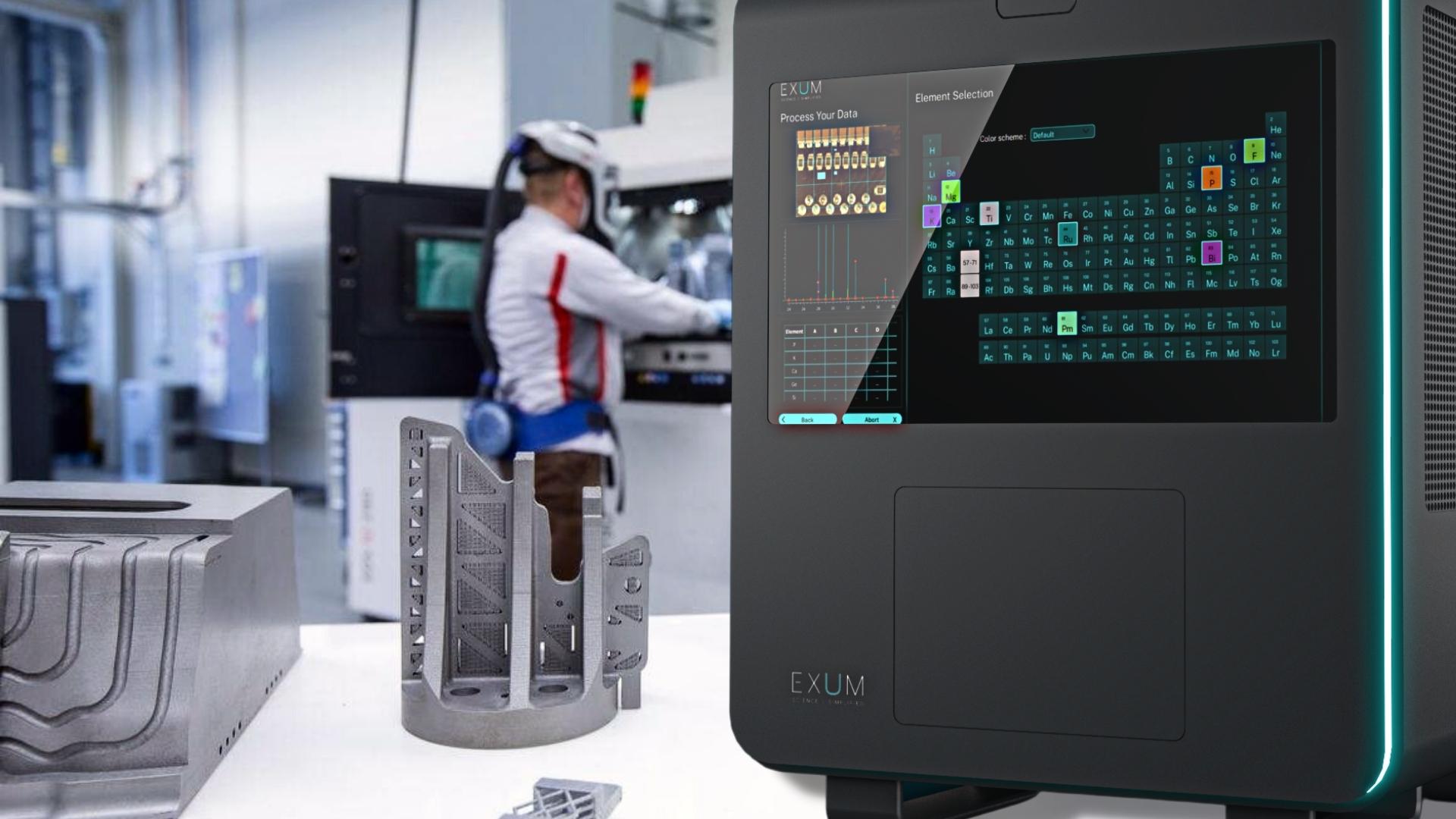
CHALLENGE: Understanding the chemical composition of any manufactured material is critical to predicting a part’s performance. This is especially important for additive manufacturing because rapidly melting and solidifying materials can affect chemical properties and impact part functionality. Despite its importance, performing chemical characterization is difficult and time-consuming, requiring multiple analytical instruments, complicated operational and calibration procedures, and trained chemists.
SOLUTION: A new mass spectrometry technique can quantify the metallic, trace, and low-mass constituents in a single analytical session with minimal sample preparation time. As a result, it has potential to accelerate the quality control process for additive manufacturing powders and builds. This is especially impactful to prolonging the life of recycled powders. Often, additive manufacturing users have a “rule of thumb” for how many build cycles they can use powder before discarding it. If a user can quickly verify the chemical composition meets specifications, they can avoid disposing of powder after a predefined number of build cycles, saving the approximately $100,000 required to refill the printer’s powder prematurely. For instance, an interview with a Systems Engineer in a Department of Defense branch revealed their facility spends $80,000 and $180,000 to refill the titanium and cobalt chrome powder printers, respectively.
