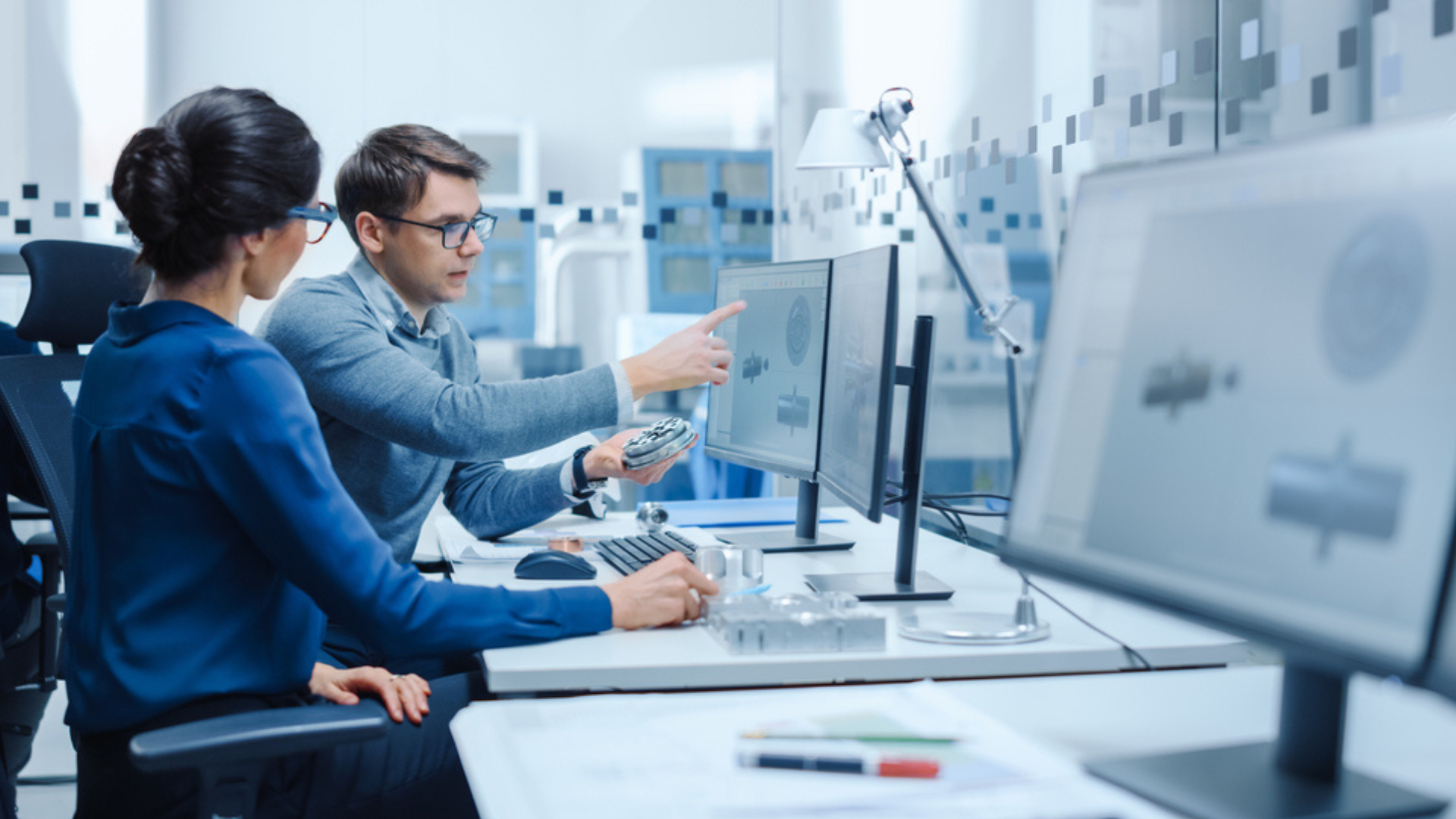
As the additive manufacturing (AM) industry turns 40, it is evident that this technology is being accepted into more mainstream manufacturing activities and supply chains. Yet the need for trained workforce in the discipline seems to be mostly unmet, despite an overall increase in college courses, industry certifications and accredited degrees.
Of course, a shortage in skilled manufacturing labor is not a new story: The National Association of Manufacturers Q3 2022 outlook survey noted that 76.1% of manufacturers cited attracting and retaining a quality workforce as their biggest challenge (just slightly behind supply chain issues as the biggest concern). Additive manufacturing, as a quite specialist sub-category, is no different and perhaps an even bigger challenge.
20 years ago, there were very few AM programs at colleges and universities, no industry certifications, and no degrees. The pioneers in AM were just figuring it out as they went along: Engineers with a curiosity about it; innovators working to develop new applications and new AM technologies. There was no course guide or syllabus for them to use. As these self-taught AM experts emerged, they shared their experiences at events like AMUG and knowledge was built through non-formal channels, discussions and presentations. But this model did not allow for a workforce to be built at scale, and neither could it support the rapidly growing AM market with hundreds of new machines, and even more new materials.
