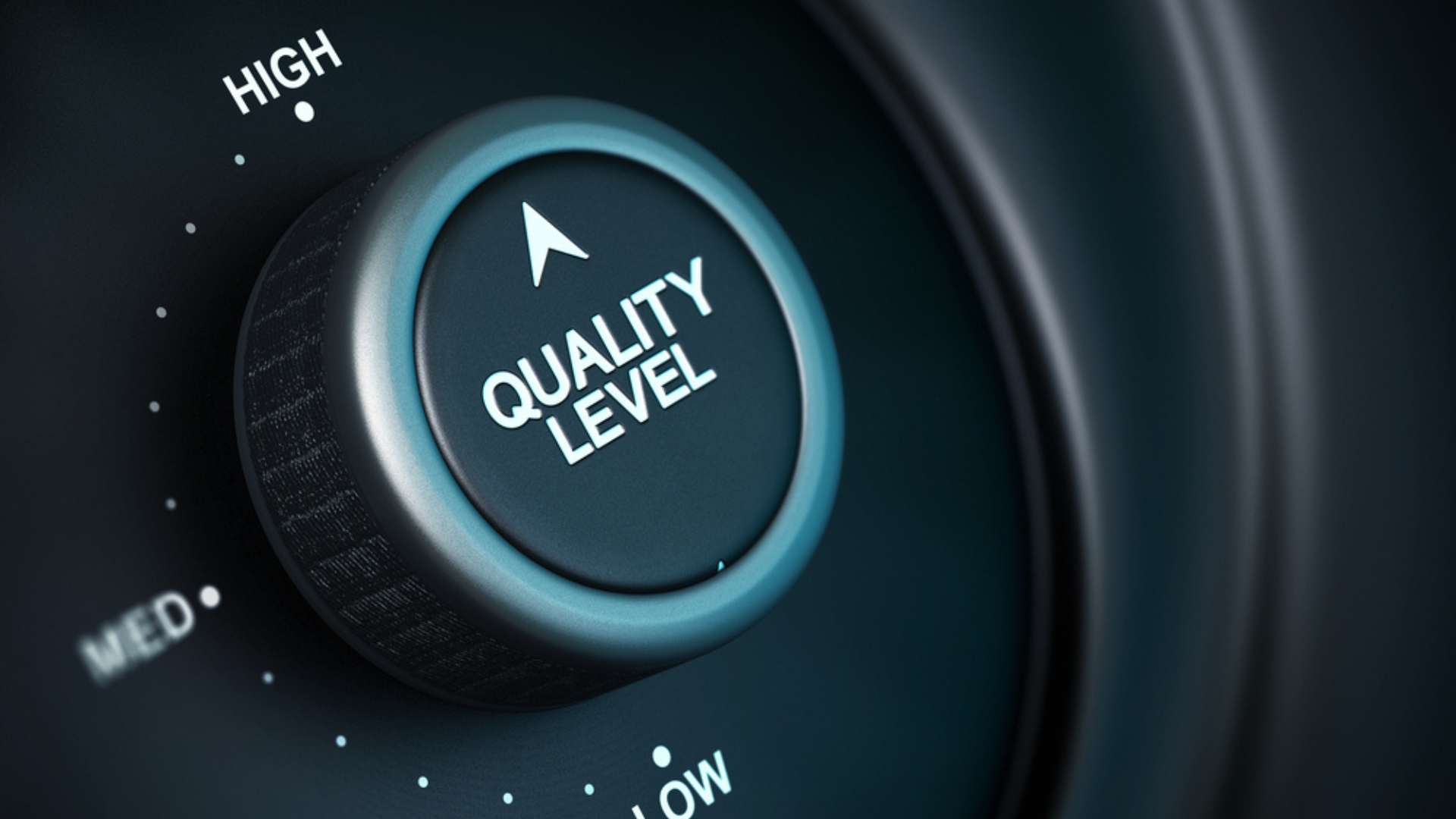
When new to medical device development and manufacturing one daunting aspect can be developing a Quality Management System (QMS). Many industries use QMS or similar principals, so why does it seem so much harder to apply them to medical device quality systems driven by regulations?
A hint can be found in the pre-amble to the US FDA Quality System regulation which states (emphasis added):
Because this regulation must apply to so many different types of devices, the regulation does not prescribe in detail how a manufacturer must produce a specific device. Rather, the regulation provides the framework that all manufacturers must follow by requiring that manufacturers develop and follow procedures and fill in the details that are appropriate to a given device according to the current state-of-the-art manufacturing for that specific device.1
In other words, the regulation is intentionally written to allow for flexibility because it must apply to all medical device types – from BAND-AIDS to Left Ventricular Assist Devices (LVADS). You will not find step-by-step detailed instructions for a specific device type there!
