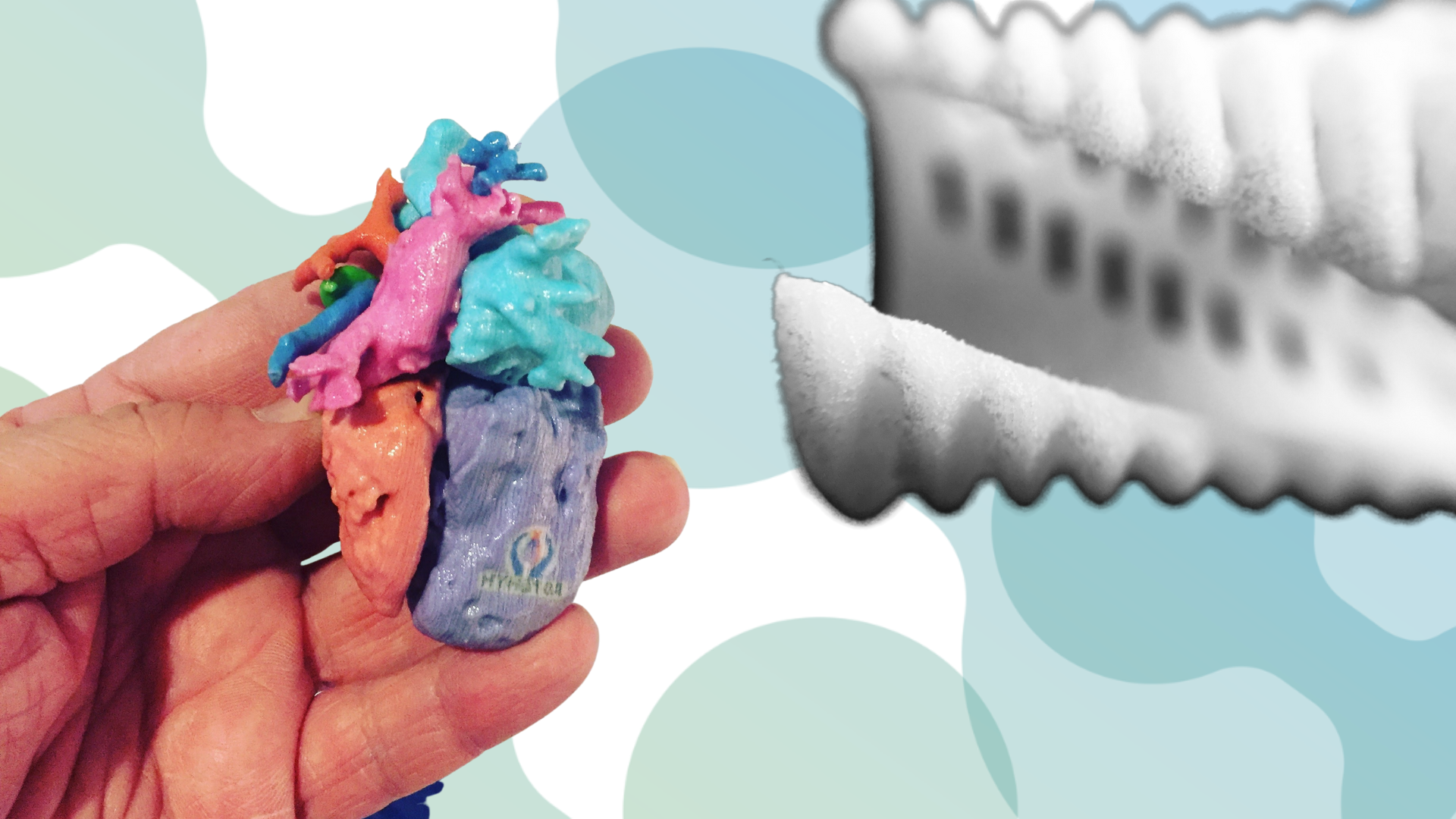
The value proposition of medical 3D printing is massive. Innovation drives innovation, though, and the ability to use advanced medical imaging to create patient-specific or patient-matched devices has always been a driver for innovation – especially as new technologies have developed. Certain devices on the market or in use with patients now would not have been able to have been manufactured previously.
No One is One-Size-Fits-All
Whether you look at the people around you or you’ve ever fallen for a clothes tag suggesting it will fit all (or, worse, “most”), understanding that no two people are built quite the same requires less-than-Sherlockian powers of observation. If one-size-fits-most souvenir shirts don’t really fit everybody, why on earth would medical device manufacturers assume that their devices might fit every body?
We’re past those days now, or we should be – because we could be.
Casts, splints, orthotics, prosthetics, implants, and more can now be body-specific, designed and built for this-size-fits-you.
This TBM (tracheobronchomalacia) splint, for example, from the University of Michigan was designed specifically for a young patient with very specific needs. The 14-year-old patient, with both severe autism and thoracic scoliosis, acquired TBM and required a very personalized solution to help her fully recover. For a condition with such high morbidity and mortality rates, the researchers’ finding a year after surgery – “The patient remains asymptomatic, has had no additional hospitalizations, and there have been no apparent complications” – was huge.
