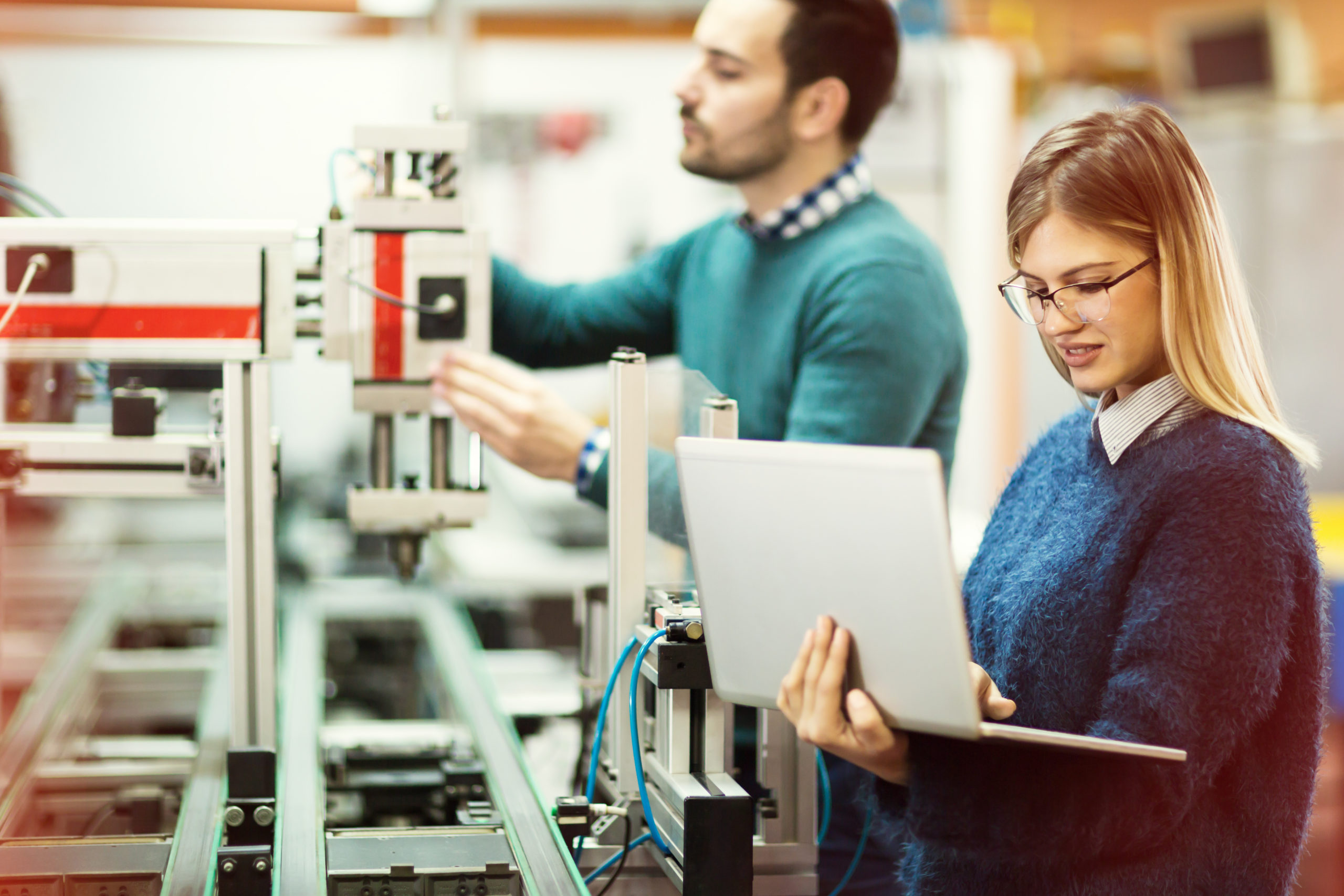
As additive manufacturing (AM) continues to grow with new companies and industrial applications expanding the market, more workers are needed to meet the demand. For AM, companies are looking to hire people in engineering, sales, operations, service, and other jobs to keep companies running. Many workers entering the industry come from academia. The 2022 AM Salary Survey by Alexander Daniels Global found that 22% of respondents had no professional experience prior to AM. It is assumed a large portion of those come straight from academia. With an ever-growing number of opportunities, it may seem like AM is an easy option for anyone with an engineering or technical degree. The challenge for the manufacturing industry is engineers alone will not fill the available jobs.
After the supply chain challenges caused by COVID-19, many companies are looking to simplify their value stream and bring manufacturing back to the U.S. Immigration and international work visas have been reduced according to research by the CATO Institute. The COVID-19 pandemic caused more than 1 million deaths in the U.S., of which more than 25% were of working age (18 – 65 years old) and it prompted many people to retire early.
Regardless of the cause, the U.S. manufacturing sector is facing a workforce shortage, which will continue to grow. The AM community is not exempt from this. Over the past few decades, many individuals and organizations, including parents and academic institutions, have signaled that the way to get into manufacturing is through science, technology, engineering, and mathematics (STEM) programs. However, engineers and scientists alone will not fill the vast number of open roles. We need people running machines, overseeing shop floors, and bringing in a diverse background to solve the problems of tomorrow.
