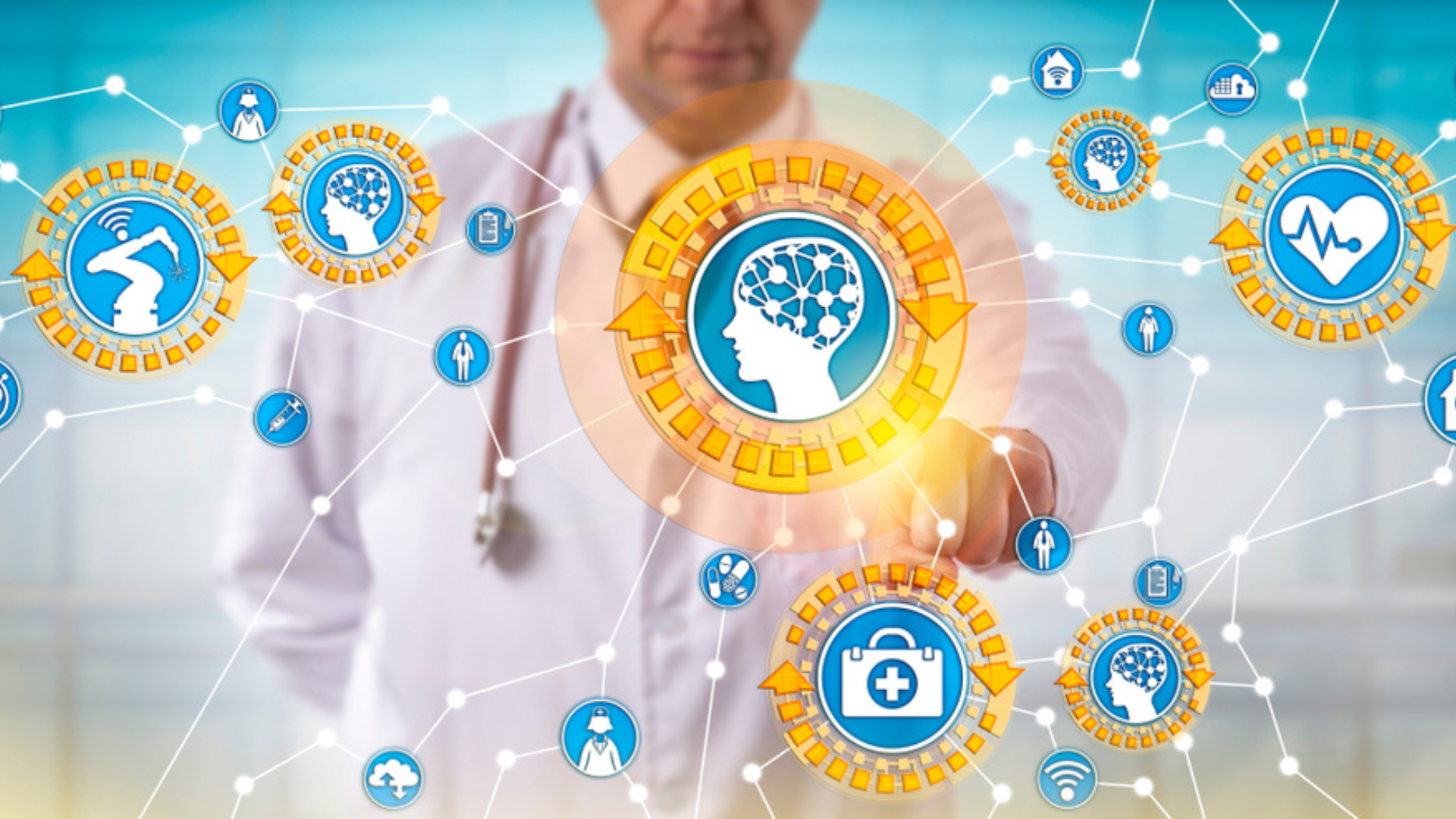
Three expert panelists delivered views and tips on overcoming challenges in development, prototyping and production of a growing range of wearable medical devices.
Leanna Levine and her team at ALine specialize in the development of microfluidics solutions for customers in particular incorporating 3D printing for proof-of-concept and rapid prototyping of lab-on-chip devices. “We’ve been working with a company based in Boston that’s developing a sweat patch that they’ve been commercializing with Gatorade. And that patch is currently available on the market,” says Levine. “We’ve been supporting that company and being able to scale up and manufacture components of that sweat patch, so that they can test the market early. And that’s the value that we bring to that product rollout.”
This textile sweat patch attaches to the skin and uses a combination of microfluidics, chemistry, electronics and software to measure and report the amount of water and electrolyte depletion by an athlete.
According to Levine, developing such products can be years in the making, and so patience is required. “It was about three or four years from the time the technology was initially conceived and then reduced to practice in a research laboratory. Then of course, it’s a matter of translating it, and developing manufacturing processes, understanding the failure modes in the system, and designing those out so that you finally get to a space where you can collect data on a large number of people, and look at the range of values you get from the chemistry.”
Articulate Labs uses 3D printing to develop physical therapy and rehabilitation devices, in this case, the KneeStim™ wearable device for rehabilitation of knee patients. These devices use neuromuscular electrical stimulation to promote muscle rehabilitation, but also combine AI and data collection to monitor bone position, range of motion, acceleration and so on. As importantly it achieves all of this during normal daily usage, whereas existing neuromuscular stimulation has always been performed in a stationary position. “The form factor that we develop for this device, has to be comfortable and form fitting, in order to have the patient continue to use the device,” says Rabinowitz. “But we also have to have it secure on the user, being able to stay in roughly fixed positions on the leg throughout flexion and extension.”
According to Rabinowitz, 3D printing has enabled much easier prototyping and production of the enclosures holding the sensor and electronics, and the beauty of CAD software enables faster iterations of the product. “Case in point,” says Rabinowitz, “We have a couple companies in Japan that are evaluating our devices and they’re giving us feedback about our patients… [Their] end users’ body types are going to be a little bit different from the average Americans. [They’re] going to need dimensions changed in a couple of ways. And that’s something we can do far more readily, which not just leads to improve patient compliance and better comfort, but also to a better product in terms of the therapy provided and the data that’s created.”
“We see two main directions [in the industry].” Says Jon Donner. “We see one trend of using the 3D printers that we build for faster prototyping, getting faster sensors, and so on, and helping in the development cycle. That’s very big. The second one is maybe more interesting, is the ability to do customizable devices.” Donner describes how his customers are researching AR eyeglasses that are adapted to each individual, to their specific optical issues and shape. “However, I would say if I had to choose one that’s the most interesting direction, and I think could be a real, open a real big trend, it’s the whole field of microneedles and microneedle patches,” says Donner.
Levine and ALine continue to take microfluidics and lab on chip devices to new levels with the extensive use of 3D printing for its clients. “We’ve been involved in an organization called Next Flex, and their focus is on developing printable circuits and components on conformal surfaces and stretchable circuits, things that will still perform under stress and strain of physical movement.” Says Levine. “They’re even going after being able to print things like an Arduino package.”
“I think the future for 3D printing is very large for a lot of these wearable products that involve some kind of a circuit that needs to be printed on a flexible substrate.”
You can become part of this conversation and more, by registering now for the AM Medical Industry Summit, Nov 1-3 2022 in Minneapolis, MN.