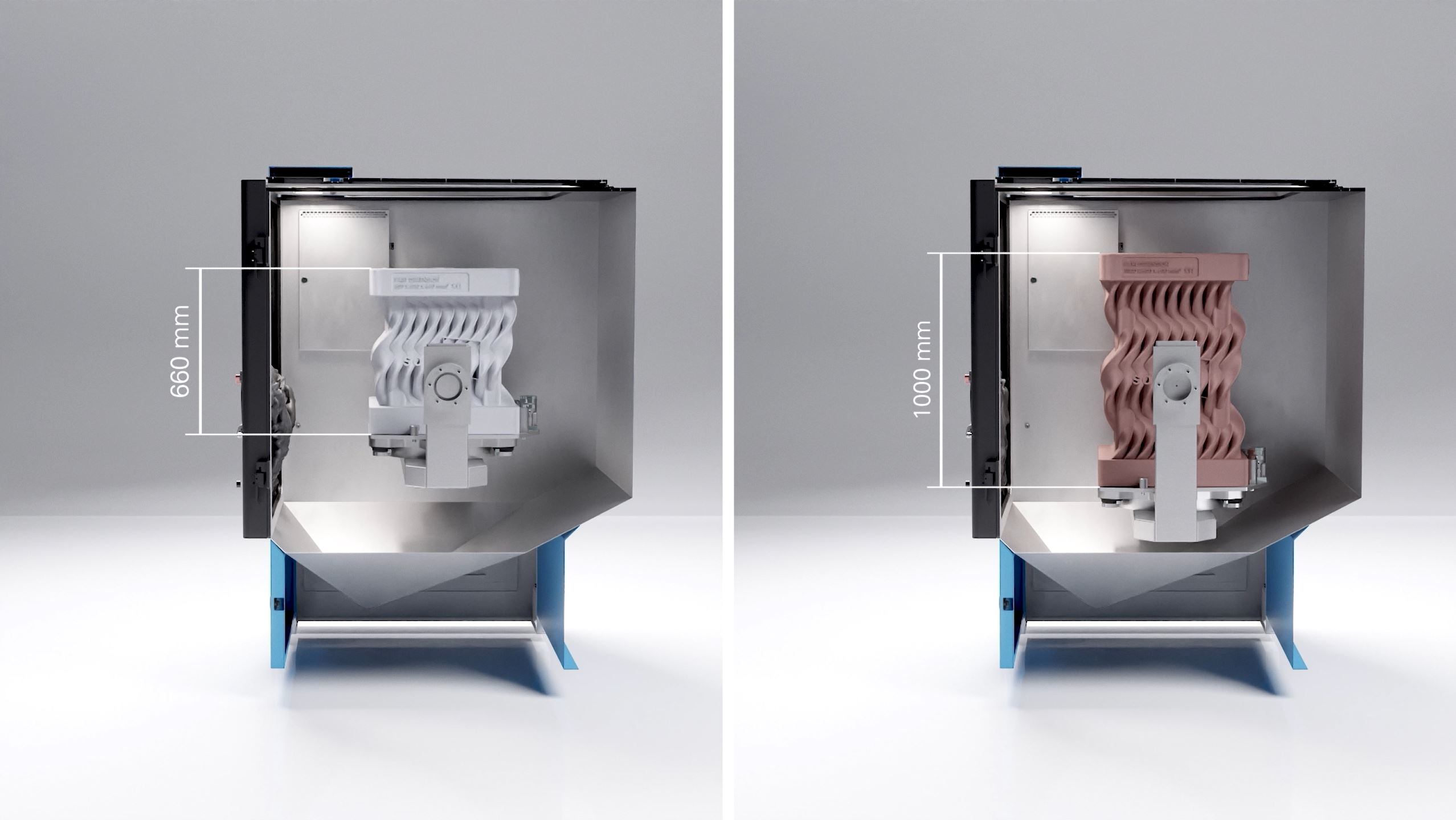
Solukon has equipped the SFM-AT1000-S with an optimized swivel arm for parts manufactured with the NXG XII 600 from SLM Solutions. An optional front-top-loading feature makes it easier to handle parts. Solukon will launch the special version of the SFM-AT1000-S at this year’s Rapid + TCT in Chicago.
Everyone’s talking about the NXG XII 600 from SLM Solutions, which has set the standard for the serial production of metal laser-melted parts. The machine is used to manufacture particularly large and heavy metal parts, which places high demands on industrial depowdering in turn. The SFM-AT1000-S from Solukon has been the depowdering system for such large and heavy parts since its launch in 2020. With a reinforced body and higher torque than the smaller SFM-AT800-S, it can safely and easily depowder parts weighing up to 800 kg. In close collaboration with SLM Solutions, Solukon has optimized the SFM-AT1000-S depowdering system with specific features for the NXG XII 600.
