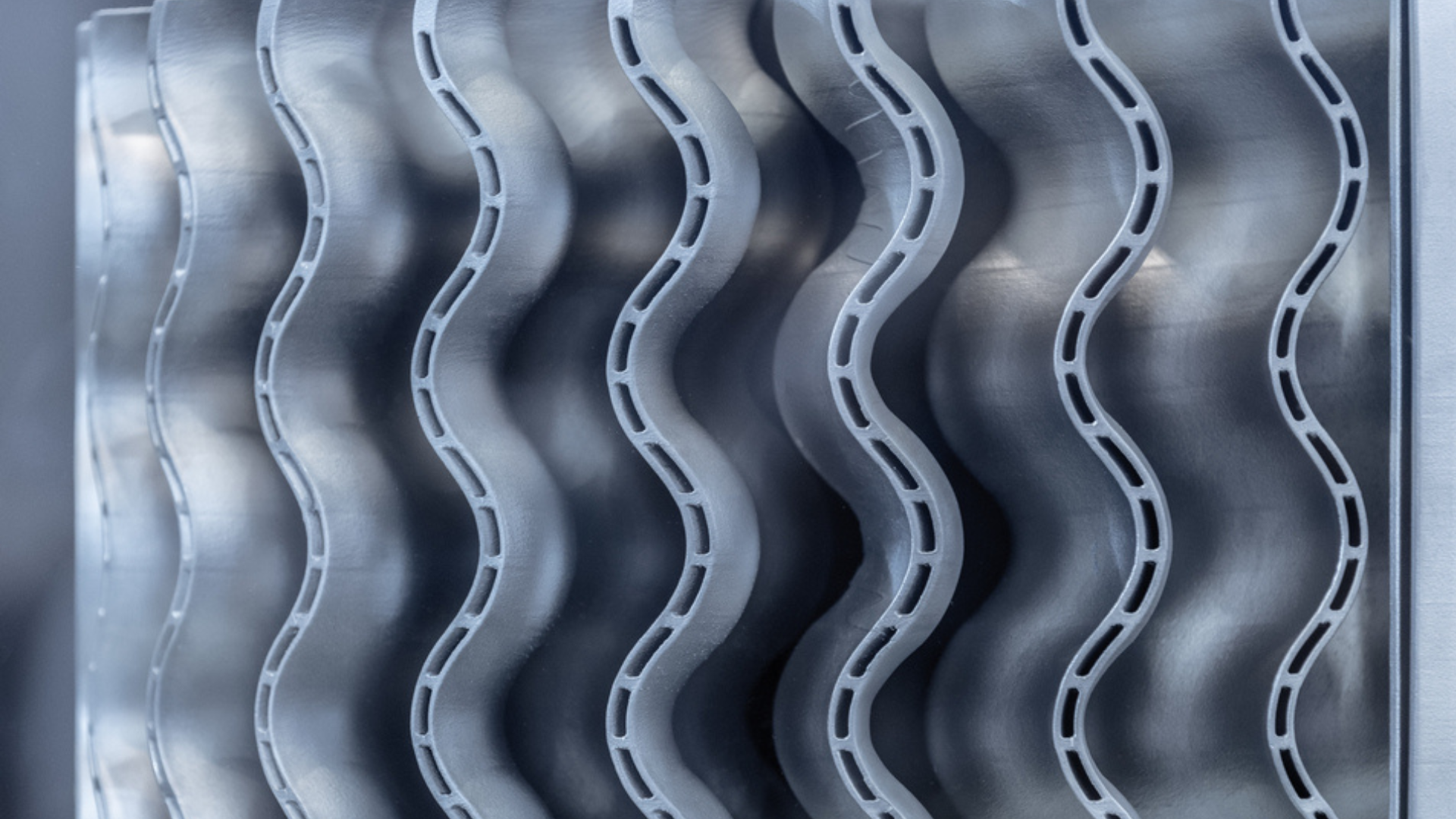
In recent years additive manufacturing (AM) technologies and materials have evolved into being able to achieve industrial-grade parts production, which means AM parts are now entering the supply chain. As a result, manufacturing OEMs are figuring out how to implement that, which is bringing new thoughts, ideas, methodologies and also, disruptions to traditional supply chain methodologies.