However, if you look at each of the regulation subparts and step back to think about the aspects of a good business, you will find almost all the pieces needed to run a business are also present in the QMS regulation. When you begin thinking about implementing a quality management system, you may already be doing the essentials, and the missing step might be documenting it appropriately. It is better and more efficient to think through something you do many times and write down how to do it, rather than using additional resources to re-think a common process over and over again. Now you have a Standard Operating Procedure!
Looking at the US FDA regulation, we can find each subpart matches with questions an investor or business partner may ask:
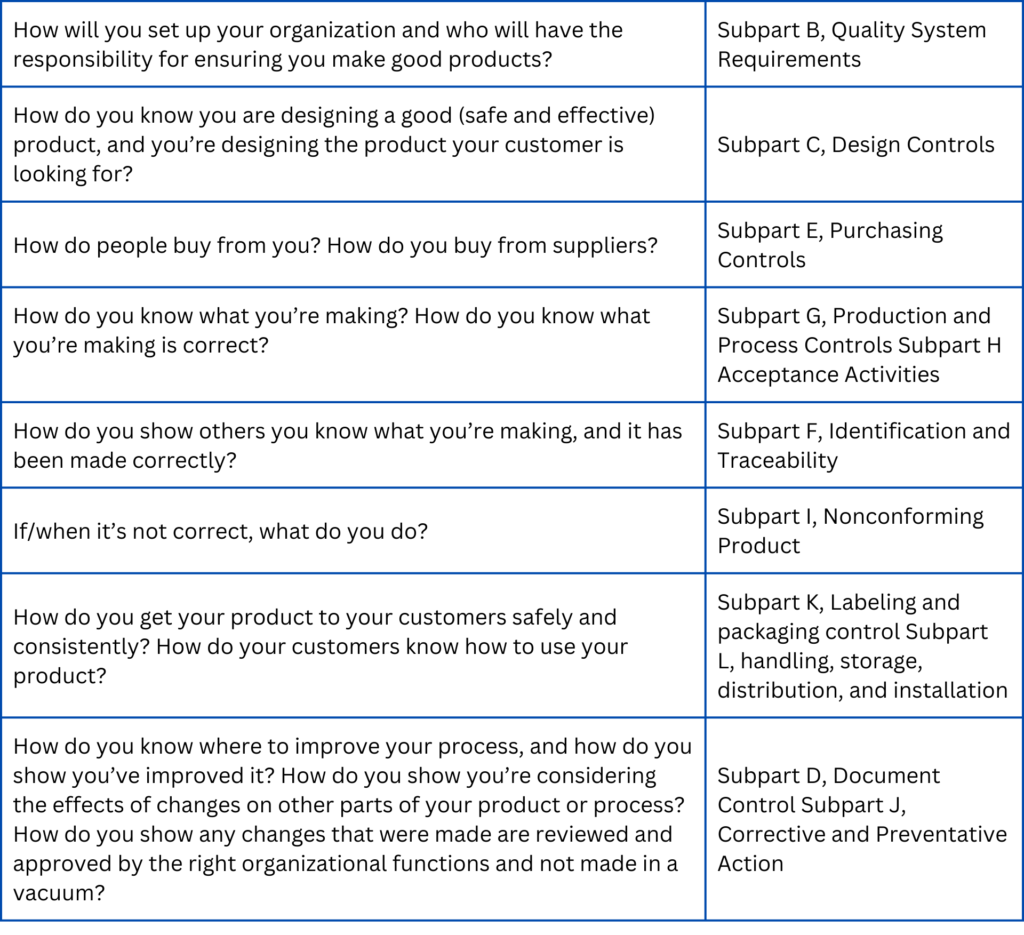
From this vantage point, the QMS could be considered a roadmap of how to build a medical device business. Intentionally applied typical business principles make significant progress towards being compliant with FDA regulation. Don’t consider quality management a litany of boxes to be checked in order to be compliant. Instead, use it to help you create a safe product, documented in a way that a new employee could follow as well as understand how the product was created and the ‘why’ behind the decisions that were made.
Quality is an important aspect of any business, but in medical device development and manufacturing it is critical since these products could be tasked with saving someone’s life. Regulatory bodies clearly reflect this importance in management’s direct responsibility for the quality of products being made. The following image demonstrates the importance of quality with executive management at the core. Everyone in the organization is accountable to the quality system.