Short swivel arm for optimal center of gravity balance position
Taking into consideration the build plate, NXG XII 600 parts can reach sizes of 600 x 600 x 660 mm. This locates the center of gravity closer to the rotational axis of the swivel arm when they are placed in the Solukon SFM-AT1000-S. To reach an optimal center of gravity balance position, Solukon now offers a version of the SFM-AT1000-S with a short swivel arm. The short swivel arm also makes the part easier to access if users want to finish depowdering manually via the sealed glove ports.
New option: Front-top-loading for easier parts handling
It’s now even easier to load the SFM-AT1000-S, thanks to the pneumatic top. When the top opens, it folds up together with the upper door frame, such that the part can be inserted at turntable height with even more flexibility – it’s no longer necessary to ”thread in” the part from above. This enables particularly large and heavy parts to be lifted easily and conveniently into the system via crane by using lifting tools provided by SLM Solutions. Additionally, the front door can be opened wider than before, which makes loading and unloading bulky parts easier.
Both the front-top-loading and short swivel arm are currently available as options for the SFM-AT1000-S.
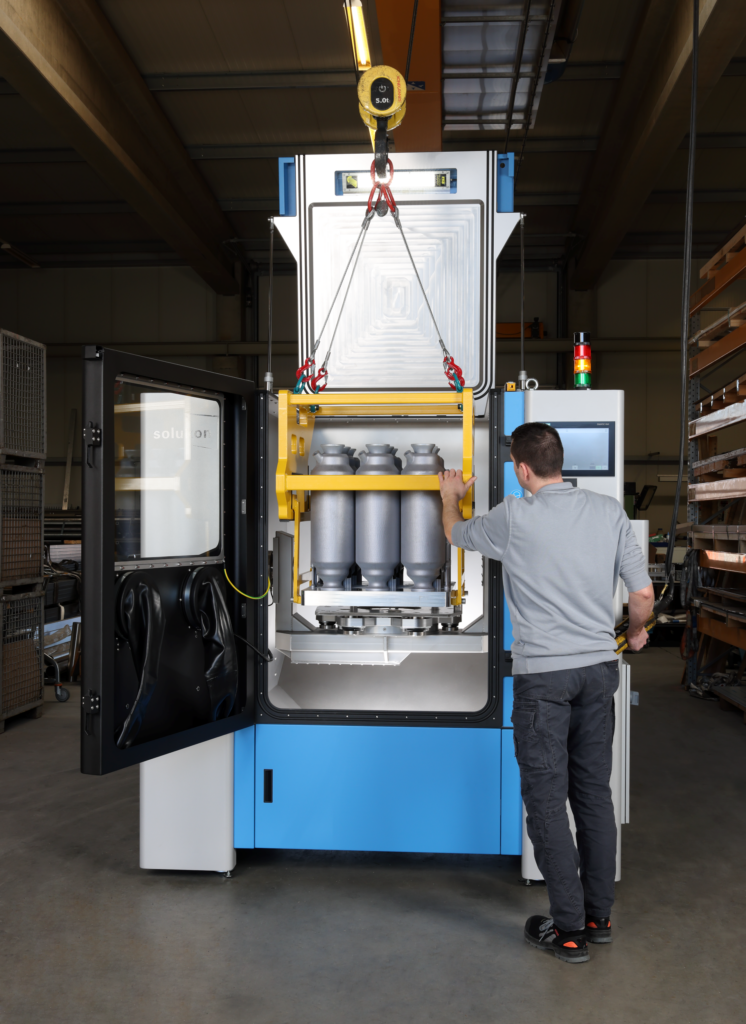
SFM-AT1000-S: Version comparison
The new option with a short swivel arm extends the compatibility of the SFM-AT1000-S depowdering system from Solukon. The table presents a comparison of both versions:
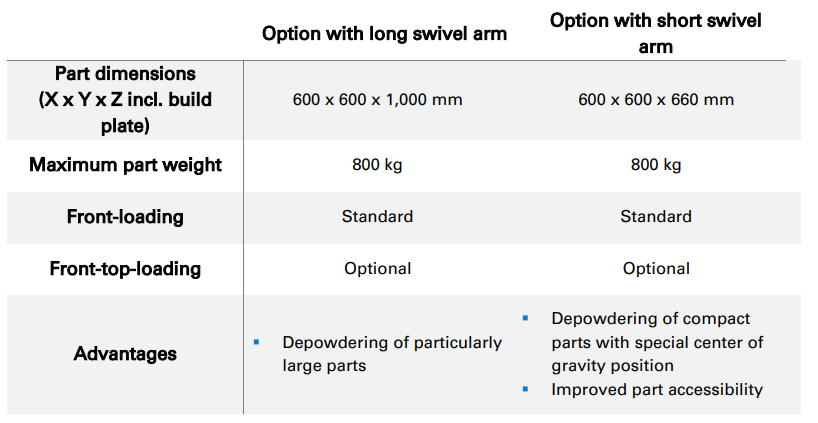
Solukon will launch the new version of the SFM-AT1000-S with front-top-loading and short arm at Rapid + TCT in Chicago, Illinois (May 2-4, 2023). The Solukon team looks forward to welcoming you at booth 1820.
