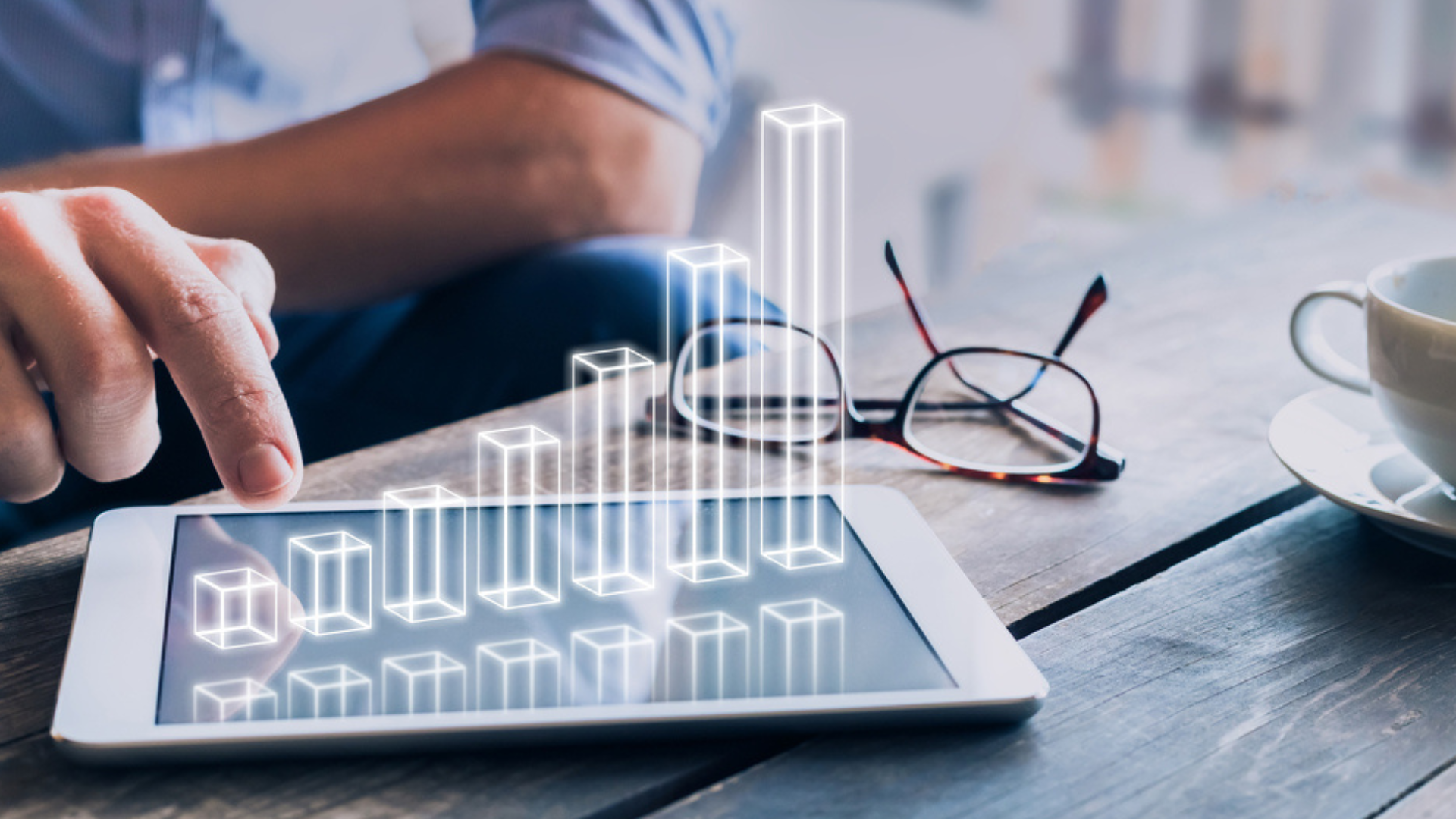
The World Economic Forum, citing data from a recent United Nations Industrial Development Organization (UNIDO) report, reveals advanced technology adoption benefits for industries. Using more innovative technology results in better production performance and revenue. Adopting new technologies is not always an easy decision for company leaders.
Various research points to three major reasons companies do not rush to adopt advanced technologies, such as 3D printing or Digital Twin methodologies. First, the availability of skilled talent, followed by the financial resources to acquire advanced technology, and added to the cost of adoptions is whether it can be integrated with existing technologies (easier) or requires a completely different system.
This recent article by Steven R. Schmid and Shreyes N. Melkote, Can Manufacturing Respond to the Great Resignation?, highlights “that a shortfall in excess of 2 million skilled workers will exist in the American manufacturing sector, and over 300,000 too few engineers.” However, the authors also point to potential directions manufacturers can go to solve training and recruiting challenges; highlighting the Manufacturing USA program. AdditiveManufacturing.com also shared news about how the national AM Forward initiative could increase technology adoption into manufacturing processes.
Here are a few significant technologies emerging in manufacturing, for which training and investment is or can be enormous:
- Robotics: Automated vehicles and sorting arms
- Software as a service (SaaS): Predictive maintenance and vision software
- Digitization or data software: Digital Twin, Data analytics (AI included here)
- Augmented/Virtual Reality (AR/VR): Wearable headsets, vision software
- Material science: High-performance polymers, ceramics and composites
- Advanced Manufacturing
Advanced Technology Adoption: Considerations and Benefits
The risks to small and mid-sized company leadership teams are ever-present – a new hire leaves for a more technically-advanced role, losing the training investment. Or, equipment is purchased without realizing the training upskilling that will be needed.
Attracting and retaining skilled talent is one of the main benefits that follows implementing advanced technologies. People want to work for companies on the leading edge, not the trailing one. Data shows why people join technology-based companies – build their resume, prestige, higher salaries due to higher revenues, to name a few.
Where can we find these early adopters?
Space and medical devices are industries with high reward (but also higher risks/costs). Both are doing things that couldn’t be done before. For example, NASA is a leader in not only developing technologies but applying nanomaterials, digitalization, and 3D printing components. Medical innovations include 3D printing of titanium hip cups with porous structures that aid in osseo integration.
Low risk areas within entertainment and sporting goods: Equipment makers are using carbon nanotubes for golf clubs; entertainment experts are creating Hollywood special effects by 3D printing for props or 3D modeling with virtual and augmented reality for films and gaming environments.
Moving to new platforms and advanced technologies will always present risks and rewards, but as the “Great Resignation” article and the UNIDO data confirm, the early adopters will reap stronger revenues. New federal and state programs will hopefully bridge some of the training and equipment acquisition costs to make these decisions easier to afford and embrace.