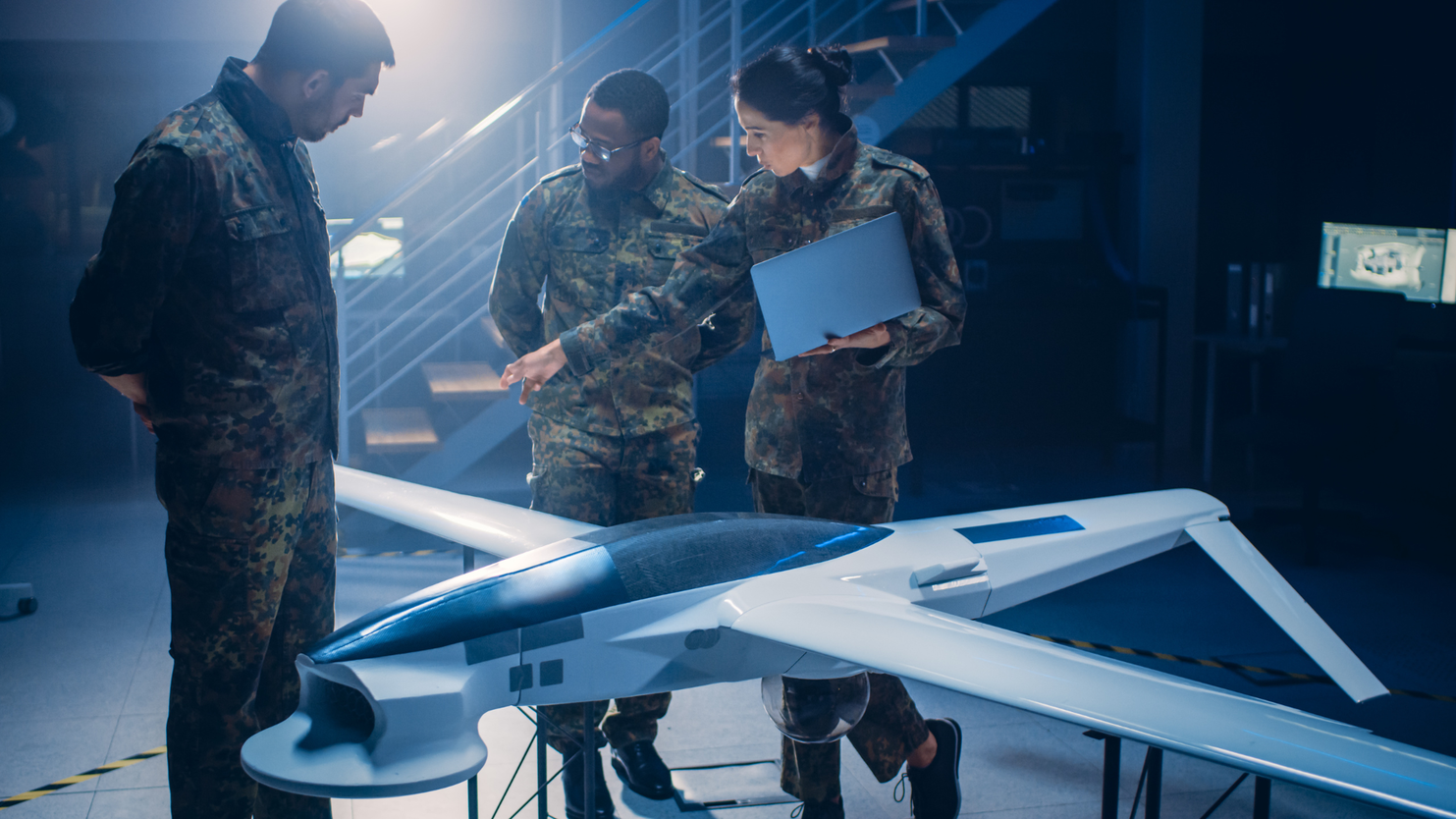
Within additive manufacturing, there is a big focus on part and application qualification. With new technologies, materials, and post processing capabilities making their entrance into the industry, it’s important to validate end-use functionality. This takes time and requires a collaborative effort amongst OEMs, users, and research institutes. For critical and commercial applications, these developments will likely lead to thorough testing, which will hopefully result in a comprehensive data set that justifies certain technologies for specific uses. However, there is one unique, industrial sub-segment that operates a little differently and is a big opportunity for 3DP OEMs to explore: the United States Marine Corps.
