic precipitation – hardened stainless steel. It’s known for its corrosion resistance and high strength and hardness levels, especially when heat treated. 17-4 PH can be heat treated to various hardness and toughness levels, allowing users to customize the post-sintering properties of the alloy to suit a wide variety of applications, such as chemical processing, manufacturing machinery, and food processing.
“The application of Uniformity17-4 PH stainless steel for BJT delivers mechanical and process excellence for our customers who require materials that perform to the highest standard across each step of the production process,” said Uniformity founder and CEO Adam Hopkins. “Our powders deliver superior mechanical properties, surface finish, printing yield, and process stability, allowing one machine to do the work of several.”
In addition to materials that are already available, the Uniformity team is continually working to develop new materials and processes to make 3D printing accessible to all industries and applications.