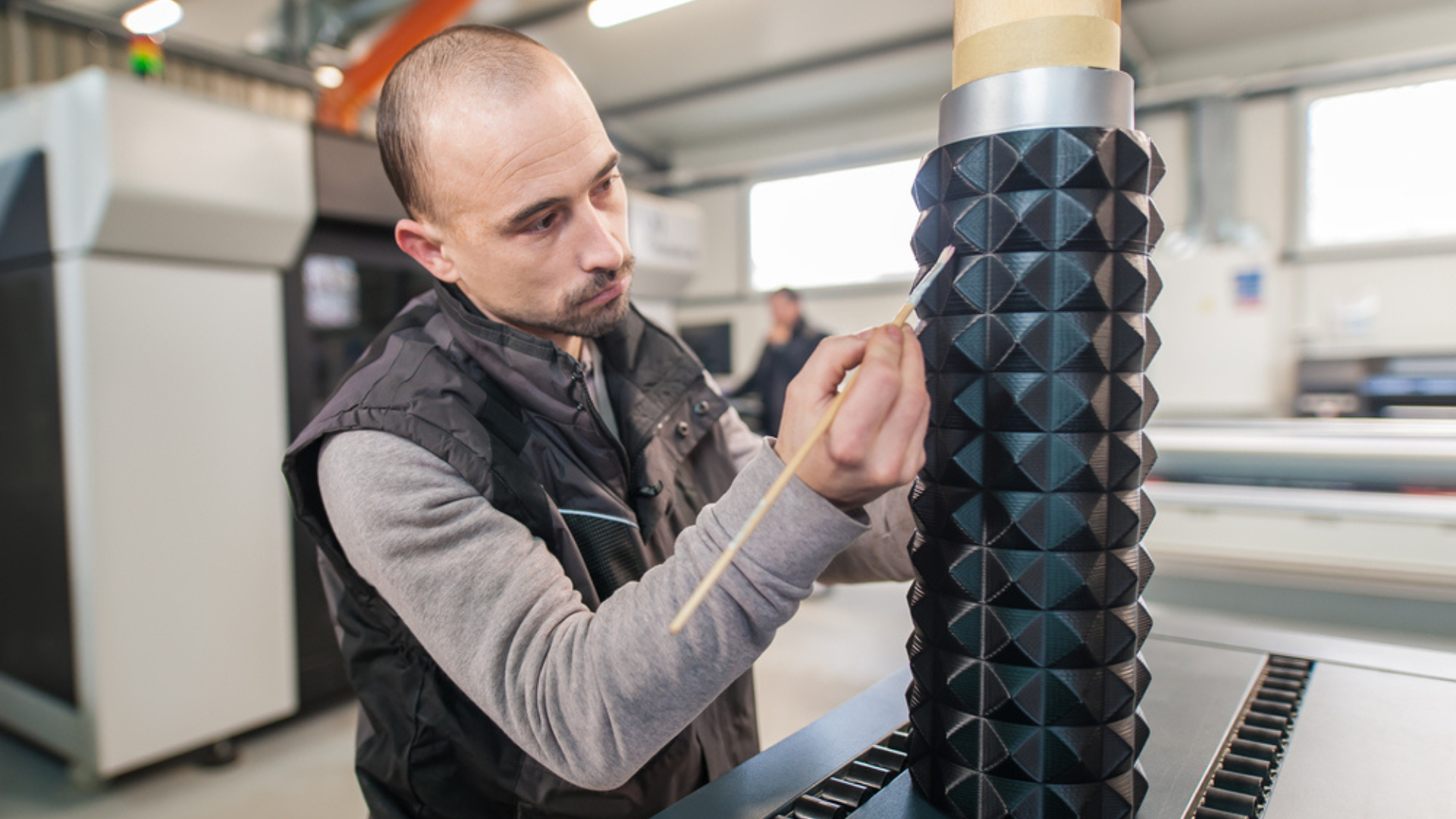
Post-processing of 3D printed parts has been, until recently, a topic that was often tertiary to the process of additive manufacturing. As 3D printing has become more industrial grade and starting to look at industrial part volumes, so post-processing has taken on an elevated significance, a part of the entire production process that, when badly planned, can cause delays, cost money and even engender part rejection.