SFM-AT1000-S: the leading depowdering system in the large-part sector
Like all Solukon systems, the SFM-AT1000-S is also based on the unique SPR® Smart Powder Recuperation Technology. Thanks to automated, programmable rotation around two axes and adjustable vibration, the Solukon systems remove all powder residues in a part’s internal channels in a reliable and fully automated process. The controlled flow of powder out of the most intricate channels and windings becomes more difficult when using materials like copper or aluminum, since these materials often get clogged inside internal channels. A new knocker was designed to address this problem. With finely adjustable mechanical knocks, clogged powder is loosened and can flow out in a controlled manner.
Digital features make the SFM-AT1000-S the most intelligent and best depowdering system on the large-parts market:
The Digital-Factory-Tool monitors the process and records all important data, including humidity, vibration, and gas consumption, and displays these values in a detailed quality report. The entire process is transparent and provides the data for qualification and certification in demanding serial production. With OPC UA, Solukon provides the interface for easy automation integration.
SPR-Pathfinder® software uses the CAD file of the complete build job to calculate the ideal motion sequence for removing powder from complex internal structures as quickly as possible. The software calculates the best possible motion sequence in conjunction with fluid simulation and an intelligent algorithm. Complex programming tasks that exceed spatial imagination are thus safely and conveniently automated.
SLM Solutions also acquires a new-generation SFM-AT1000-S
Both SLM Solution’s customers and the OEM from Lübeck trust Solukon’s expertise. After purchasing an SFM-AT800-S in 2021, SLM Solutions has an SFM-AT1000-S with front-toploading and short arm in its facility and uses it to reliably and quickly depowder NXG XII 600 parts.
Long-standing partnership between SLM Solutions and Solukon
With the development and purchase of the new Solukon SFM-AT1000-S specifically equipped for the NXG XII 600, Solukon and SLM Solutions have strengthened their longstanding partnership. “The NXG XII 600 is the gold standard in industrial 3D printing. We are also collaborating with the market leader in the area of depowdering, and are glad that Solukon is launching a depowdering solution that fits our system perfectly,” says Sebastian Feist, Product Manager for Factory Integration & Periphery from SLM Solutions.
Andreas Hartmann, Solukon’s CEO/CTO, is certain that his company is equipped to meet the trend of increasingly large parts: “The NXG XII 600 from SLM Solutions has set the entire large printer market in motion. We are happy that we can now offer the numerous NXG XII 600 users a customized depowdering system as well. Even larger parts measuring 1,500 millimeters, produced on an NXG XII 600E for example, or more on the Z-axis will inevitably require Solukon automated depowdering solutions. We are in ongoing discussion with manufacturers to ensure that we can always provide the right system. The SFM-AT1000-S for NXG XII 600 will not be the last Solukon system for the large-format printers.”
About Solukon
Solukon Maschinenbau GmbH is a German high-quality supplier of powder removal and processing systems for metal and polymer additive manufacturing. Founded in 2015 by Andreas Hartmann and Dominik Schmid, the company, located in Augsburg, has extensive experience in the development of AM systems and related peripheral equipment, and offers a full range of industrial powder processing systems. Since 2022 Solukon has been offering an intelligent software for automated depowdering of lasermelted metal parts as exclusive licensee, the SPR-Pathfinder®. Solukon products meet the highest functionality and safety standards and are approved for safe and reliable removal of tough-to-handle and reactive materials such as titanium and aluminum. Solukon is present on four continents. The systems are trusted by leading manufacturers of 3D-printing systems, like EOS, SLM Solutions and AMCM, by institutions like NASA and Cern as well as by companies like Siemens and Ariane Group.