To test the new technology’s quantification capabilities, a material producer provided two titanium powders: one blind sample (Sample #1) and one known sample (Sample #2). The elemental composition was shared for Sample #2, which was used as a reference material to quantify the unknown sample’s constituents. For all quantified elements, results matched the powder’s certified values and those generated by an accredited testing laboratory using other methods. Once the pelletized powder samples were loaded into the instrument, results were acquired within minutes.
TECHNOLOGY: Laser Ablation Laser Ionization Time of Flight Mass Spectrometry (LALI-TOF-MS) addresses many challenges associated with other analytical techniques to offer rapid, high-sensitivity quantification of nearly the entire periodic table. The ionization source, LALI, uses two lasers to first ablate, or release, material from a solid sample’s surface and then ionize neutrals present in the ablated material. The laser ablation process allows direct analysis of solid materials, like additive manufacturing powders or parts, without the complicated sample preparation procedures of other techniques that require liquid sample introduction. The ionization laser targets the neutral particles created by ablation, which are more representative of the sample’s constituents than plasma-generated ions. Overall, LALI results in more reliable elemental verification and reduces sample matrix effects.
After ionization, the TOF mass analyzer creates a full mass spectrum at each laser spot, as shown below. Figure 1 displays an example titanium powder sample’s mass spectrum. Based on the naturally occurring isotope patterns, the software verifies each detected element. The top pane highlights trace low-mass elements that are difficult for many techniques to quantify: hydrogen, carbon, and oxygen. The bottom pane shows the naturally occurring isotope pattern for titanium oxide. The text box compares the theoretical (known) isotope ratios with those quantified from the mass spectrum’s peak areas, which are within 1%. This demonstrates the isotopic accuracy of LALI-TOF-MS.
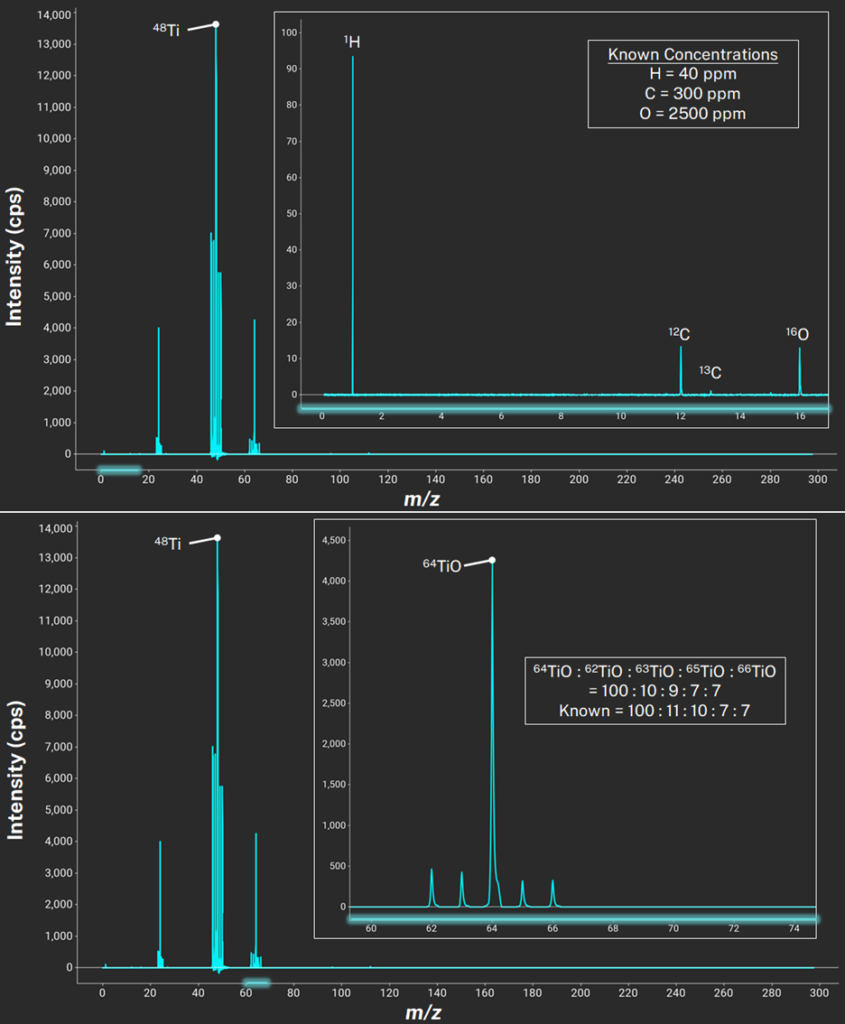
TESTING QUANTIFICATION CAPABILITIES: This study involved analyzing a pair of titanium powder samples. One was a known reference standard, used to quantify the unknown sample’s constituents using a linear single-point calibration. Because LALI-TOF-MS requires a solid sample, powders are pressed into 1.3-cm (0.5-in) solid pellets using a pellet die set and hydraulic press.