Fast forward to 2022 and there are now multiple university programs for AM worldwide, with Master’s and Graduate degrees available at many universities. In recent years industry associations such as ASME, SME and ASTM have developed certifications in the field for continuing education. America Makes has delivered its Education and Workforce Development (EWD) plan which shares resources for educators, and manufacturers. European and Australian universities are pushing ahead with advanced degrees in AM. Accelerated Training in Defense Manufacturing (ATDM), sponsored by the DOD, recently opened up a new training center in Virginia offering free AM, welding and CNC skills training in a 16 week course.
So what’s the hold up? AM skills training and courses are more widely available compared to previous decades. America Makes states that its EWD program has trained or engaged over 65,000 people. But there still seems to be a dislocation between available courses and what the industry needs, and confusion about how to get there.
The confusion seems to start as to what AM courses are available and just what is needed for workers to be successful in the field. In the past, routes into manufacturing were either trade skills or an engineering degree.
Barbara Humpton, CEO of Siemens commented in a recent online discussion with Tom Costabile, CEO, ASME:
“What used to be needed in this [engineering] environment was a four-year degree,” she commented. “What we’ve learned is as we hire for say, trades, it turns out the skills you need can be learned both with some educational background and then some hands-on training. Put that together in a two-year college, a community college experience, and they’re ready for a job. And this idea that there are multiple pathways is really exciting because now we can talk to people at any point in their lives.”
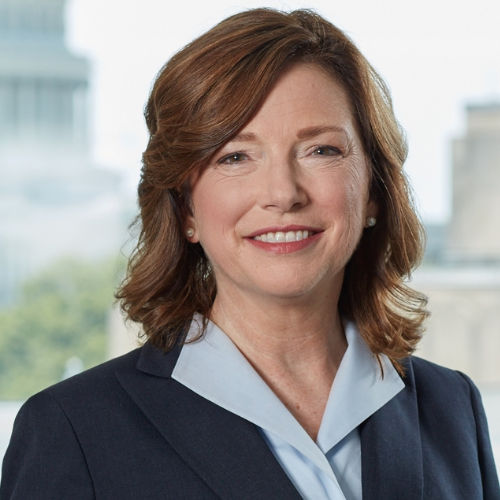
But for AM there is no single route, and new routes are constantly being developed, either by companies or industry bodies. The availability of the internet, YouTube videos and so on, make those paths less clear although accessibility is far higher than ever before.
Josh Cramer of America Makes said:
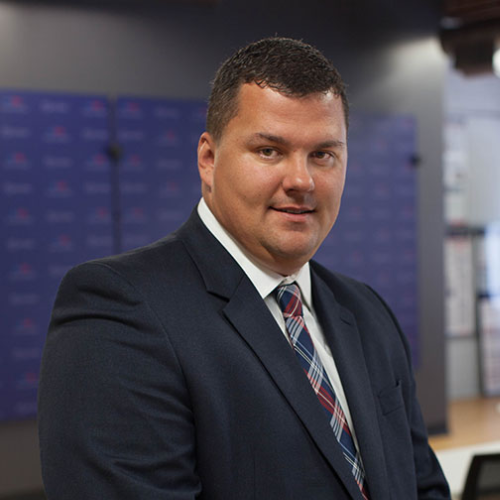
“There are opportunities to really seek pathways to AM beyond school and leverage things like work and earn opportunities, how they train while they’re at a company, and where are those opportunities to on ramp quickly with a company,” he said. “We are focusing some new programs around micro-learning, so taking what used to be long courses, cutting them up in bite size pieces so that we have an opportunity to capture and validate, so we’re not losing folks anywhere in that system as well.”
While at the same time, being more creative in curricula for AM might also be part of the way forward.
“We’re definitely seeing an increase in interest from students, which then requires curriculum design change for people to really educate this workforce in what they need to do,” said Dr Ashley Huderson, ASME. “And so I think from a curriculum standpoint, we are seeing the adaptation of exploratory work and creative topics, and allowing the students to move in a space that may not be bound by some of the traditional engineering ways of thinking or some of the processes.”
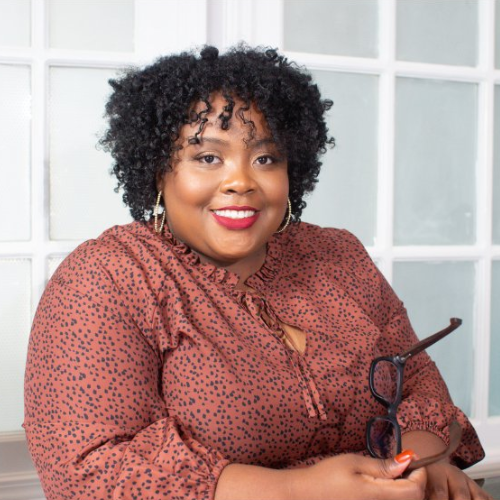
The development of advanced applications in AM, such as medical and dental, also raise questions about required knowledge. Is it better to be a dentist and then move into additive manufacturing? Or an additive engineer moving into the dental space? No one seems to have a definitive answer.
Industry insider, Varun Bhatia from Medtronic commented in a recent panel.
