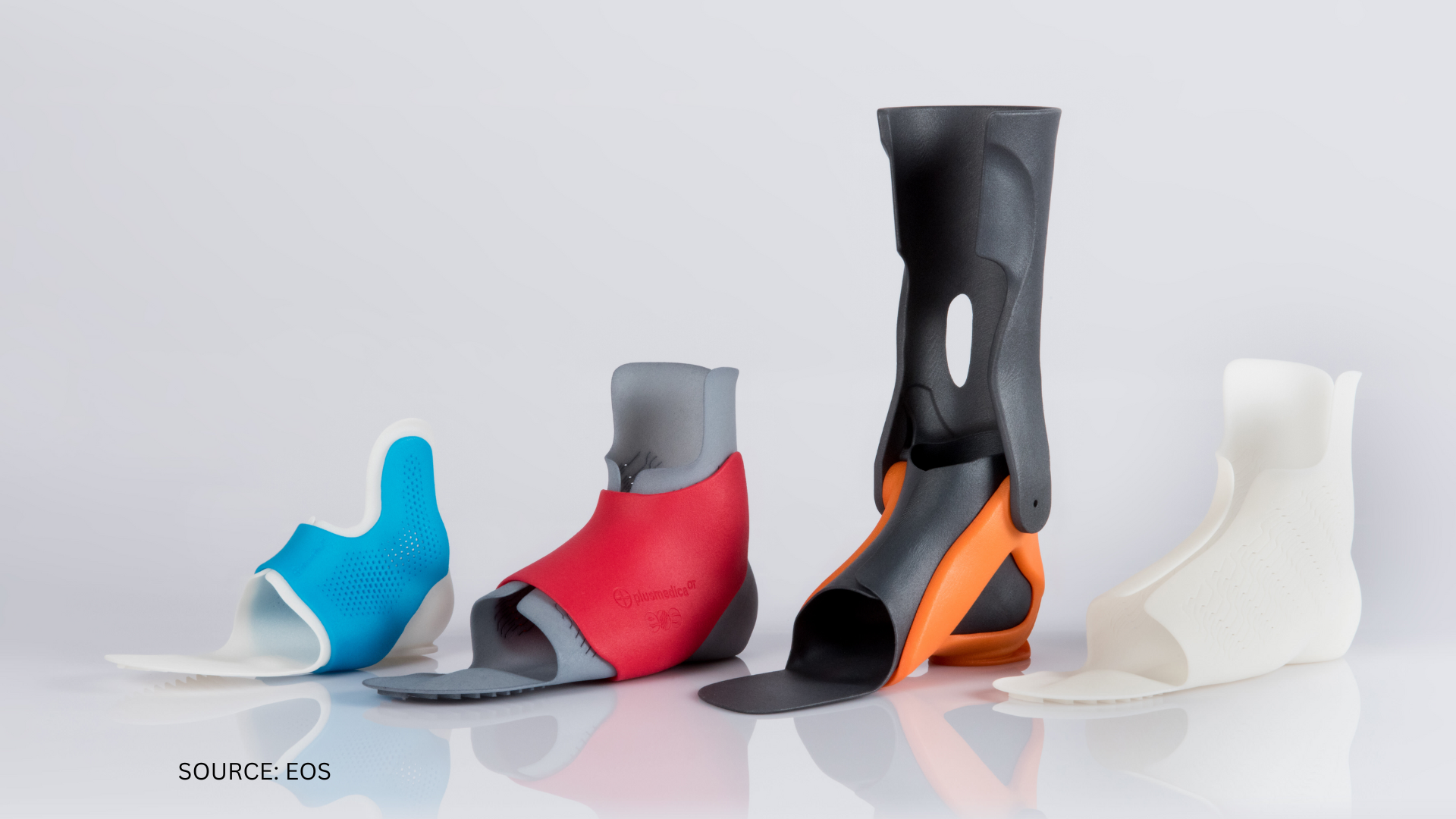
The healthcare industry has been a leader in the application of additive manufacturing (AM) since 1988. 3D-printed tools and implants are now more commonplace and help hospitals treat patients with typical and complex, unique, personalized, and custom-made devices. Greg Hayes, senior vice president of applied technology at EOS, discusses the changes within the AM industry and the impact it has had on healthcare.
Adam Penna: How has additive manufacturing changed during the last two years?
Greg Hayes: Across all industries, additive manufacturing has two main areas of change that are now coming to fruition. The first is that AM production is becoming commonplace. Organizations are moving from prototyping to production quickly. Many changes come along with this implementation of additive manufacturing: quality control systems, reliability (on the systems and companies themselves), and employee training. The second is that industry-wide understanding of qualification and certification of machines and materials is becoming more widely accepted. Groups like ASTM and MMPDS are putting together well-understood data packages, bringing a better understanding of reliability and statistical control.
A.P: What new materials are being used today for medical implants?
G.H: Mainly speaking, medical implant materials remain consistent. Biocompatible polymers, while in existence for some time, are becoming more commonplace, and titanium alloys still encompass most metal implants. More niche materials like nitinol and more additive-friendly alloys are being worked on and will see some traction in the following years. The main improvements are seen in new variations of existing materials. For example, lower price points and sustainably sourced titanium (Hyperion metals) can open the door to new applications. And ALM is bringing carbon-neutral materials to the market, which can play a role in the healthcare industry tier supply chain. So, there are no magic new materials, just improvements—cheaper and more sustainable sourcing.
A.P: Are we increasing the scale of medical 3D prints?
G.H: There are two main markets seeing growth: aerospace and healthcare. But we must distinguish between medical components and the healthcare industry supply chain. So, there are not only implantable devices using AM but also components of a hospital bed or other handles/fixtures used in the hospital room in equipment. These products are not necessarily related directly to patients but are used within the healthcare setting.
A.P.: Can you improve the speed parts are produced to provide patients with a faster turnaround time?
G.H.: The short answer is yes. There are standard-sized implantable medical components that can be premanufactured to determine the timeline in which they will be available. With patient-specific components, there are ways to improve manufacturing speed. For example, our new EOS systems equipped with multiple lasers and scanning systems that no longer use just a single spot, but rather a beam-shaped exposure can vastly increase throughput. In situ monitoring and increased automation will also add to the reliability and repeatability of these systems. There are also advances in supply chain logistics using local manufacturing to eliminate delays and secure critical manufacturing demand.
A.P: How has additive manufacturing been used for point-of-care treatments?
G.H: Many companies have been working on patient-specific implants, cutting guides, and “made to measure” orthotics. However, manufacturing is not instantaneous, even with 3D printing. As imaging techniques continue to improve and costs decline, personalized medical devices can be more readily available. While having an industrial additive manufacturing system in each operating theater is not very realistic, in my opinion, the benefits of localized manufacturing can be realized today by hospital systems.
Find out more about the use of additive manufacturing in healthcare by visiting the Medical Channel.