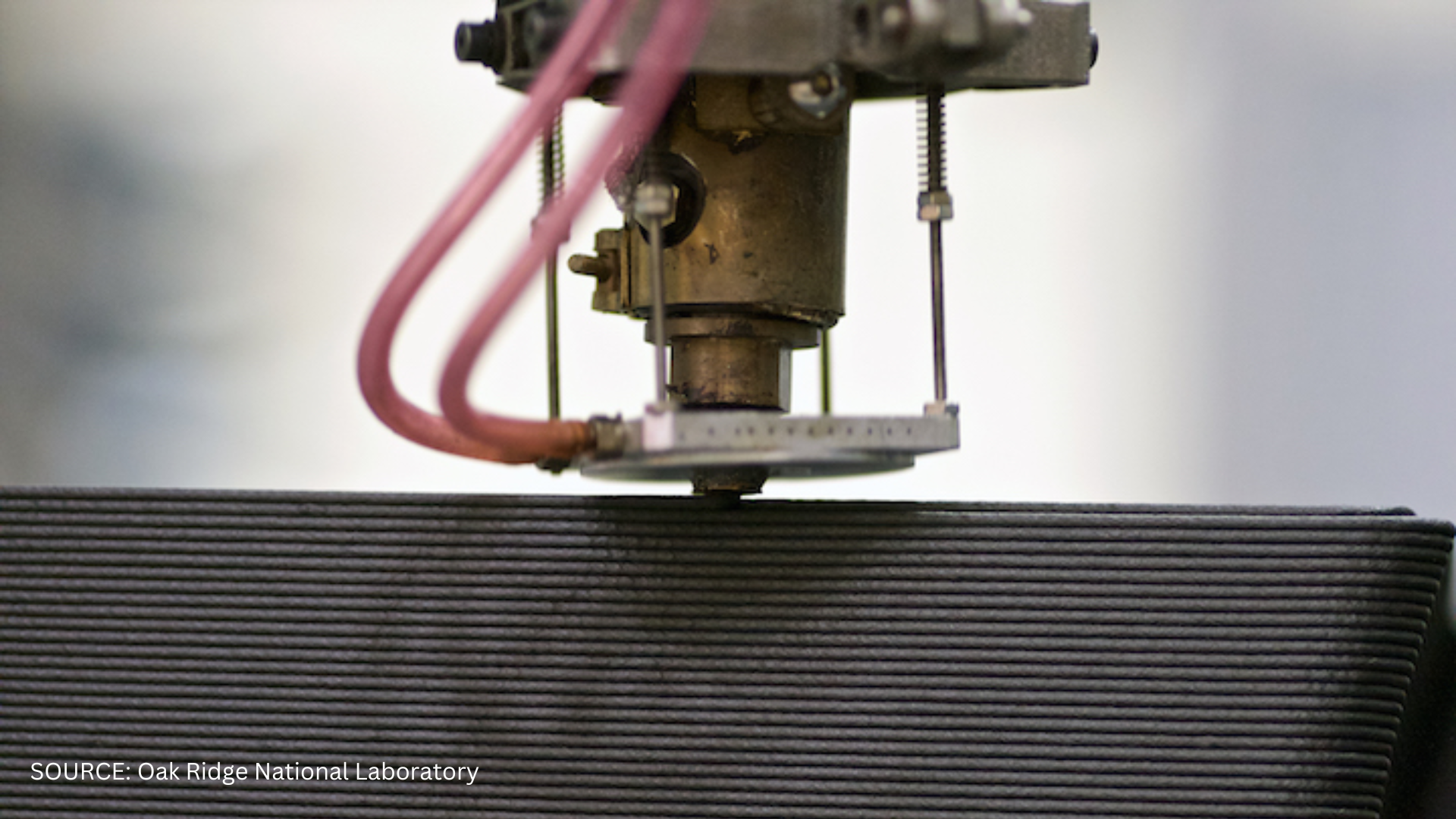
Lonnie Love is a corporate fellow and section head over precision manufacturing and machining at Oak Ridge National Laboratory. He is a leader in large-scale additive and advanced manufacturing. He spoke with Mechanical Engineering about development of large-scale AM technologies.
M.E: You have been involved in additive manufacturing and 3D printing research for some time. Automotive work garnered early attention, and now you’re branching out.
L.L.: There’s a lot of opportunities for additive to really transform a lot of different industries. I think automotive has leaned
in, and it is doing a lot in a very competitive environment, mostly focused on smaller components. I think this whole electrification of vehicles, it’s going to provide a lot of opportunities for additive to have a big play in automotive, but one area that I’m really passionate about is very large-scale 3D printing.
Additive is really good at low-volume complex Parts I think this is starting to change, where you can also do high volume but by and large, it’s really targeted towards low volume production.
When you start talking big things there’s not a lot of processes that you can use, so additive really has a sweet spot for 3D printing very large structures. We’ve done a lot of tooling work tooling for air, wind, and aerospace.
We’ve been working for the past four or five years with Lincoln Electric on large scale steel where we’re printing large steel structures. For me, a killer application is tool and die, being able to print large stamping dies, 10,000 pound dies, and in days rather than months. This can really trans form the tool and die industry.
M.E: Describe the workings of large scale printers.
L.L.: For large-scale metal, these are mostly welding systems, so rather than using a powder we’re using wire. We’re working with Lincoln Electric and my favorite machine right now is called Medusa. It’s a turntable, about two meters in diameter with three robots around the periphery. As the table turns, the robots are working together to grow this big steel part. Right now, we’re putting down about 40 pounds of steel an hour, making parts that are about two meters in diameter, two meters tall.
But we’re modifying and working with Lincoln Electric on a much faster process that will get us over 100 pounds of steel an hour. So as you start looking and making something like a big stamping die, something that weighs 10,000 pounds, you should be able to do it in a few days.
Lincoln Electric is building a factory up in Cleveland, Ohio, with around 20 or 30 of these machines.
M.E: What is the most exciting area of your research?
L.L.: There’s a couple of new technologies coming out that I’m really excited about. I really love hybrid machines and hybrid processes, especially as you start talking about printing these big structures.
How do you machine them and how do you get to net shape? So some of these hybrid processes are really exciting.
I see a lot of parallels with the robotics industry. Much like the 50s, 60s, and 70s, the robotics industry was really focused on just research and trying to mature the technology, and in the 80s, it pivoted and became a real manufacturing process.
I think we’re going to see the same thing in the 2020s, where the automotive industry is really going to drive additive and push it to the point where they can do mass production, and they will be extremely reliable. We’ll go from having hundreds to thousands of metal powder bed systems to hundreds of thousands of metal printers much like how today we have hundreds of thousands of industrial robots in the marketplace.
This interview has been adapted from a podcast and edited for length and clarity. To listen to the podcast visit: https://www.asme.org/topics-resources/content/podcast-ornls-lonnie-love-and-large-scale-3d-printing.