Defined as the maritime land force military branch, the Marine Corps is responsible for expeditionary and amphibious operations. As the tip of the spear, Marines are typically the first conventional combat team on location and are tasked with establishing a foothold for the United States Army, Navy and other military service branches. This indicates that the Marines are a temporary and specialized force that operate on different timelines and mission objectives. Therefore, operational uptime and immediacy are paramount to mission success. What does that mean for the qualification of 3D printed parts?
In March of 2020, the Department of the Navy published Marine Corps Order 4700.4 related to the Additive Manufacturing Policy. To understand the qualification standards of the Marine Corps is to understand the bins system.
Marine Corps Order 4700.4: The Commander’s intent of Marine Corps Order 4700.4 is to leverage additive manufacturing to reduce maintenance cycle times, curb supply chain backlogs, and place manufacturing capabilities at or near the point of need. By conducting a comprehensive review of existing ground platforms and weapon systems to certify AM-worthy parts, this directive aims to improve performance, readiness, material availability, or cost avoidance. The MARCORSYSCOM (Marine Corps Systems Command) will coordinate risk assessments, develop mini-factories, establish cooperative agreements with AM industry, and monitor equipment readiness to identify parts that have the most impact on short-and-long-term readiness.
Enter the color-coded bins system. The bins are used to determine the application or readiness for specific parts, materials, technologies, etc. This includes relevant technical data, drawings, material types, post-processing, and final inspection. Below are brief descriptions of each bin and examples of their usage within the Marine Corps’ present-day system.
Green: As we have been commonly taught, “green means go,” and that is no different for the green bin. Parts that fall into the green bin category require no additional approval for production and use. This includes repair parts that are deemed to be a reasonable substitute or low-risk factor parts, such as hand tools or training aids. All parts require an appropriate six-digit source, maintenance and recoverability (SMR) code and exist in a digital repository for information sharing and tracking. Finally, all green parts can be printed by the Marine Corps network of producers and whose form, fit and function characteristics require no analysis of performance impacts prior to use. Examples include:
- Carrying handles, blocks, braces, hand tools, jigs, fixtures, and training aids.
- Facility items such as doorknobs, hinges, and HVAC replacements.
- Innovative solutions to tactical problems that pose no risk to personnel or equipment.
Howie Marotto, Colonel, USMCR, and AM Business Development Manager at EWI, contributed to Marine Corps Order 4700.4 reflected on the adoption of 3D printing, “There are over 400 3D printers in the field with Marines, more than any other service or global military combined.” Most of these printers capable of printing green bin parts are polymer. However, Marotto explains the success story of the first metal 3D printed part approved for use on a military weapon system, an impeller that was reverse engineered, tested, and implemented on a combat vehicle. After successful testing by the Marines, the part was then further evaluated at Johns Hopkins University, where it was concluded that the AM part was actually better than the traditionally manufactured part. Learn more about the first metal 3D printed part aboard a USMC combat vehicle.
Yellow: Similar to the rules of the road, the yellow bin is reserved for parts that need to exercise “caution and further evaluation or data collection before they can be approved. This typically represents repair parts that may pose a moderate risk to personnel or equipment and require some sort of risk assessment. The yellow bin also includes prototype parts undergoing refinement. Regarding risk assessment, the Marine Corps operates similarly to the other Department of Defense (DoD) branches but is slightly more aggressive. Forward-deployed commanding officers can wave onsite qualification if they feel the benefits outweigh risk, i.e. mission success with no or acceptable risk. Below are examples of yellow bin parts and requirements.
