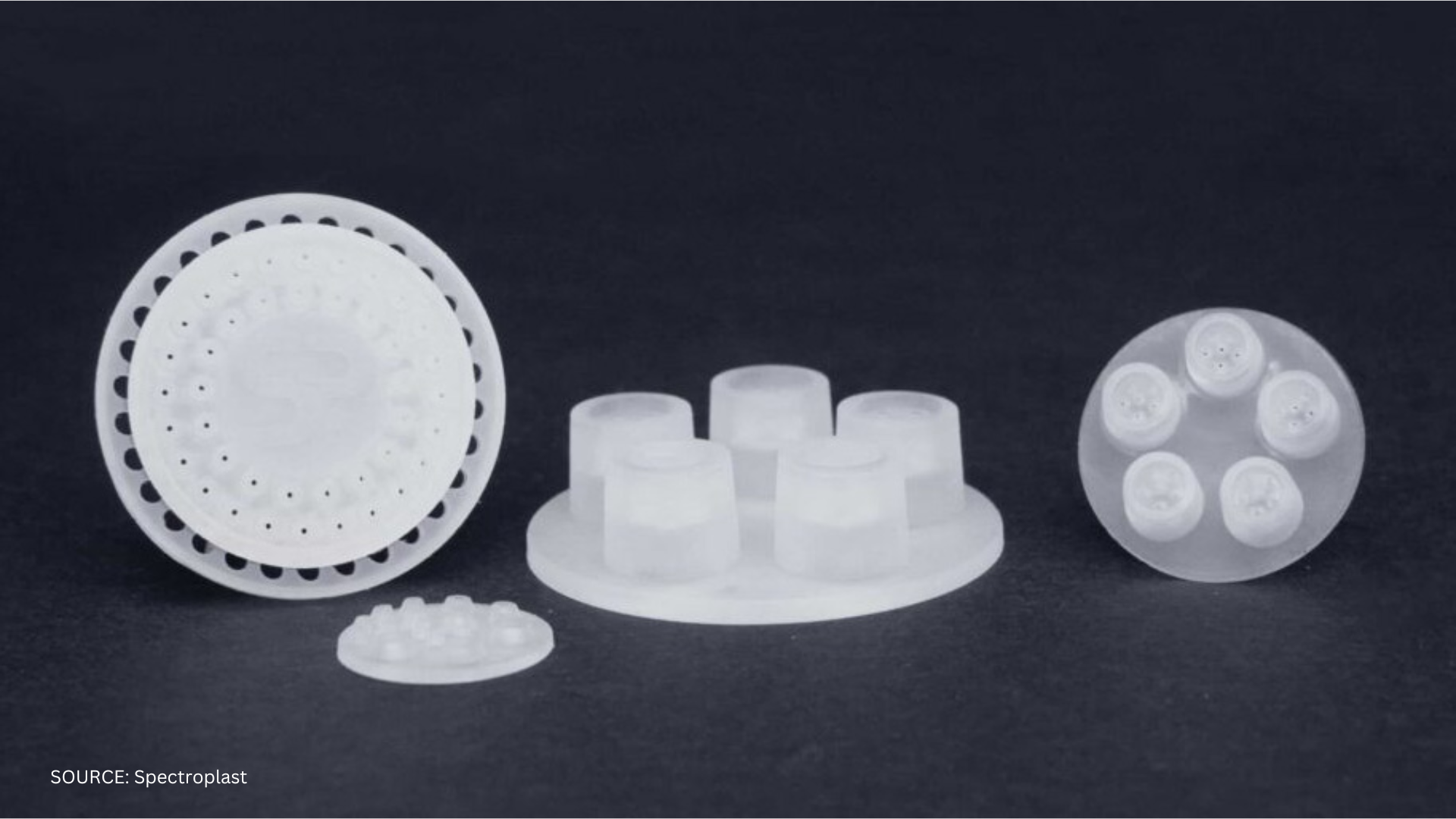
Silicone 3D printing is a discipline that has only seen visible advances in the last few years. Of course, indirect production of silicone parts using indirect additively manufactured (AM) shells has been viable for a much longer time but the limitations of the materials have made directly 3D printed silicone parts much more challenging.
