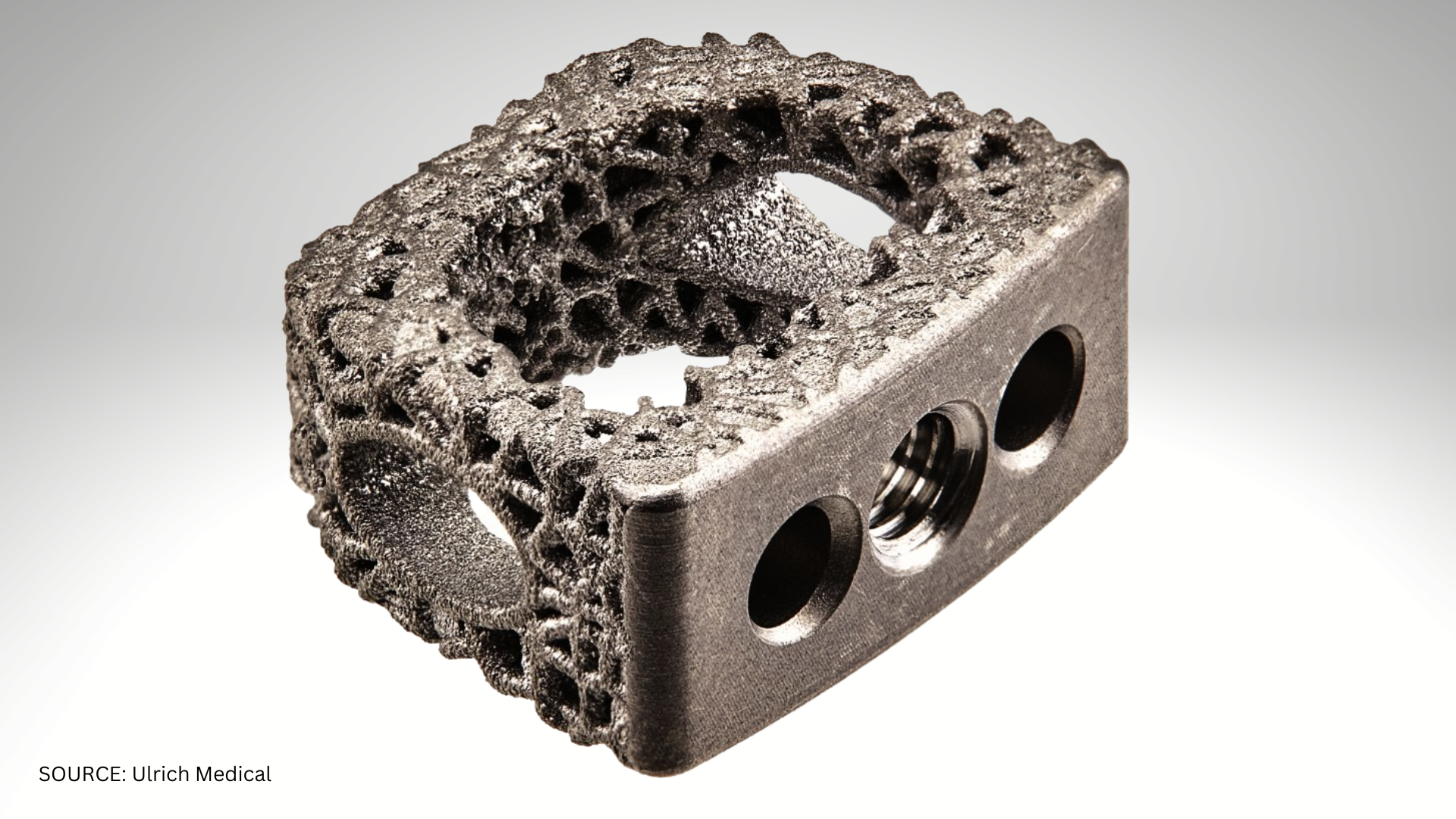
The medical device market has historically been one of the pioneer industries using additive manufacturing (AM) for production. In fact, according to FDA’s analysis of medical device clearances, additive manufacturing has been used in medical device production as early as 2008 (Ricles, L & Oh, S. RAPID, May 2014).