- Repair parts with moderate risk to personnel or equipment.
- Prototypes and other innovative designs.
- All yellow bin parts require risk assessment.
Former General Glenn Walters, the 34th Assistant Commandant of the Marine Corps, was instrumental to the increased adoption of 3D printing. The previous protocol in the military was to develop research facilities to investigate 3DP, whereas Walters helped authorize the immediate purchase and acquisition of the technology throughout a mixture of battalions. In 2016, Walters stated, “We have to have the speed of trust in our young people to seize and hold the technological high ground.”. Since then, the adoption of 3D printing has ballooned at foreign and domestic bases. Learn more about how the 1st Marine Division is unleashing the potential of 3DP in the Marine Corps.
Blue: The blue bin is arguably where much of the 3DP industry currently exists and includes parts in the beginning stages of approval. Once feedback is provided in the yellow bin stage and approved by the commander of the equipment, repair parts and innovative solutions can be implemented for further evaluation. Typically, blue bin parts have a complete digital thread attached and exist in the digital repository, a necessary component for the future of military self-resilience. Pending the risk assessment, parts will route through the appropriate Program Office and may be evaluated in a laboratory or controlled field environment. A detailed characterization of the part use and function is necessary and will then be placed into the green or red bins. Below are examples of blue bin parts and requirements.
- Stop-gap solutions and replacement parts such as gaskets, radio components or impellers.
- UAV components, specialized wrenches, and other tools.
- All parts require a 3D data package.
Gary Bredael, Director of AM at the Hartech Group, has expressed the value of a data package for 3D printed parts. “The DoD has high interest to make more 3D printed parts, primarily due to the supply chain issues that have become a major bottleneck,” Bredael said. “When the Marines order a new vehicle, they want as many 3D printed parts on it as possible and the entire digital thread included. This enables them to print spares on-demand instead of relying on the OEM.” Bredael further elaborated on the importance of a data package and identified other industrial manufacturers requesting the same type of information for commercial applications.
Red: Well, if green means go, then you can probably guess what the red bin indicates. Red bin parts are not approved for production through AM means. However, commanders have the authority to print and use red bin parts as a temporary solution when mission success is in jeopardy and a proper risk assessment is completed. As the AM environment continues to evolve, red bin parts may be reassessed for approval.
The Intersection Between Defense and Industry: The United States Armed Forces measures itself on mission success and has authorized the use of 3D printing to increase operational readiness and warfighter innovation. Qualification of parts will continue to be a major barrier or opportunity depending on your perspective. While risk is defined differently, what can commercial manufacturers or 3DP OEMs take away from the military’s approach to additive manufacturing qualification?
- The Digital Thread: As Bredael mentioned, defense and commercial manufacturers want more 3D printed parts on their equipment so it’s easier to fabricate them on-demand. This reduces inventory challenges, eliminates long-lead times, and increases overall resiliency. Will defense contractors and suppliers proactively provide data packages and how will this impact IP ownership? To me, this sounds like a new business opportunity.
- “Figure It Out” Approach: The Marine Corps authorized the use of 3DP equipment beyond the research environment because it trusted their people to find innovative solutions on the ground and in real time. No one has the training, figure it out. Many commercial OEMs have research and development facilities filled with 3D printing equipment, but how many of them have the patience or funding to implement it on the ground level? Sometimes the most innovative solutions are to problems that were never on the radar to begin with.
- Time vs. Cost: For the military, cost avoidance continues to be a factor but it’s nowhere near as important as reducing equipment downtime with faster parts in hand. For commercial, it’s always been a delicate balance, typically tipping the scale in favor of cheaper parts. In our ultra-competitive environment, sometimes (and incorrectly) referred to as a battlefield, will commercial companies begin to implement a similar approach? Speed > Cost?
Learn more about 3D printing and the Marine Corps Systems Command at www.marcorsyscom.marines.mil.
Special thanks to Gary Bredael, Howie Marotto, and Michael Pecota