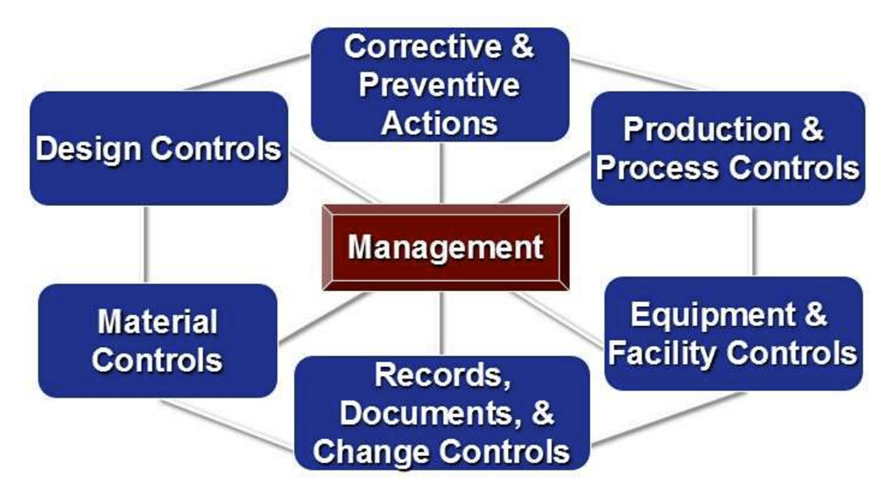
High Level Tips to Develop a Quality Management System
It’s clear why a QMS is important and good business sense, but what should be considered when developing one? While it does take a significant number of resources to fully implement a QMS, it doesn’t have to be right-out-of-the-box perfect. Regulatory bodies will focus more on whether procedures are relevant and followed than if they are perfect. Plus, a quality system is not fixed – you can change it; But if changes are made, be sure to document why it was changed, if/how it effects other parts of your system, and if all relevant organizational functions agree (i.e., Change Control).
Most people want the Best of something, and the Best is typically thought of as the latest features and greatest technical specifications. But similar to that complicated digital camera collecting dust on the shelf versus the one in your pocket, the best quality system is the one that is used. Don’t make it so complex that no one is going to use it. The quality system will encompass day-to-day workflow, so the people who do the day-to-day work are valuable stakeholders and contributors to its development.
The complexity of the device or technology as well as the sophistication of the relevant manufacturing process will dictate how extensive the quality system needs to be – band-aid versus LVADs. The size of the manufacturing facility and the number of different products or product lines that are being produced can also influence the scope of an organization’s quality system.
This brings us to objective evidence: if you didn’t write it down it didn’t happen.
The basic idea is to document the following three steps:
- What are you going to do, and why are you doing it
- Do it
- Objective evidence that it was completed as written, or an explanation of why it still makes sense as objective evidence if it wasn’t completed exactly as written.
Some examples of these three steps are: for testing (1) protocol, (2) test, (3) report; for manufacturing operations (1) work instruction, (2) manufacturing to the work instruction, (3) manufacturing traveler and device history record.
Where should we begin?
A great place to start is reading the regulation and determining how it applies to the product being designed and produced. You can start with one large document and leave placeholders for sections that do not yet apply. For example, you likely won’t have Corrective Actions and Preventative Actions (CAPA) until a product has been manufactured. The most important thing is to follow what the procedures say you’re going to do and document that you’re following it. At this beginning stage it’s also important to remember you can change the procedures if you document why it’s changed and if you determine and can accept the impact on other parts of the process.
There are several groups that can provide templates or a digital quality management system in a “box”. If you buy templates, make sure you edit them to your context – generic to specific – make it your own! If you hire people to help you, don’t hire someone who sits in a different city and writes it alone – expect to be involved in the process and get input from the people doing the job.
Lastly, the quality system needs to be effective, which means you also have to train to it. Similar to the New Year’s Resolution of exercising, it doesn’t help unless you actually train. When you exercise repeatedly it becomes a habit and eventually your routine becomes so embedded in day-to-day life that you can’t imagine living without it – it makes everything else work better. Each time there is a question, model this repetition by looking to the procedure to guide how to perform a task, like product development. As a bonus, working the quality system will later help in an inspection when muscle memory will trigger employees to automatically walk an inspector through the procedure to answer their question.
Overall, a QMS helps document and provide objective evidence that the products being designed, developed, and manufactured are safe. It enables an organization to gather information along the entire product lifecycle to demonstrate that these devices are safe and that they are always safe because the organization is consistently following its processes. Producing safe products is a fundamental goal of medical device manufacturers and QMS is a critical tool to meet that goal.
Other Resources
- 21 CFR 820: Quality System Regulations
- ISO 13485: Medical Devices – Quality Management Systems
- ISO 14971: Medical Devices – Application of Risk Management
- CDRH Learn > Industry Basics Workshop Series
- Technical Considerations for Additive Manufactured Medical Devices
- 3D Printing Medical Devices at the Point of Care: Discussion Paper
- Process Verification & Validation for Medical Devices Using Additive Manufacturing
1 Medical Devices; Current Good Manufacturing Practice (CGMP) Final Rule; Quality System Regulation, Pre-amble, pg. 52603