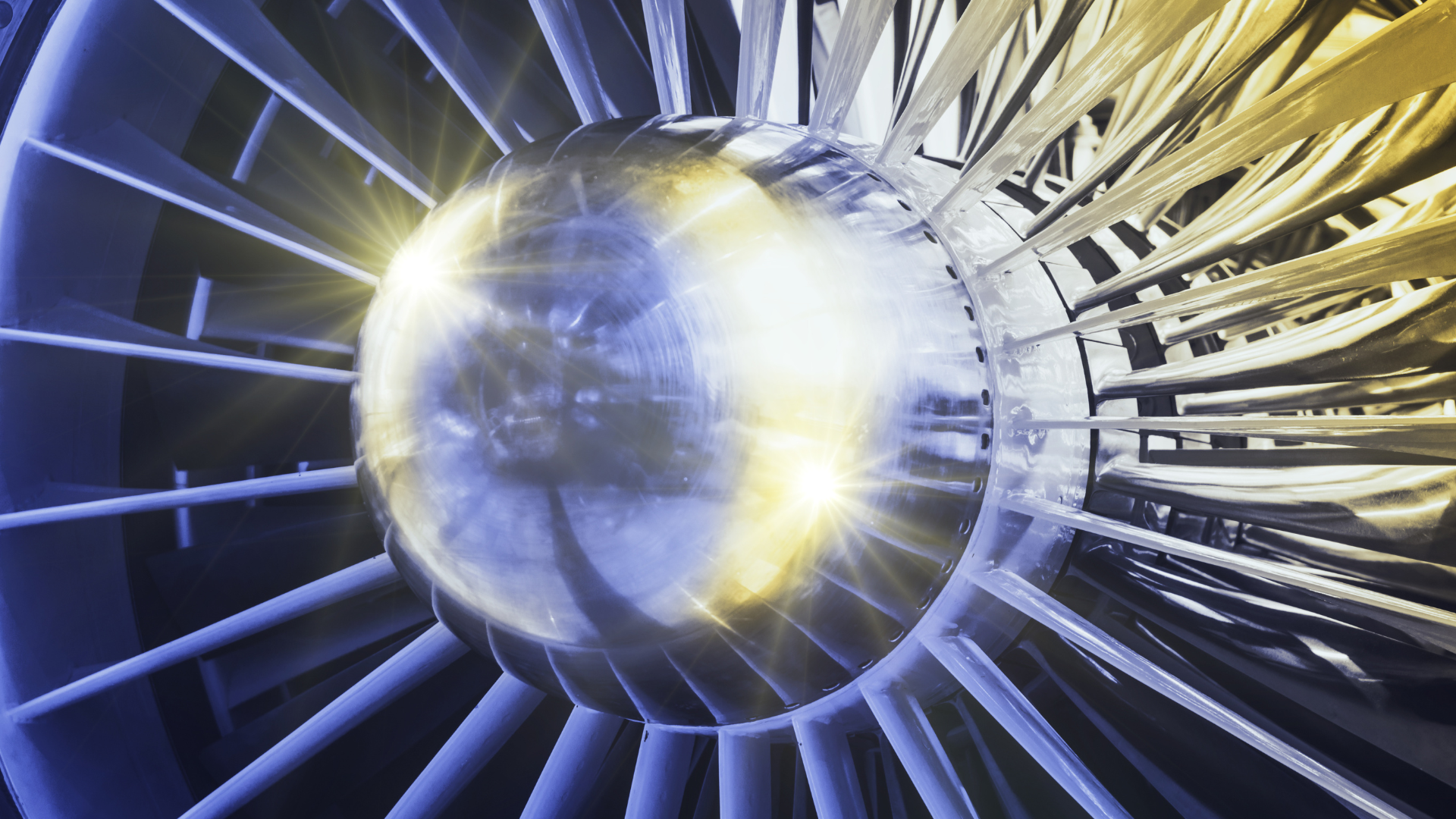
3D printers have demonstrated capability of so much. There are many wow inducing, human race compelling, case studies in healthcare, construction, space, automotive, and aerospace.
We are not talking about fidgets, prototypes, or paperweight models. We are talking about flight critical (safety-critical) parts. Honeywell, Boeing, and Lockheed Martin are all using 3D printing for critical parts. Honeywell and Boeing are finding vast time and cost savings in printing parts for aging fleets. Lockheed Martin is using 3d printing in many ways; this article highlights a large high pressure fuel dome and avionic circuit housing box mounted to an orbit ready satellite.
Where 3D printing really thrives in this industry is for short volume, high accuracy parts, but that’s not to say there hasn’t been successful applications of serialized parts like GE’s fuel nozzle that went into manufacturing in 2015 and is still being manufactured in thousands-per-year quantities. All of these devices are foundationally built within the organizations’ quality management system (QMS) that is compliant to and certified to meet the AS9100D Standard. This compliance is typically certified by an outside registrar and often times if not always, companies post their performance on the Online Aerospace Supplier Information System (OASIS) database where it’s transparent for companies to pick suppliers with good quality performance data.
All 3D printing systems used in the aerospace field need to be based on a strong quality management system. AS9100D is the standard that outlines the requirements of quality system for manufacturing of aviation, space, and defense organizations. This standard is based on ISO 9001, with specific requirements for aerospace. It matches up more accurately with the medical device standard, ISO 13485 which also was based on ISO 9001 but diverged in 2015/16. Regardless of the basis, and despite all the technical disagreements of interpretation and nuance, all these quality systems standards rely on the same foundational sections encompassing:
- Leadership
- Planning
- Support
- Operation
- Performance Evaluation
- Improvement
Typically, the largest subsystem to demonstrate compliance, and holds true with AS9100D, is Operation which includes 7 minor, in name only, systems which cover:
- Operational planning and risk management including counterfeit part prevention
- Requirements for products and services
- Design and Development of products and Services
- Control of Externally Provided Processes, Services, and Products
- Production and Service Provision
- Release of Product and Services
- Control of Non-conforming Outputs
Undertaking implementation and operation within an AS9100 compliant quality system is not a small project, but its methods and requirements are well documented. Where things are still evolving is in certification method. For those short run parts is Qualification and Certification (Q&C) worth it? Can quality only be ensured within the point design quality methods? Is there an opportunity for part family Q&C Specification development? Yes, companies have found ways to qualify and certify short run parts, but the time and cost for that pathway definitely erodes at profit margin. Some companies have found ways to group qualification and certification into part families to minimize the testing, specifically the statistical part counts needed for Q&C. Now standards organizations, specifically ASTM are working to make those methods more consistent and transparent through the work of Committee F42 which has an open work item addressing this very issue.