In a recent panel session, Balaji Prabhu of Dentsply Sirona, and Gene Kulesha of Onkos Surgical, discussed strategies and tactics of post processing for both polymer and metal additive manufacturing.
The key point on which all panelists immediately agreed is that for industrial AM activity to be successful, the post-process activity has to be incorporated into the initial design and production plan.
Prabhu points out that in his field of dentistry that comfort and fit of dental products demands 30-50 microns of accuracy, and that faulty post processing could throw that off to 100 microns which is not acceptable.
“So what this really comes back to is, in terms of the dentistry or the dental 3D printed workflow, post-processing is not just an add-on. It is starting to become part of the printed digital workflow,” says Prabhu.
Post-processing techniques can run the gamut from manual and machine finishing, plus assembly, that have been used for decades in traditional manufacturing, through to new innovations necessitated by the unique technologies additive uses. Polymer 3D printed parts can often be quite easily finished using manual grinding and polishing. However, as part counts in additive increase, so mechanical finishing solutions are better for faster throughput. So vibratory tumbling systems are common for metal parts. CO2 and dry ice blasting systems are also common for finishing of parts. However, additive manufacturing often uses materials that are quite different to traditional manufacturing materials that bring new challenges for post-processing. One of these is metal powder.
With powder-based metal additive manufacturing powder removal is a critical aspect, not usually encountered in traditional manufacturing.
“Really the hard part in medical device printing of metals is really getting residual powders out of highly porous components, getting smooth surfaces on even non-porous components” says Kulesha. “And there’s a whole variety of different techniques and technologies that take out the powder, mechanically remove some of these satellites that can become later deleterious when they’re implanted.”
Manual powder removal is possible but brings inherent risks of inhalation or even explosion. Automated de-powdering is seen as both a safer option but also more effective in terms of cost and time spent as well as delivering repeatability. The process starts with initial vacuuming of powder inside the 3D printing platform. But the growing market in automated systems is delivering options for vibratory and oscillating platforms, as well as ultrasonic devices and then blasting. But it is not always foolproof.
“If you don’t get all the powder out of a powder bed fusion build structure, it’s really good to do a heat treat of some sort,” says Kulesha. “It will really center it or diffusion bond it onto the rest of the lattice structure [and] just gives you a little bit of an insurance policy.”
Heat treatment of metal 3D printed parts is almost as important especially in cases where there are certain criteria for part strength or fatigue control.
“On the orthopedic side, I think really getting the strength, getting the fatigue strength up in titaniums to match that of a forging – I mean, we’re just about there,” says Kulesha. “But to do that on a repeatable basis, you really need to have the right heat-treating equipment, and you’ve got to have someone that’s able to understand that heat treating equipment. It’s got to be reliable.”
Post processing of polymer 3D prints delivers fewer challenges than 3D printed metal parts and many tasks can be achieved manually, but the process can still benefit from mechanization and automation.
“In dental, the patient is going to feel when [the 3D print] isn’t smooth,” says Prabhu. “When you’re looking at the resin based technologies, you’re looking at more smoother structures, more accuracy in there. So the polishing operation is more a secondary process, but still necessary.”
“Obviously the nicest, crispest finishes will come if you go in and re-CNC, re-machine them, using standard tooling,” says Kulesha. “But that becomes a little bit burdensome, and certainly might defeat the whole reason for 3D printing, which is to get you to that net shape as close as possible.” Post-processing in the additive manufacturing workflow is becoming a critical part of making the technology industrial grade. Addressing the right strategies can mean the difference between profit and loss, and achieving repeatability and part quality.
Join the discussion at the AM Medical Summit, November 1-2 in Minneapolis or one of the upcoming AM webinars.