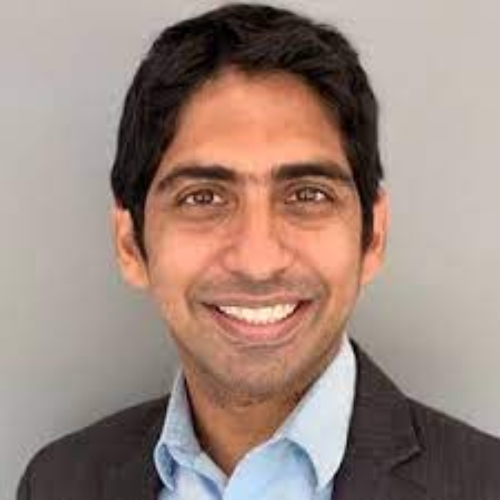
“So [engineers] don’t necessarily need to have a medical background, although it helps,” he said. “It helps to have at least some medical context, but I don’t think it’s a necessity. It goes back to the whole aptitude. As a mechanical engineer you already have the skills, how do you apply that to specific applications?”
But Sarah Rimini from Ricoh sees a different point of view too.
“If you want it, go out and do it, and grow your knowledge,” she said. “I started as an MRI tech at a hospital back in 2006 and grew into 3D imaging and 3D printing and eventually last May I graduated with my Masters of engineering through Penn State in additive manufacturing and design. I think the biggest thing about finding someone that could be able to run these programs is not just looking for a particular background but looking for a thirst for knowledge and wanting to be able to excel in the field and grow, not just from their background but add into it so everything is all encompassing.”
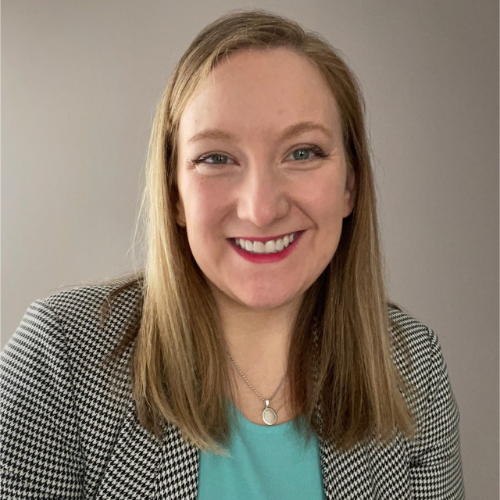
However, as the AM market continues to grow, with new technologies, methodologies and materials developing quickly, it is also becoming clear that interdisciplinary skills and now, more importantly, interdisciplinary teams are required, adding to the skills gap and making qualification yet more complex.
Lisa Block from Hybrid Manufacturing, commented.
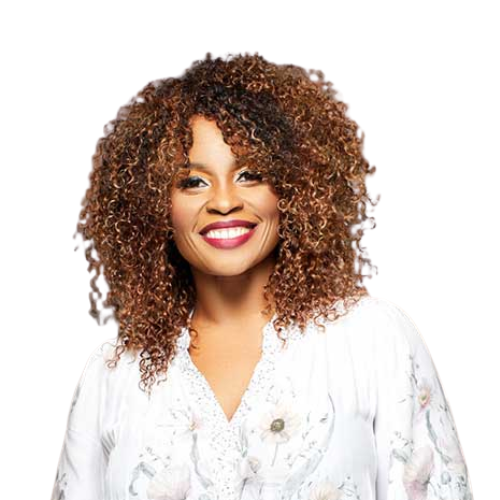
“I need the traditional manufacturer and I need the traditional additive person and I need there to be a mashup and a mating of those skill sets together to make a hybrid manufacturing process work,” she explained. “I need a traditional machinist that’s been at it for 30 years, has learned how to make parts efficiently with subtractive. I need an additive professional that has knowledge of metallurgy and 3D printing and multiple 3D printing processes and I need them to work together so that our systems and our processes work effectively.”
Where in the early 2000s and even 2010s, a single AM engineer would handle everything, the job itself is becoming too big and too varied for just one individual. As AM shifts into industrial production, typical AM centers are now in need of teams of experts.
“So we’re not seeing one expert in a company anymore or even two,” said Cramer. “We’re starting to see where we have these diversified roles, anywhere from design for additive, to moving into production and production technicians, engineers, as well as also looking at folks that are maintaining equipment and post-processing parts.”
So where is this all leading? Those aspiring to excel at AM definitely have a number of choices for building skills, from self-directed online learning, through to skills training at local community colleges, hands-on at companies, and all the way through to post-graduate work at some universities.
While the building blocks for training an AM workforce at scale seem to be getting into place, training remains uncoordinated: Each industry body in every different country adheres to different standards for AM certification. College courses can be vastly different in scope and technologies used. Maybe some older courses are already outdated by the rise of newer AM platforms, software and materials. And employers need to be able to understand and assess what courses deliver to be able to hire with confidence. Until that coordination can occur, workforce development for AM will remain a little wild and quite inconsistent.
If you know someone new to additive manufacturing, a good place to start is the Additive Manufacturing Basics.