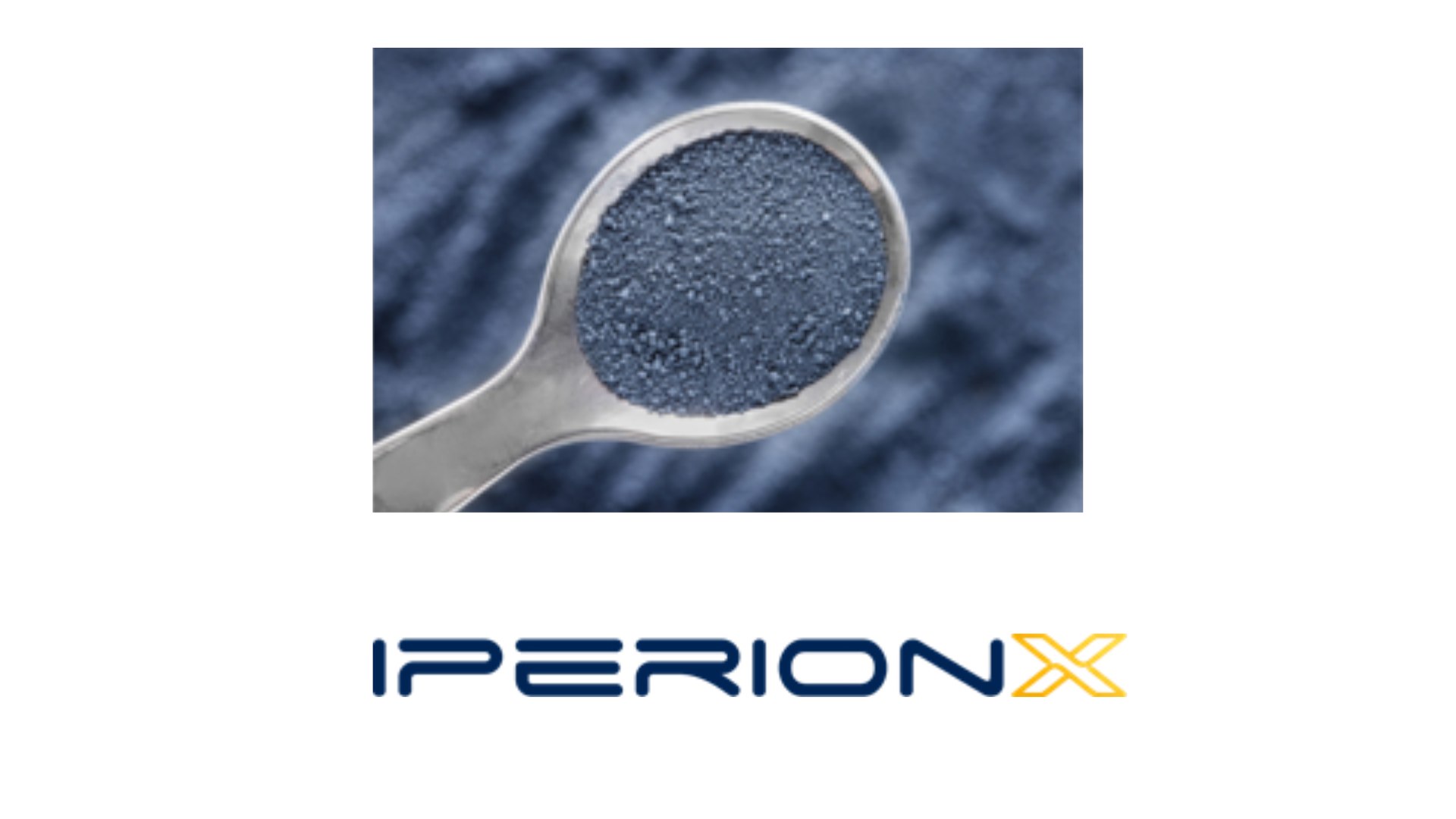
CHARLOTTE, N.C./January 17, 2023 —IperionX won the U.S. Department of Defense’s National Security Innovation Network (“NSIN”) Air Force Research Laboratory (“AFRL”) Grand Challenge contract. As a result, IperionX will be eligible to produce titanium recycling powders from scrap materials and rejuvenate used or out-of-specification titanium powder for the AFRL. The Grand Challenge is a competitive challenge program hosted by the U.S. Department of Defense’s National Security Innovation Network.
Winning this Grand Challenge, against a field of leading titanium industry participants, is an important validation of IperionX’s patented technologies to produce circular, low-carbon and lower cost titanium metal from 100% recycled titanium scrap or out-of-specification titanium powder feedstocks.
The U.S. Air Force and U.S. Department of Defense are accelerating the use of additive manufacturing to reduce long lead cycle times and to produce large volumes of complex parts for advanced weapons systems.
Only 20%-40% of titanium powder used in additive manufacturing ends up in fabricated parts. Titanium metal powders are typically reused only a limited number of times before the quality is compromised by elevated contaminant levels or inferior powder morphology. Out-of-specification titanium powders increase the probability of defects and jeopardize the structural integrity of additively manufactured components.
Titanium metal produced by the current “Kroll Process” is high carbon, energy intensive and expensive. Leading companies across the defense, automotive, consumer electronics and luxury goods sectors want to source low carbon, low-cost titanium from traceable recycled sources. IperionX’s patented technologies offer a pathway to significantly lower cost, and lower carbon, titanium metal powders for titanium components in these industries.
The patented technologies were developed by Dr. Zak Fang, an American Professor of Metallurgical Engineering at the University of Utah, and uniquely position IperionX to upcycle a wide variety of low-grade, high oxygen content titanium scrap which has historically been downcycled to lower value markets. IperionX is able to achieve greater yields of nearly 100% from low-grade scrap without the need for blending the scrap with high-grade primary metal.
Winning the Grand Challenge also complements IperionX’s project with Materials Resources, LLC to qualify titanium alloy powders for the U.S. Navy and test titanium flight critical metal replacement components for the U.S. Department of Defense.
The winner of the Grand Challenge is eligible for a contract award up to $500,000 across four phases, with IperionX successfully completing Phase 1, and will complete Phases 2 – 4 as part of routine production operations at its Titanium Pilot Facility in Utah.
Anastasios (Taso) Arima, IperionX CEO said: “Winning the Grand Challenge is an outstanding endorsement of IperionX’s patented titanium technologies. Our leading technologies can efficiently recycle titanium scrap metal and metal powders at lower cost than existing processes, and we look forward to working closely with NSIN, AFRL and other Department of Defense agencies to qualify and rapidly deploy the use of circular titanium metal across key defense platforms.”
Dr. Calvin Mikler, Materials Engineer, AFRL said: “The AFRL team is excited to work with IperionX on the next phase of the titanium recyclability Grand Challenge. IperionX seemed to really understand the purpose of the Grand Challenge and pitched a unique strategy to deoxygenate and rejuvenate used titanium powders and scrap materials back into powder suitable for additive manufacturing of aerospace-quality parts. We can’t wait to see the results of all the hard work yet to come!”
Contract Details: The winner of the Grand Challenge is eligible for a contract award up to $500,000 across four phases:
- Phase 1 ($125,000): White paper submission and pitch day
- Phase 2 ($125,000): Generation of a precursor titanium feedstock
- Phase 3 ($225,000): Titanium powder production
- Phase 4 ($25,000): Build, test, and analyze cost savings for the overall concept
- IperionX has successfully completed the requirements for Phase 1, and currently undertakes Phases 2 to 4 at its operational titanium pilot facility in Salt Lake City, Utah.