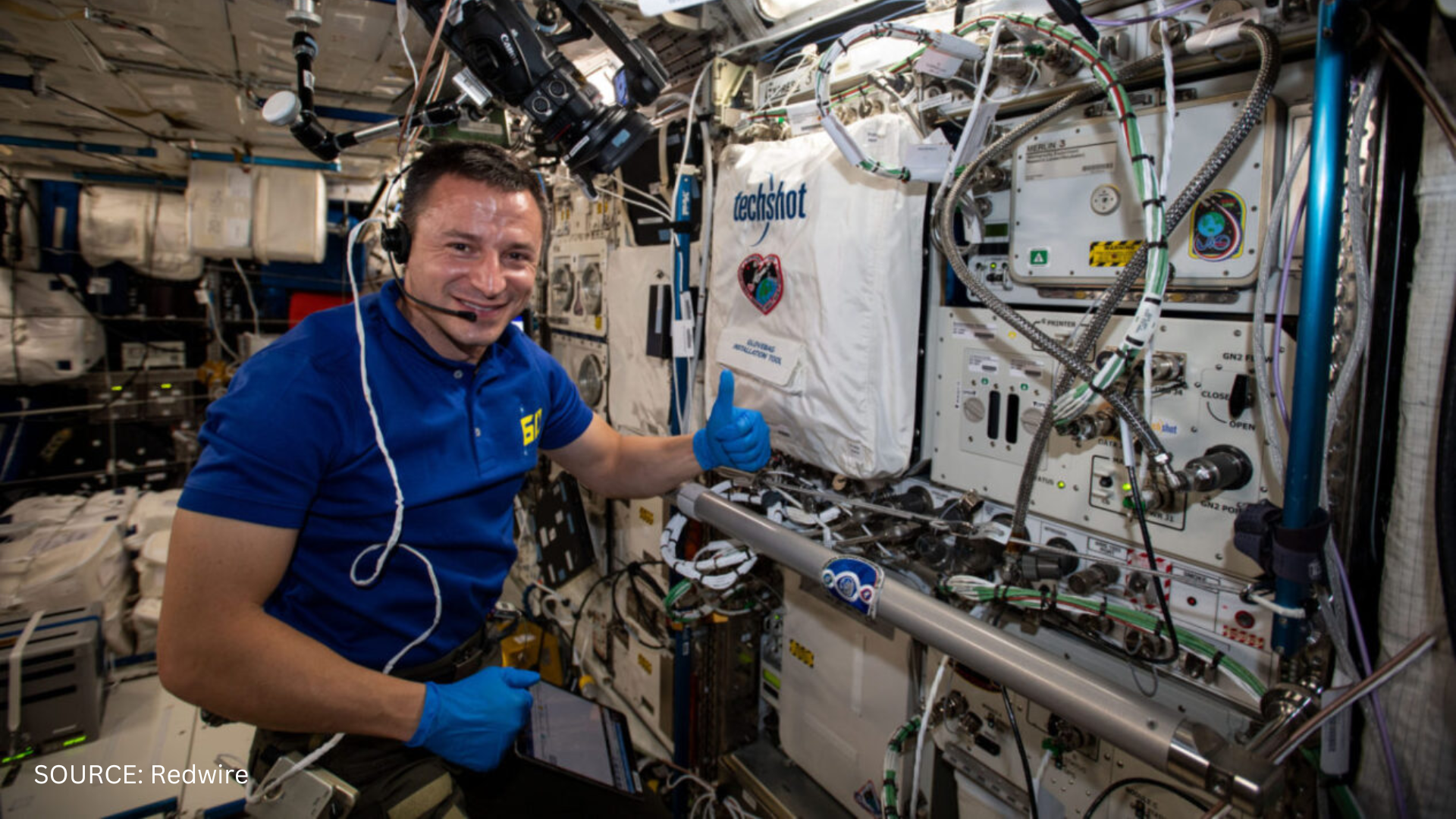
Many innovations developed for space exploration have impacted how we live: solar cells, better artificial limbs, CT scans, the insulin pump, wireless headsets and more. Research and development of 3D printing in space for micro- and zero-gravity is moving fast and will no doubt continue to impact our lives.