Many other such cases are out there proving out the efficacy of 3D printing to deliver results made for specific cases. Dozens of 3D printed TBM splints alone have shown demonstrable clinical success stories in patients of varying ages. For a disease that can too often prove fatal, these results speak volumes. For medical providers on a broader scale, though, such results may not be enough.
So let’s take a look at even more. Commercial clearance of splints, swabs, and implants brought about via 3D printing highlight the growing body of evidence that this technology offers realizable, safe, and quality-of-life improving if not fully life-saving capabilities.
Innovative Medical AM Applications
As medical applications continue to gain evidentiary support for additive manufacturing as a viable approach for patient-touching use, let’s take a look at seven of the newest innovations on the block.
These specific examples of innovative medical applications will be presented at the upcoming AM Medical event, where the audience will vote in a speed round to choose their favorite during the Applications sessions!
Low-Cost 3D Printed Telepathology Device
Daniel Rosen, MD, Baylor Medicine
In an increasingly remote world where virtual meetings and even doctors’ appointments rule, telepathology is taking its place. Digital pathology imagery transmitted among medical professionals enables communication – telepathology – that removes geographical, physical, and other barriers that might stand between patient and qualified professional. A new 3D printed standalone high-resolution microscope has been developed to enable low-cost telepathology connection. Allowing for both synchronous and asynchronous as well as static and dynamic usage, this microscope targets use in patient care, quality assurance, medical education, and biomedical research.
Implantable Devices with Resorbable Polymer Composites
Mahrokh Dadestan, PhD, Evonik
Not all implants need be permanent additions to the human body. Some traumas require reconstruction via scaffolding that ultimately is resorbed into the body. 3D printing bioresorbable polymer composites, which incorporate calcium phosphate salts for enhanced osteoconductivity and improved scaffold strength, accelerates the healing and recovery process with a reduced long-term foreign body reaction. Backed by studies proving that osteoblast cells respond to calcium phosphate, producing more bone matrix, these innovative devices have a broad range of applications.
Modified 3D Printed Eye Mount for Ophthalmology Wet Lab
Glenn Seela, University of Minnesota
While open source approaches to 3D printing tend to be more associated with hobbyist usage, the medical realm is no stranger to modifying open source designs. A modified open source 3D printed eye mount has in this case been adapted to fit existing wet lab materials, upgrading in a cost-effective manner the Kitaro eye kit. In this way, 3D printing is enabling an improved capacity to simulate a number of ophthalmology procedures for a real-world wet lab environment. Modifications can be adapted to each unique simulation setting, taking existing open source materials to be widely adaptable and expandable.
Three Little Birds: Custom Clinical Applications for Endangered Species
Jonathan Ford, PhD, University of South Florida/Tampa General Hospital Radiology
Medical applications extend to our furry and feathered friends as well, as veterinarians continue to turn to custom 3D printing solutions. The International World Health’s “One Health” movement encourages collaboration between human and veterinary medical practices, bringing new capabilities and innovations to more of this planet’s complete population. USF/Tampa General Hospital’s Division of 3D Clinical Applications, along with specialist veterinarians and national zoos are turning to 3D technologies for clinical solutions for animals domestic and wild. Endangered species in particular have been benefiting from their own custom 3D printing medical innovations.
3D Printing Surgical Guides for Pediatric BAHA
Elliott Hammersley, UPMC
Hearing aids are famously the leading example of mass adoption of 3D printing, with effectively the entire hearing aid industry adopting the technology in 500 days. Bone-anchored hearing aids (BAHAs) are perhaps poised to be the next major use case. Pediatric patients’ BAHA implantation is now benefiting from advanced patient-specific anatomic models, virtual-surgical planning, and 3D printed surgical guides. The intricacy and fine detail of anatomical understanding and segmentation ensures that exact location and trajectory of anchor screw placement is well understood prior to implantation.
World’s First Successful Double Hand and Face Transplant
Alyssa Glennon, Materialise
Any transplant procedure is fraught with difficulty, from sourcing donors to ensuring fit and painstaking surgery through to forestalling rejection. Each layer of complexity requires careful understanding for potentially life-changing results. Now double that. Now double it again. The world’s first successful double hand and face transplant required more than just careful planning and exact timing. Surgical planning and 3D printed patient-specific guides effectively gave this patient his life back.
3D Printed Simulation Models for Resident Education of Caudal Anesthesia
Josephine Nelson, University of Minnesota
Compared to many other medical disciplines, anesthesia is a relatively younger capability – and in more complex procedures, as in pediatrics, opportunities to train are incredibly limited. Lacking specialized training models, many medical practitioners’ first experiences in performing pediatric anesthesia involve real patients. Intubation and other anesthetic procedures with available training models tend to see superior resident education – and patient outcomes. 3D printing comes to bear here in establishing new multi-property caudal anesthesia trainers. Building in new layers of complexity, such as transparency to allow for immediate understanding of the relationship of needle to sacral anatomy, leads directly to better training opportunities. These 3D printed training models allow for simulation of palpation, needle introduction, and needle guidance, with immediate educational feedback.
AM Medical
The upcoming AM Medical event will feature these use cases and many more, as innovations continue to accumulate. Will you be joining the event live in Minneapolis November 1-3? Check out the full agenda for details on the Innovation sessions to vote on your favorite of these applications and hear directly from the experts in medical additive manufacturing.