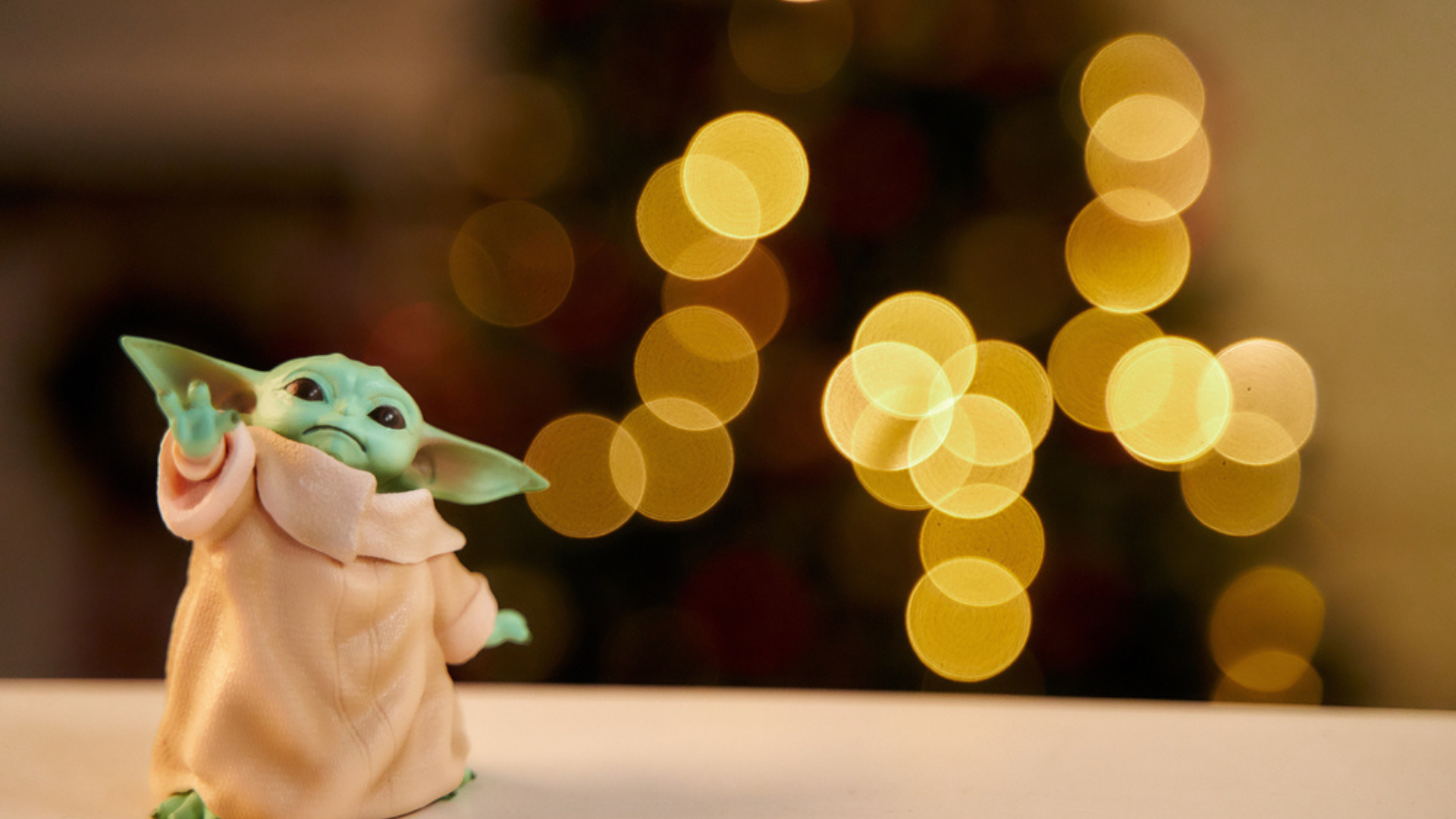
When it comes to 3D printing, there’s a lot of advice floating in the ether regarding best approaches to new projects. From investing in the technology in risk-averse sectors to learning the nuances of design for additive manufacturing (DfAM) and all the other lovely acronyms that go along with it, most people seem to want the answer to a seemingly-simple question: How do I do this?
In the face of all that flies something else: the bad advice. Let’s dive in there. How do we not do this? (And why are so many organizations seemingly following these guidelines?)
Research
Don’t do it!
Did you know there are seven unique ASTM-defined technologies under the additive manufacturing umbrella, each with unique capabilities in terms of materials, tolerances, and quality? Did you know that each of those seven processes can be further refined into additional, often proprietary techniques that can often be quite differentiated for similar-at-first-glance offerings?
Well, 3D printing is 3D printing. If it’s good enough for a Yoda head, it’s probably good enough for your project. Besides, calling a product “3D printed” is sexy. It basically sells itself once made.
Actual approaches
The decision to adopt 3D printing in a workflow is often not so much borne of the idea that “I want to 3D print this!” but, rather, stems from a manufacturing problem that requires a solution.
Understanding your needs, your challenges, your validation processes, and – vitally – what qualities a single solution would need to offer to produce what you need, when you need, and at the cost you (and your customers) need it is the first step. From there, if 3D printing seems to be a fit, you’ll often find it by narrowing down your own parameters.
