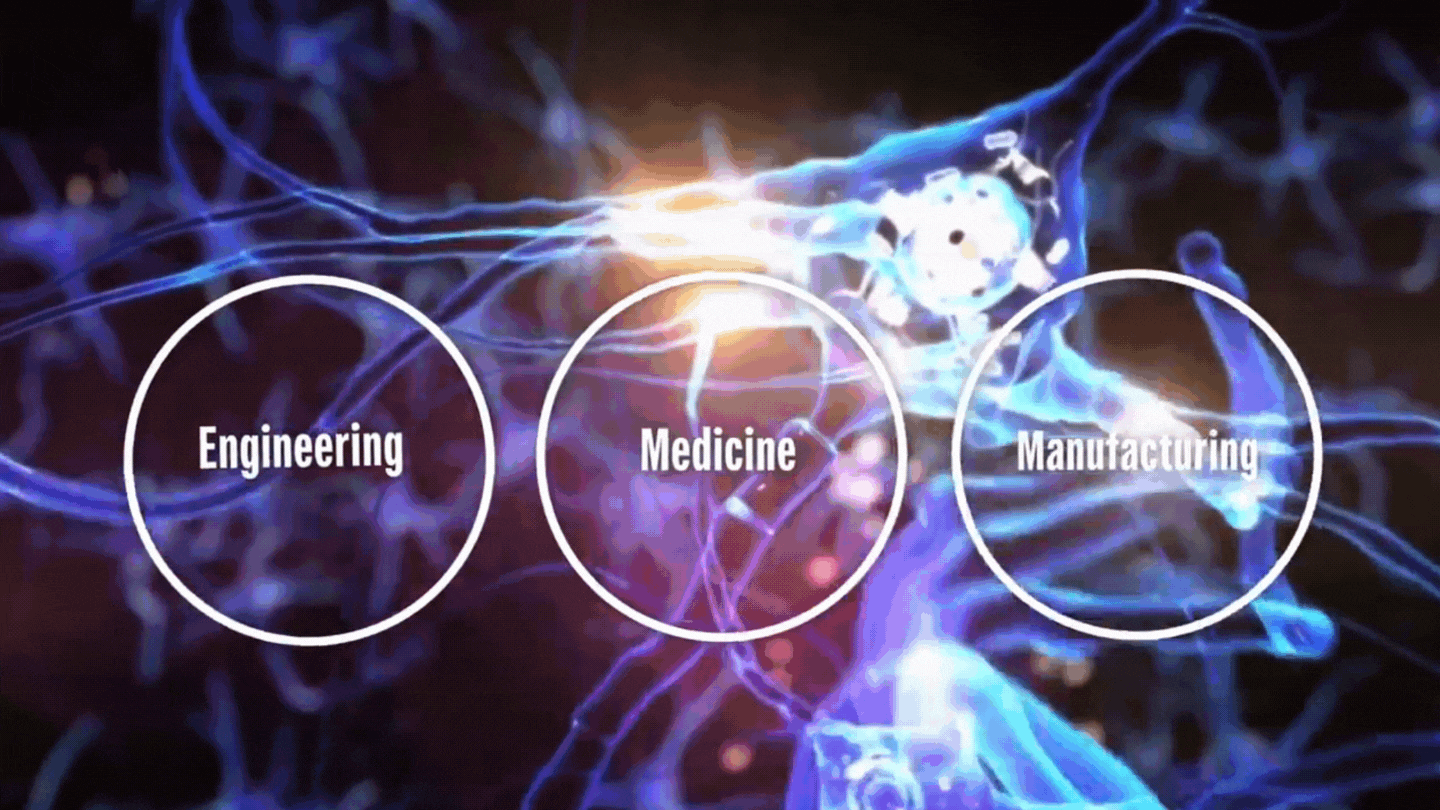
Precision medicine, by its nature, is personalized and a primary driver to improve patient outcomes. While many focus on gene therapies, 3D printing is not only more accessible, but has shown that is an enabler for personalization and can make a significant impact on patient care. From educational models and surgical planning to more complex personalized solutions, the medical community is collaborating to realize 3D printing’s full potential.
Collaboration is necessary to bring together diverse expertise in medicine, anatomy, biology, additive manufacturing, electronics, tissue generation, software, and engineering. All are needed to design and create devices and tools for patient-centered medicine. The community has seen Stryker collaborate with 3D Systems to pair biomedical engineers with surgeons to simulate surgery and 3D print surgical guides for a patient. PrinterPrezz already working with surgeons, is collaborating with Osseus Fusion Systems to develop new spinal interbody fusion devices.
GE Healthcare is a leader in collaborations, leveraging their diagnostics and imaging expertise to work with Formlabs, a developer of 3D printers and materials; CMR Surgical, specializing in surgical robots; and Decisio Health, a virtual care monitoring company. When the collaborations were announced, Kieran Murphy, president and CEO, GE healthcare said, “Healthcare’s next chapter will be written in part by emerging technologies like 3D printing, robotic surgery and virtual patient monitoring.”
Both the Stryker and GE Healthcare collaborations reflect the trend toward more integration with other technologies. In addition to surgical robots, 3D printing is often paired with simulation and augmented reality, used as patterns for silicone casting, and with electronics and sensors to create active devices. These specialized, often patient-specific devices provide feedback or transfers electrical impulses within the body. These multi-functional devices can rely on embedded or printed electronics or smart materials.
Not surprisingly, expanding applications of additive manufacturing in medicine is often dependent on materials. Recent developments include conductive graphene that can be printed on the micro scale, availability of shape memory materials for more AM processes, and the ability to directly 3D print silicone, a popular material for medical applications.
Silicone is widely used due to its resistance to a wide range of temperatures, tissues, and fluids along with needed mechanical properties, and demonstrated biocompatibility in devices. Until recently, creating personalized devices has relied on using 3d printing to create a pattern that can be used for silicone casting. While 3D printing using filaments on a material extrusion printer has been possible for a few years, ETH Zurich spin-off Spectroplast was the first to offer directly 3D-printed customized medical implants in silicone using a special-built stereolithography machine. Wacker Chemical now offers silicones for specially designed material jetting machines.
With all the possible processes, materials, and complex build capabilities, it’s not hard to see why integration of artificial intelligence and other software-based tools have been critical to more personalized medical devices. In the design stage, generative and simulation tools are critical to not only include innovative design features, but also assure a reliable build process and a final device that can meet material performance requirements as well as be cleaned for patient safety. Altair is one company that provides a range of digital solutions for additive manufacturing including topology optimization, simulation-driven design, and manufacturing simulation.
With all the technology integration and organizational collaboration, the biggest drivers and most active collaborators are the people. Individuals willing to share their experience, ask questions, and volunteer to create technology and standards roadmaps, develop CPT codes for new 3D-printed enabled devices, and actively develop consensus standards for the entire AM community. Several Standards Development Organization volunteers are involved in developing and published a wide range of standards including ASME V&V 40 for verification and validation of biomedical computational models and the in development V&V 40.3 for patient-specific models used in surgical planning. As technology advancements continue, collaboration is sure to continue as the medical community addresses the need for more complex devices and processes including 3D biofabrication of tissues and bones, and eventually the direct printing of organs.
Join the collaboration at the AM Medical Summit, November 1-3, 2022.