A panel at ASME’s AM Medical Summit in 2021, moderated by Brandon Ribic from America Makes, in discussion with Petar Stefanov, from Spectroplast, and Dogan Yirmibesoglu, from Yale University, explored the newer advances in silicone 3D printing.
Stefanov is CTO and co-founder of Spectroplast which 3D prints 100% silicone materials and has founded a service bureau. Yirmibesoglu is a researcher at Yale University focused on developing next-generation 3D silicone printers, materials and software.
With new advances being made by companies and institutions, does that change the equation for the direct production of silicone parts using AM?
“Stop thinking within the mold,” says Stefanov. “Conventional methods of producing silicones, which are mainly molding-based, carry a lot of limitations, specifically, geometrical limitations, on the design. I would really try to encourage people to try to break those barriers and come up with much more complex designs than conventional injection molding would allow.”
“Silicone 3D printing is allowing people to [develop] more designs,” says Yirmibesoglu. “For example, we can now 3D print 17 channels inside one actuator – That’s really hard to make with molding.”
But even with these current advances, 3D printing in silicone still has some limitations or challenges. Namely gravity and also developing the predictive technology to enable viable parts despite the challenges.
“3D printing silicone has a bit of a unique, dual nature to it,” says Stefanov. “On one hand, you have the elastomeric properties of the printed parts, [which] can deform and bend and move during printing. And on the other hand, you’re dealing with a pretty high viscous raw material. That dual problem set is a bit unique as compared to other 3D-printed materials like acrylics or ceramics.”
Yirmibesoglu concurs: “In direct-ink-writing technology, you are trying to additively manufacture, putting new layer on top of the other one, while the previous layers are curing. So the gravity is a big problem here. I wish we could 3D print in space with silicone.”
But both experts agree that advanced software solutions can enable successful 3D printing of silicone even with gravity and challenging materials.
“When you are printing the silicone, the nozzle drags the silicone because it’s a material that is slowing down after extrusion, and curing and becoming solidified,” says Yirmibesoglu. “The behavior of the material must be incorporated with how the deposit material, especially in the geometrical shape. By combining the relationship between the tool path and the geometrical structure, by using software that can benefit from machine learning, would be really great to have.”
Where issues of physics can affect the success of a printed part, sometimes other technologies might provide an answer. Stefanov and Spectroplast use a vat photopolymerization technology that avoids the issues inherent with extrusion-based additive.
“With our solution the resolution of the finished piece is not so much defined by how precisely one can deposit the highly viscous material, but is rather defined by the resolution of light that will shine onto it,” says Stefanov. “And thus, we are able to increase the resolution of the printed pieces about 10 times higher than most of the extrusion-based approaches out there.”
Additive Manufacturing as an industry has always been shadowed by different cost equations to traditional manufacturing, which has made adoption slower across the industry, despite the added advantages of advanced geometric shapes. Will silicone 3D printing prove any different in terms of cost advantage? Can costs be realistic even with increases in scale?
“I think we have managed to develop a a more cost-competitive solution even than conventional techniques like injection molding, up to a certain volume of products per year,” says Yirmibesoglu. “That number could be between 30,000 and 50,000 pieces per year. Below those quantities, additive manufacturing tends to be more cost-effective due to the fixed costs that are related to conventional manufacturing. Namely, the cost of the tooling; the preparation of the process; the trial runs; and the scrap rate as well.”
So what does the future hold for 3D printing of silicone? All agree that it will see great advances and greater adoption as new freedom of design is realized.
“We will see different applications that we didn’t imagine, probably,” says Yirmibesoglu. “But for the future, I think with development of new slicing techniques with these materials, we will be able to be more closer to the entering into the human-combined designs, that we will see applications where a silicone-printed piece is being used in the surgery or being used as a replacement of human body parts.”
Silicone 3D printing is now available in North America at Protolabs. They are the exclusive U.S. provider of 20-60A durometer silicone. Get expert advice at this upcoming webinar.
To become part of this conversation and more, register now for the ASME AM Medical Industry Summit, Nov 1-3 2022 in Minneapolis, MN.