Each sample was analyzed using three 0.2 mm2 areas. The areas are each rastered twice, removing any surface contaminants in the first pass and using the second pass for quantification. The system’s sample tray can accommodate up to 16 pressed pellets, and the user can set up the instrument to analyze all samples within the same session. While the user is defining testing conditions, the instrument brings the closed sample chamber to vacuum. Once vacuum is achieved, the analysis requires only three minutes per sample.
For Sample #2, the known sample, a laboratory chemical test report was provided. To quantify the composition of nine elements, the lab used four standard test methods and three different analytical instruments. This known information was then used by to quantify Sample #1’s elemental concentrations with LALI-TOF-MS. Figure 2 compares results quantified by LALI-TOF-MS with certified values and those provided by an analytical testing laboratory. In this graph, values certified by the powder provider are black, results acquired by the laboratory are gray, and those quantified by LALI-TOF-MS are blue. Titanium’s concentration is presented in weight percent (wt %) and those of minor and trace elements are in parts-per-million (ppm). In this case, the accredited lab quantified four trace elements only. Testing laboratories typically charge per element and the excluded low-mass elements can cost ~$100 each. The graph includes certified values for the elements that were not measured by the lab. For results quantified by LALI-TOF-MS, error bars show the internal precision. These values are 1σ standard deviation of the three different raster areas.
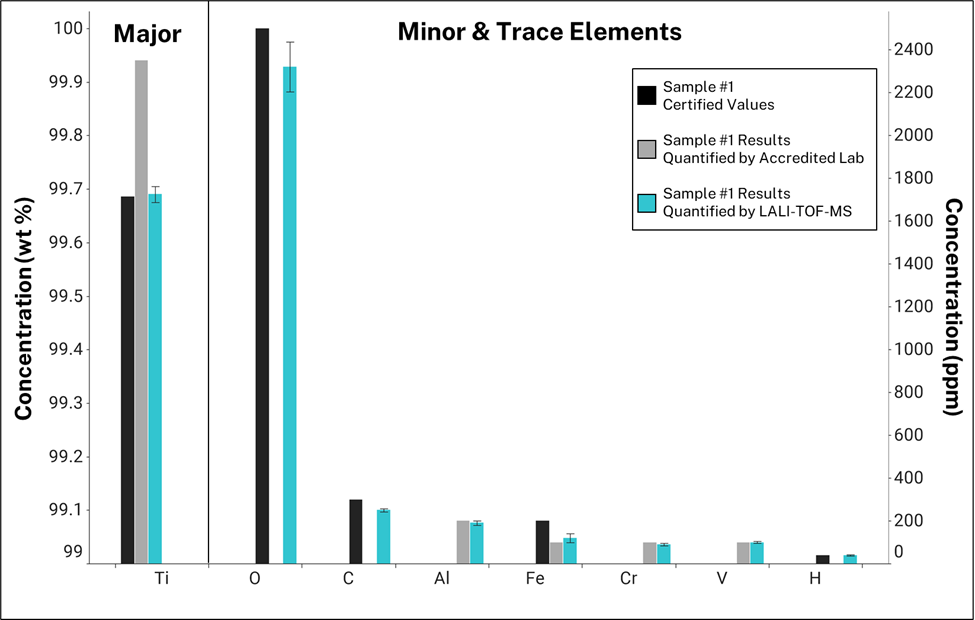
Figure 2: Results from quantifying the unknown titanium powder (Sample #1) through single-point calibration using the known titanium powder (Sample #2) as a reference. Bars compare results quantified by LALI-TOF-MS with certified values and those acquired by an accredited lab. Note certified values are included for elements that were not measured by the accredited lab. Error bars are 1σ standard deviation across triplicate raster areas.
SUMMARY: This study highlights LALI-TOF-MS as a promising new and alternative technique for chemical characterization of additive manufacturing powders. Using Sample #2 as a reference, the elemental constituents of Sample #1 were quantified within 8% of known values, on average. All quantified elements were within 20% of the certified or lab-quantified values. Internal precision was 6% relative standard deviation (RSD), calculated from the triplicate raster areas’ variance. This low variance demonstrates the repeatability of the technique.
Because this innovative technology can quantify the metallic, trace, and light elemental constituents in the same analytical session, it has potential to significantly reduce quality control time for additive manufacturing powders. Instead of using four different standard test methods and three different analytical instruments, the LALI-TOF-MS results presented in Figure 2 were acquired within minutes. Its simplified operations and desktop package bring high-sensitivity chemical characterization out of the traditional laboratory environment. For additive manufacturing users, this solution can support a procedure for reusing powder based on rapidly acquired data instead of a predetermined number of build cycles.