Research by YouScience, showed that more high school students were interested in engineering than had the aptitude to succeed in the field. This is likely due to the idea that becoming an engineer will provide a lifelong, well-paying job, which is not inherently false. Conversely, students have 3x the ability to succeed in advanced manufacturing compared to their interest in the field. This is a marketing and perception problem. I conducted an informal study during an 8th grade career fair in Denver, Colorado. Students were asked what they thought about when they heard the word manufacturing. They overwhelmingly said factories for cars. As a society, we need to change the perception of manufacturing from dull, dirty, and dangerous to something more vibrant.
Engineers will continue to provide a backbone of how to create a safe and reliable product, yet they alone cannot fill the workforce shortage. In 2020, 199,790 engineering degrees were awarded in the U.S. according to DATAUSA, created by Deloitte and Datawheel. If extrapolated to 2030, these individuals would nearly fill the 2.1 million worker shortage forecasted by Deloitte and the Manufacturing Institute. The problem is many people who graduate with a STEM degree do not work in STEM. According to a U.S. Bureau of Labor Statistics (U.S. BLS) study from 2014, only 36.6% of STEM graduates work in STEM or STEM-related occupations. To fill the gap, companies should look at how to lower barriers to entry into their company and train internally.
The leaders for creating the change within an organization should be middle management. These individuals have power within the organization and are the future leaders of the industry. Middle management needs to get buy-in from top-level executives to shop-floor employees on new ways to grow their workforce, knowing that hiring engineers will not be the end-all solution. For many roles in a company, training can be done on the job. If job descriptions continue to have extensive experience as a requirement, the only people to hire will be from the competition, which does not help the workforce shortage challenge.
Beyond attracting a new labor market, companies should focus on how to keep individuals within their company. In 2022, manufacturing had an average tenure of 5.2 years, which is one of the highest across all sectors according to the U.S. BLS. Studies from Alexander Daniels Global, The Manufacturing Institute, McKinsey, and Guild Education all show that the leading reasons for people to choose and stay with a job are compensation, career growth, meaning, and community. These retention drivers should not be surprising, yet many companies stop at compensation, or hold other factors on a pedestal to pay their employees less. Management should look at how they meet all four factors for individual employees.
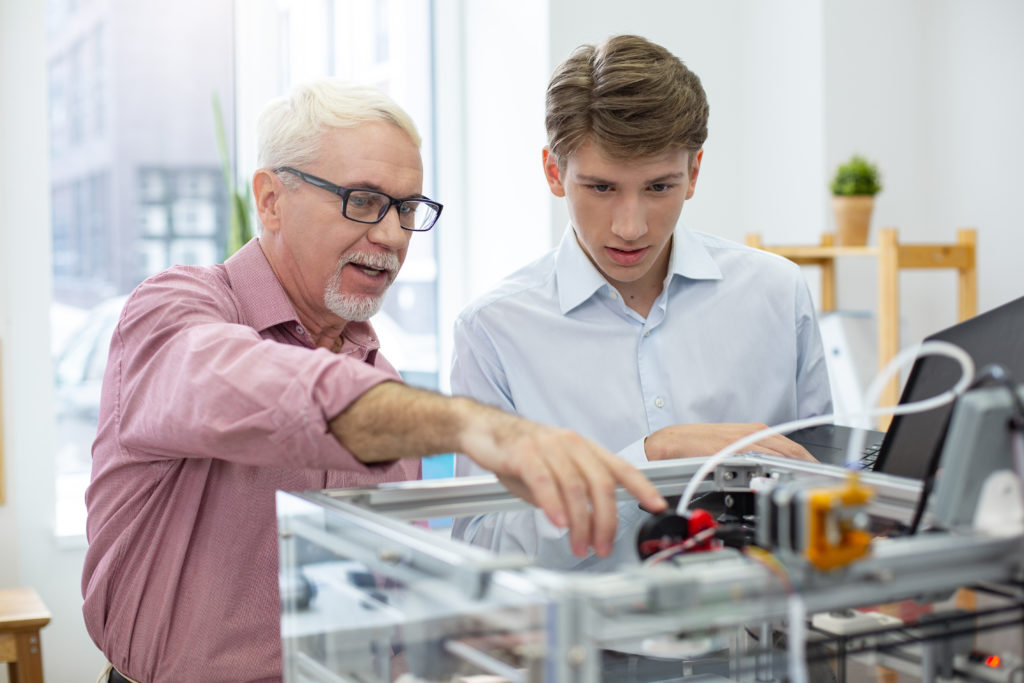
Reverse mentoring can help promote career development, meaning, and community within an organization. Having a mentor be the younger employee and the mentee be a senior level executive, both benefit from generational sharing of information. It can be challenging to set up and would require buy-in from all parties. You can find many resources online on how to organize it well, yet a good starting point is a short video from Patrice Gordon. Reverse mentoring is important because you can empower everyone from entry-level roles to careered executives. Additionally, figures vary, yet it is well considered that a large portion of the manufacturing workforce will reach retirement age in the next 5-10 years. Reverse mentoring can help disseminate information and create future leaders.
Engineers can be valuable to any manufacturing company, yet they alone will not solve our workforce shortage. Opening job opportunities to those without a formal degree and supporting individuals will help your organization. With new employees, especially within Gen Z, the factors stated earlier are key for them to join and stay at your company. As an industry, we need to come together to create change. Middle management is the best tactical approach, yet everyone in an organization can contribute to the positive change.