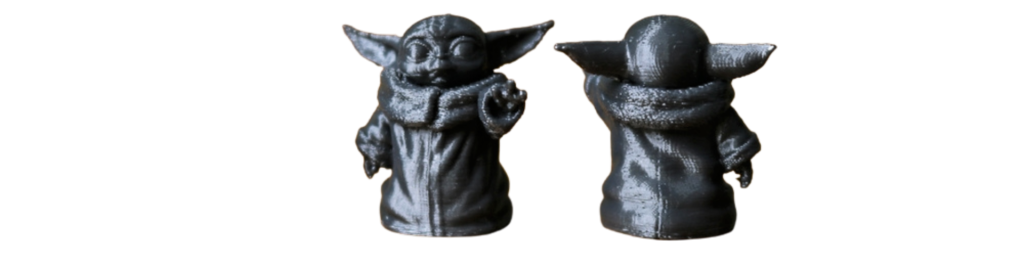
For example, do you have a high-value, low-volume project using an expensive material that you’d like to redesign, lightweight, and optimize? Sounds perfect for 3D printing, and those parameters will guide you to the right combination of software, hardware, and materials.
If, though, you need a lot of the same thing made – don’t 3D print it just because you can. Traditional high-volume manufacturing processes like injection molding are still often the best fit. Sometimes 3D printing may fit as a bridge process while a traditional technique ramps up, but don’t look for 3D printing to be your end-all-be-all every time.
Investment Questions: In-House or Outsource?
Both! Or just buy it all!
I want to 3D print, so I’ll get a 3D printer, you think. The logic seems sound. You can’t 3D print without a 3D printer, after all. Ignore that little voice whispering, “Or can you?” – how would it know what it’s talking about? You have a project or two, probably, and can figure it out. Just buy and install, there are some great “best 3D printer” lists out there, easy peasy to pick one out!
Conversely, what if you have a lot of projects but don’t want the mess of in-house production? Outsource it! Go to a service bureau or someone who knows what they’re doing; they do it all the time, after all. So have them do it all the time for you, even if your own team might mention you have the available budget, floor space, and souls willing to learn to operate new equipment.
Actual approaches
There simply isn’t a one-size-fits-all solution anywhere in manufacturing. For some businesses, in-house makes more sense than outsourcing ever will. With experienced teams, investing in owned operations that keep intellectual property and supply chain close in hand is the only logical way to proceed. Point-of-care 3D printing, for example, needs to be done at the point of care.
Teams looking at the capabilities of million-dollar machines but lacking footprint/budget/enough work to move toward ROI, though, may be wise to work with those service companies that already have that expensive equipment available to them. Take stock of what you actually need to accomplish and whether it makes sense to engage those who already have both installations and know-how. Increasing numbers of service bureaus are highlighting their validation processes, too, from ISO to ITAR to clean room facilities.
Design, Optimization, and New Ways of Doing the Same Old Thing
Just transfer your digital file to a new manufacturing process, it’ll be great
I have a part, I need the part, I’ll 3D print the part: again, easy peasy. Digital inventory means not having to stock physical shelves with physical goods, so when I need another of these legacy parts to repair equipment, I’ll just print another one. That’s what digital manufacturing means, right?
Actual approaches
We’re back to DfAM here. 3D printing isn’t a new way of making a wheel; it reinvents the wheel.
Take the time to step back, evaluate what you’re doing, what it needs to do, and whether it makes sense to step into areas like topology optimization, generative design, or other advanced design processes that appropriately apply new capabilities, new physics, and new geometries via new ways of making. A design file for a CNC-made part is just that; it shouldn’t be a 1:1 move to a new platform. You’ll get better results using a file designed for the manufacturing process you’re using.
IP and How to Lose It in the Cloud
Just throw it out there!
Everyone is talking about “the cloud” so we can trust that. These networked printers are super smart, so just throw your designs and notes online to share with your team…and whoever else can gain access. Go for it, your customers won’t mind.
Your legal team will also love this approach.
Actual approaches
Intellectual property is precious. Treat it that way.
More and more, the spotlight is shining on the issue of security in digital manufacturing processes. As critical-use parts are made, validation is a very serious part of the process – and so is keeping those parts close to the vest. Going back to point one on research, do your research here. New security solutions are arising all the time. Sometimes these are as simple as internal networking or more offline work. Often, encryption and security protocols can be baked into the design process, end to end. Find the best level of security for your specific needs, checking with trusted and validated providers. This is what will actually make your legal team (and your customers’) happy.
Operating Environments
OSHA says what?
Inert atmospheres, ESD flooring, ventilation, appropriate power supply: all I’m hearing here are expensive, expensive, expensive, expensive.
3D printing is getting easier, they say, so it’s a safe bet that everything for sale out there is plug-and-play. So plug it in, off you go. Just be sure maybe your will is up to date before going to work.
Actual approaches
Specialized equipment, as a rule, requires a specialized operating environment. There’s a perhaps surprisingly high risk of explosion or fire from improper material handling in a perhaps surprisingly high number of different AM processes. Ensuring that all due diligence has been performed before an installation is even begun isn’t a short process – but it’s a pretty vital one to have all the building blocks in place for safe operations from day one.
More standards, including safety standards, are evolving constantly in AM. One would be wise to adhere to them.
How Not to 3D Print
It’s easier than ever before to 3D print – but harder than ever to 3D print well. With, forgive the pun, so many layers of complexity at every stage of the additive manufacturing process, understanding what you’re getting into is the first critical step. Sometimes knowing what not to do helps inform the path to success. And, after all, isn’t 3D printing all about failing faster to get to the optimal results?
Join the discussion at the AM Medical Summit, November 1-2 in Minneapolis or one of the upcoming AM webinars.