In a recent discussion, AM supply chain specialists from Northrop Grumman, Equinor and Shell discussed how they are integrating and even reinventing supply chains to adopt AM into their processes. While they are not stepping away from traditional supply chains, they know that AM, if set up properly, can be a game changer simply by rethinking the possibilities that can move them away from the linear supply chain. The implementation of digital inventories and AM-focused suppliers is key to the new approach.
Brede Laerum, head of the AM Center of Excellence at Equinor, commented. “The new way of working that we are looking into is using a digital inventory software platform where everyone is connected, the OEMs and the sub suppliers, and it meets a higher transparency, also higher speed,” he said. “So when everyone is connected, then of course you can deal with companies from anywhere in the world. You can download or rather order a digital part from anywhere in the world. And using additive manufacturing, of course with high quality processes, then you can really recreate the physical component anywhere.”
Laerum continues: “It’s as simple as changing from a process where you design something, then you produce it, and then you hope that someone is going to buy it, to designing something, then you sell it and you produce it afterwards. And that’s exactly what we are talking about here by using those digital tools that are available for us.”
Inventory for these OEMs is also a concern. Laerum revealed that Equinor has more than $3 billion in inventory, yet still needs to source more parts and that AM should be a solution to this.
Angeline Goh, additive manufacturing technology lead for Shell agrees. “We are looking at additive as a way to overcome some of the challenges we have in Shell with regards to a growing inventory where working capital is tied up,” she said. “We also face a lot of challenges from the fact that many of our assets are mature, and as a result we [deal with] equipment that is no longer available in the market and no longer in the scope of the OEM. And the spare parts for it are difficult to get.”
AM is well understood for its value in on-demand production of parts and Laerum also sees that a shift to an advanced ‘just-in-time’ model would be a desired outcome for his operation.
“We would like to go more into on-demand manufacturing instead of producing them in case we need them,” he says. “We would like to produce them just in time, when the need arises. And additive manufacturing is perfectly suited for that philosophy. So digital parts can be bought and sold and the production of the part is locally as close to the end user as possible.”
All the OEMs speaking are also keen to utilize AM not just for creating identical parts to those created using traditional manufacturing but as a way to improve part performance, reduce material usage and so on.
Peter Le, additive manufacturing engineering manager at Northrop Grumman, commented, “First we have to identify the suppliers, then the most appropriate technology or additive process to apply to this. And in that inherently will be an iterative cycle where you’re interacting with either the supply base and that designer to do design for additive,” he says. “So not just doing one-for-one trades, but really unlocking the benefits of additive through that design for additive approach. Eliminating overhangs, trying to better understand is there a surface finish requirement and so on.”
Implementing AM into the supply chain requires adjustments in standards, an understanding of exactly which AM technology should be used for what parts, ensuring quality of the parts, and consistency by the supplier. While this is important for any OEM, production of critical aircraft parts is a lengthy and complex process.
Peter Le: “In our industry [there are] a lot of traceability requirements, the quality management system, powder handling, all that good stuff,” he says. “But essentially, we would go out and conduct a supplier audit and identify any gaps, work with the supplier to fill any of those gaps, and then eventually get them added to that special processor’s list. But as a part of that audit, there’s also qualification builds that we like to ensure that we execute with the supplier as well.“
Fortunately a new set of standards are being implemented to enable AM supplier qualification.
“We already have some international standards that we are using in the oil and gas energy industry, like the API 20S for metal parts,” added Brede Laerum. “We will also have a new standard called API 20T for polymer parts, and we use the DNV standard called B203 and those standards tells us how to qualify a 3D printing factory with our processes and competence and machines. But it also tells us how to qualify the physical components that are being produced from that factory so that we are absolutely sure that the quality is right and that the functionality is what we are expecting in the other end.”
It is evident that a lot of movement is happening in implementing AM into the supply chain but it is still in early stages for developing the right models and procedures.
Says Angeline Goh, “I think additive poses a wealth of potential opportunities to diversify and to create alternatives that will solve problems that we face today with our current supply chain,” she says. “But we still have to come together to solve challenges such as improving the ‘right first time’ issues so that the short delivery lead time that we promise our end customer is indeed achievable. I think as an industry we will be able to accelerate the process of using, but also scaling up additive manufacturing if we come together, share knowledge and also work together for more standardization in the quality control process that we need, specific to our industry.”