Most medical device types have focused on porous (or lattice) structures that are tailored to different anatomic locations to encourage boney ingrowth and allow an implant to become integrated into the patient’s body; or patient specific devices where a patient’s anatomy is used to create something that is unique to their anatomy. The most common use of patient specific workflows occurs for medical models, which help surgeons plan or visualize complicated surgical procedures, such as the separation of conjoined twins.
However, the vast majority of medical devices are not patient specific, and therefore it is natural to analyze when it is appropriate to leverage additive manufacturing over traditional manufacturing methods. Medical device volumes are typically much lower than consumer devices, for example, which makes AM potentially interesting for serial medical device production. especially as additive manufacturing systems become more efficient and can compete with production methods such as casting for joint replacement devices.
In many cases, considerations in designing for medical AM production is not different than the Design for Additive Manufacturing (DfAM) principals that can be applied to any other industry. This discussion is not meant to be a comprehensive review of DfAM, but rather a review of subjects that can be important or unique to medical device manufacturing.
There are several variables that can be adjusted with AM that may impact design. Common variables to consider are:
- Material
- Hardware/machine technology
- Layer thickness
- Energy disposition strategy
- Topology optimization
- Part consolidation
- Orientation
- Packing density
- Post-processing needs
- AM production of tooling instead of the final part
Although many of these variables may seem to be independent of the design itself, understanding how they contribute to the end product is important to an AM design’s success. If certain features need to retain an “as-built” roughness, as would be advantageous in porous structures for example, then orientation of the design on the build platform may need to be a consideration in the design. Or designing machining features into the “as-built” part may be advantageous to economically facilitate post-processing steps. For metal AM applications, can ‘supportless’ build strategies be implemented to reduce post-processing altogether or enhance certain unique design features?
When designing medical devices using additive manufacturing, there are some unique constraints. One of these is the preference to use known materials with some clinical history. The speed to market is typically longer and more expensive if a novel material is being used. However, limitations in material choices are not always as constraining when using an AM process as compared to traditional manufacturing. When thinking about a device or device feature it is important to consider the true purpose of what the feature is intended to do, rather than be fixated on a particular material property. For example, a known rigid material could be used to create an elastomeric feature, as is possible using DfAM principals.
A common design constraint for systems using powder feedstock, is how to remove powder that may be retained in complex structures or blind features. An additional step for medical devices is to demonstrate, with objective evidence, powder has been sufficiently removed, which can typically be completed in subsequent validation steps once a design is finalized. Another potential source of concern from regulatory bodies is inspection techniques for complex structures. Standards exists that can be applied to AM porous (lattice) structures (ASTM F1854-15), but as these structures become more and more complex, additional inspection techniques may be needed. The cost contribution of these techniques, which can be as advanced as micro-CT, may also need to be examined.
Another commonly missed opportunity for design to positively influence medical device manufacturing is designing to minimize post-processing steps. One way to do this is to consolidate multiple parts from an assembly or sub-assembly into one fully redesigned part. The more filetypes or production steps involved in making a final product in medical device manufacturing, the more processes you have to control, validate, and document. The time it takes to properly perform quality documentation is not insignificant, especially for new medical device manufacturers. Any steps taken to streamline these processes are advantageous from a business and a time-to-market perspective. While Design for Additive Manufacturing is an important consideration for any AM product, it can have an important impact on medical device design and manufacturing. Communication and collaboration between commonly siloed development and manufacturing teams are crucial to the successful application of medical AM design.
Join the discussion at the AM Medical Summit, November 1-2 in Minneapolis or one of the upcoming AM webinars.