Dr. Eugene Boland, chief scientist at TechShot, now a part of Redwire, shared his team’s recent research in AM being conducted at the International Space Station.
TechShot was founded in 1988 to develop research payloads for the Space Shuttle program. Since then it has evolved to having its own research and manufacturing equipment on the ISS US National Laboratory. These payloads are mainly focused on 3D printing in space technology and are able to run experiments autonomously and remotely, with minimal user expertise.
“NASA is looking to pivot to long-term exploration, which really requires a paradigm shift in how they design and manufacture all their space systems,” says Boland. “They term it “in-space manufacturing,” which really looks at a number of concepts from sustainability to mission flexibility, because if you want add or remove capability without forfeiting the trip, you better have a way of adapting in real-time on demand, fabrication of critical systems, repair parts, and recycling.”
According to Boland 3D printing in space is a natural technology for such a mission.
“You can’t always bring the spares with you, and if you do, things still break, and some things are one-time use, and would be great to recover that launch material and be able to use it for something else, he says. “It’ll decrease NASA’s reliance on overbuilding and spare parts from orbital replacement units now to component-level repair… with the end goal of decreasing launch loads.”
While TechShot had previously only focused on parts production, it pivoted to bioprinting research and in 2019 launched the BioFabrication Facility, or BFF, to the space station to experiment with 3D printing of tissues in organs in microgravity.
Why do bioprinting in space? It seems hard enough to do it in gravity conditions, so why would space be any different?
“Well, for one, the absence of gravity opens up a lot of 3D structure capability, but also things that you don’t always think of as being gravity-dependent, and that’s convection and buoyancy, so we can use a lower-viscosity bioink in cells and nutrients stay where you put them,” says Boland. “We don’t get thermal currents, we don’t have cells and other things settling out, so now, for the first time in bioprinting, we can print biology just for the sake of the biology, only what we need, where we need, when we need.”
Alongside bioprinting research in micro-gravity, TechShot is also working on innovations that will enable the development of a low earth orbit economy of in-space research. The cost of placing cargo into orbit has dropped dramatically, opening up space to non-governmental entities that previously could not afford it. TechShot has been developing a Multi-Material Fabrication Laboratory, known as the FabLab, which incorporates metal material extrusion technology, CNC milling and finishing, pick-and-place heads, in-situ quality control, and a micro furnace. It is intended to be available for other companies wishing to conduct research in space.
Fitting all that technology into an ‘Express’ rack, which is about the size of a phone booth, and being very careful about the very finite supply of power to run the system is where the innovation really comes in.
“The micro furnace is designed to be 12-kilowatt capacity and capable of debinding and centering a six-inch by six-inch by six-inch block of printed titanium 6-4 with operating temperatures between 600 degrees and 1450 degrees Celsius with a uniform temperature of within three degrees,” says Boland. “All this sounds great, but then we have to remember, there’s only 2,000 Watts available, so now, it’s time to be efficient.”
After much miniaturization, the result is a very compact, comprehensive metal 3D printing system that can produce high quality metal parts, fully post-processed, at high accuracy and at high speed.
“We have an XY position accuracy in this system of five microns with bidirectional repeatability of two microns at Z axis,” says Boland. “Time is always the critical factor, and in this case, we’re over 440 millimeters per second on the Z stage and our XY stage in excess of 750 millimeters per second. There’s nothing that is too fast for this printer because we want to extrude these materials as quickly as possible.”
So what do these types of innovations mean for life down here on Earth? Maybe it will result in a wider availability of viable organs for transplant? Perhaps a wider availability of metal parts, on demand, in orbit? And perhaps the possibility of significantly faster 3D printing in gravity?
Only time will tell.
Join the bioprinting discussion at the AM Medical Summit, November 1-3 in Minneapolis.