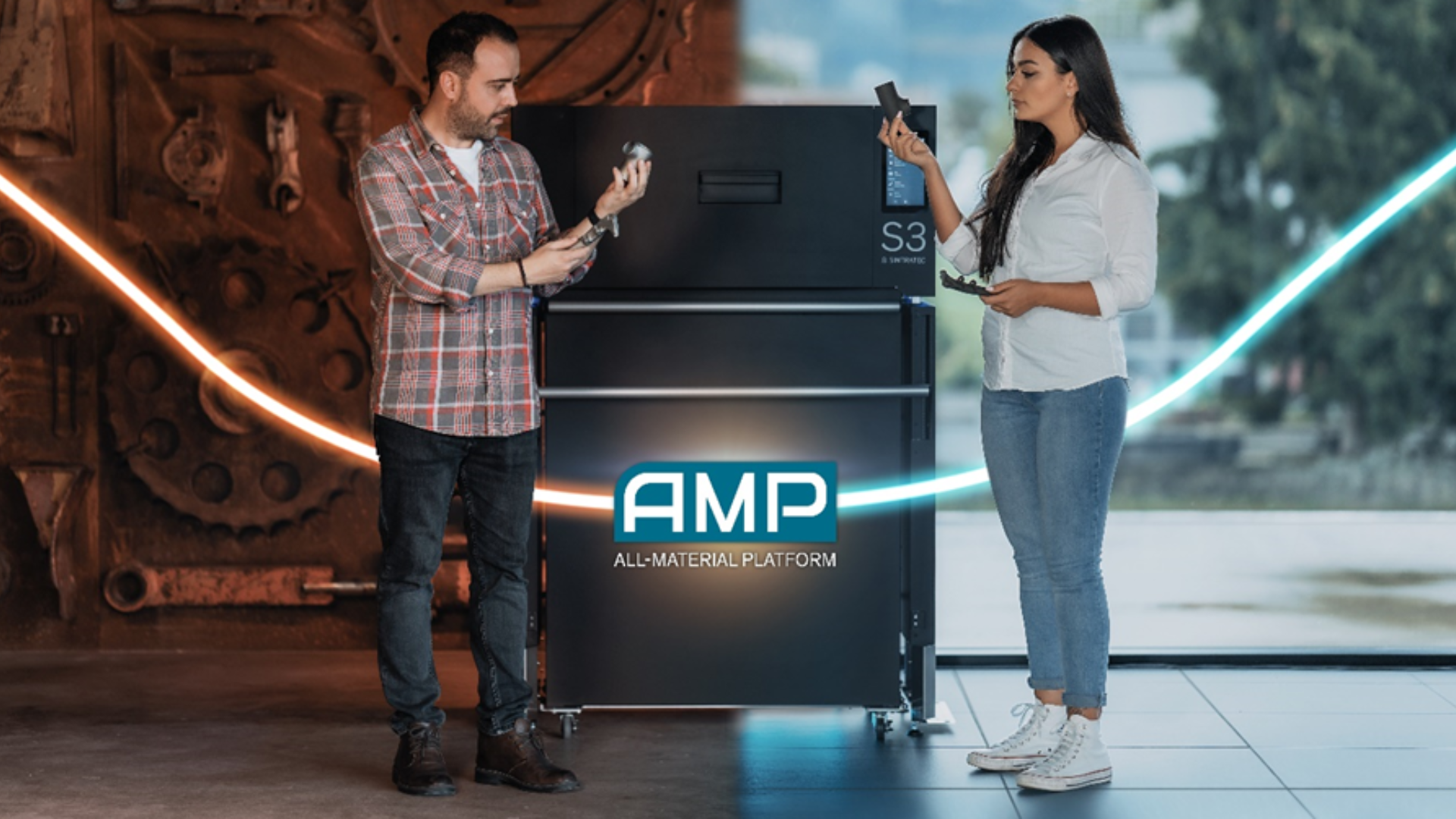
Brugg, Switzerland/ November 14, 2022 — As a major milestone in the company’s history, Sintratec unveils its one-stop additive manufacturing solution: the All-Material Platform (AMP). In a world first, the AMP scales from prototyping to production and enables processing of all its materials on the same production line.
With the start of Formnext, the 3D printing industry’s largest trade show, Sintratec ushers in a new era for Selective Laser Sintering (SLS). Sintratec shifts away from selling single, insular 3D printers, to offering a modular and scalable manufacturing platform. Sintratec calls this unique and patented solution the All-Material Platform (AMP).
In the All-Material Platform, the 3D printers are divided into two parts. The so-called Build Modules carry everything that comes into contact with the printing material, such as the powder tanks and the recoater. The second part, the Fusion Modules, are not contaminated with powder and contain the more expensive components, such as the laser and the optics. Thanks to this modularity both various polymers and metals can be processed economically on the same production line. Excitingly, the AMP’s novel modular approach also means that all its modules are cross-compatible and interchangeable with one another.
With the introduction of Sintratec’s second generation of modules – the Sintratec S3 and the MCU-220 – the benefits of the platform approach are further highlighted. The S3 packs a powerful 30-watt fiber laser which significantly increases the printing speed compared to the S2. Joining the existing Build Module (MCU-160) the new MCU-220 features a 90% larger build volume, making it the ideal choice for bigger objects and a higher throughput. Additionally, the AMP material portfolio is expanded with the Sintratec PA12 GF – a glass-filled polyamide 12 variant for parts with an exceptionally high stiffness and impact strength.
The AMP sets itself apart from conventional industrial 3D printing, where scaling from initial prototyping to production remains difficult and cost-prohibitive, with the resulting production lines often being restricted to one material. By selecting modules customers can tailor their AMP setup to their individual application and benefit from optimal cost structure. The modules’ backward and forward compatibility also ensures that customers do not need to replace their existing hardware when scaling up, effectively future-proofing their setups.